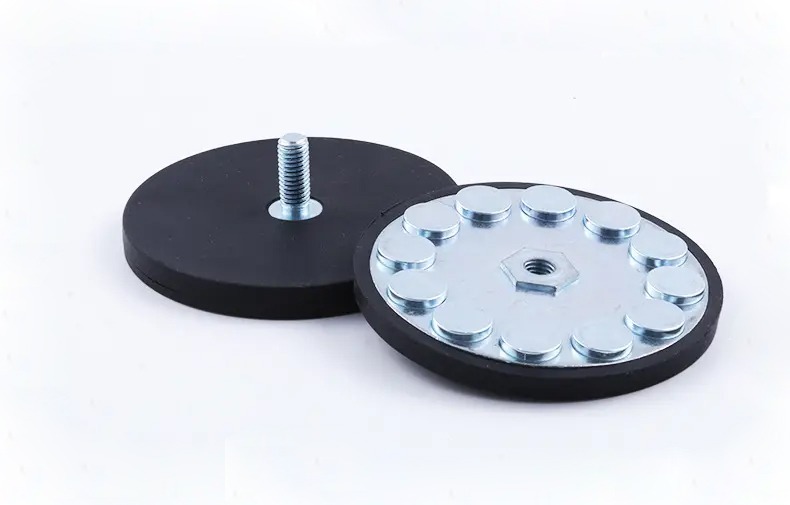
Overmolding is a process where two or more different materials are molded together to create a single product. It usually has a rigid plastic substrate covered with a flexible rubber-like thermoplastic elastomer (TPE) to provide a soft touch grip.
You need to provide 3D drawings, materials, colors, expected quantities, etc. Based on this information we will give you an accurate quote.
Depending on the complexity and size of the part, we usually take 4 to 6 weeks to complete the overmolding project.
Overmolding involves injection molding of two or more materials, commonly used to make non-slip handles, or to wrap certain parts (such as magnets) for collision avoidance. If your plastic parts have two or more materials, then over molding process is the ideal solution for you.
Yes, we provide the ability to create fully encapsulated magnets using overmolding process. we have more than 10 years of experience in insert molding magnets and overmolding magnets project.
Overmolding magnets refers to the process of encapsulating magnets with plastic through injection molding. In this process, a plastic material is injected into a mold cavity that contains the magnet, and the plastic then solidifies around the magnet, creating a secure and protective encapsulation.
There are many factors to consider magnets overmolding, first, magnet have two poles, magnetism must be considering, because of our mold is steel. second, is all the same poles at a place or different also need considering. third, magnetizing at injection molding before or after must be considering too.
Here is overmolding magnets steps: