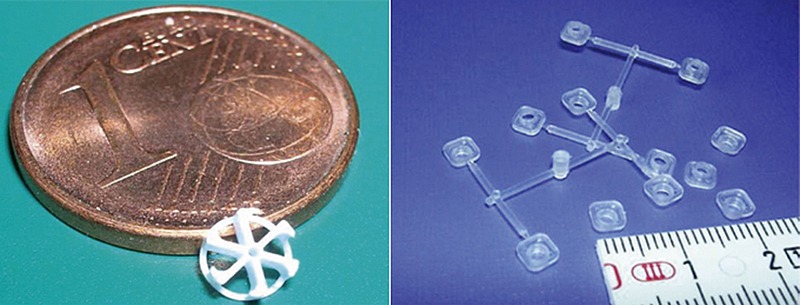
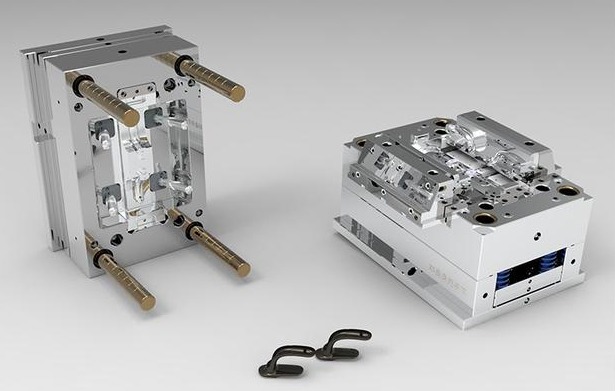
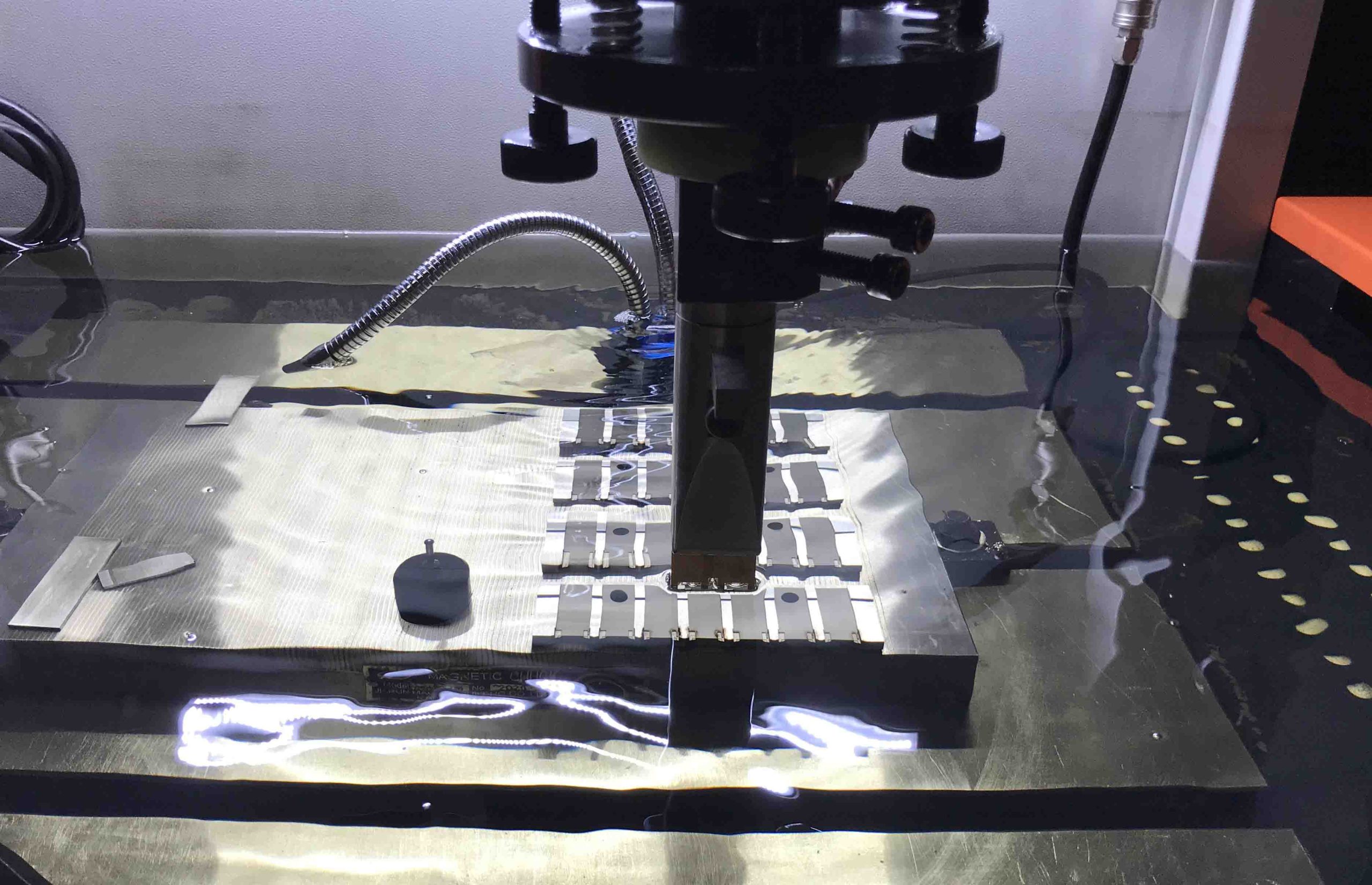
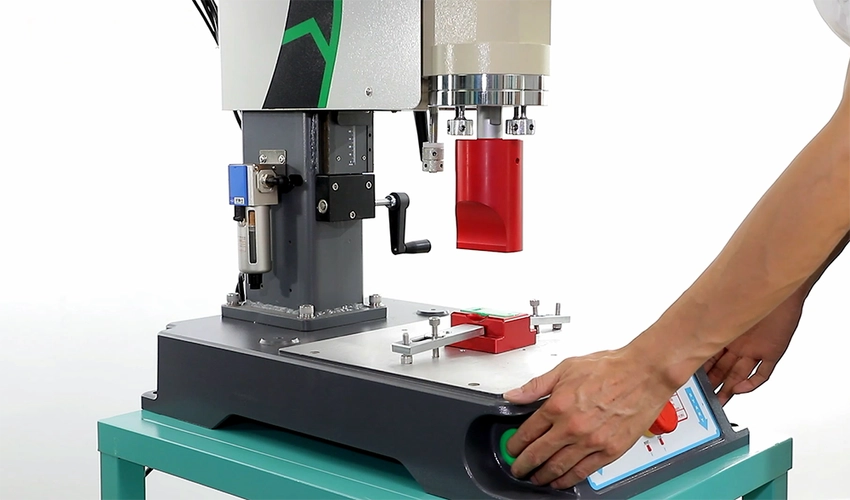
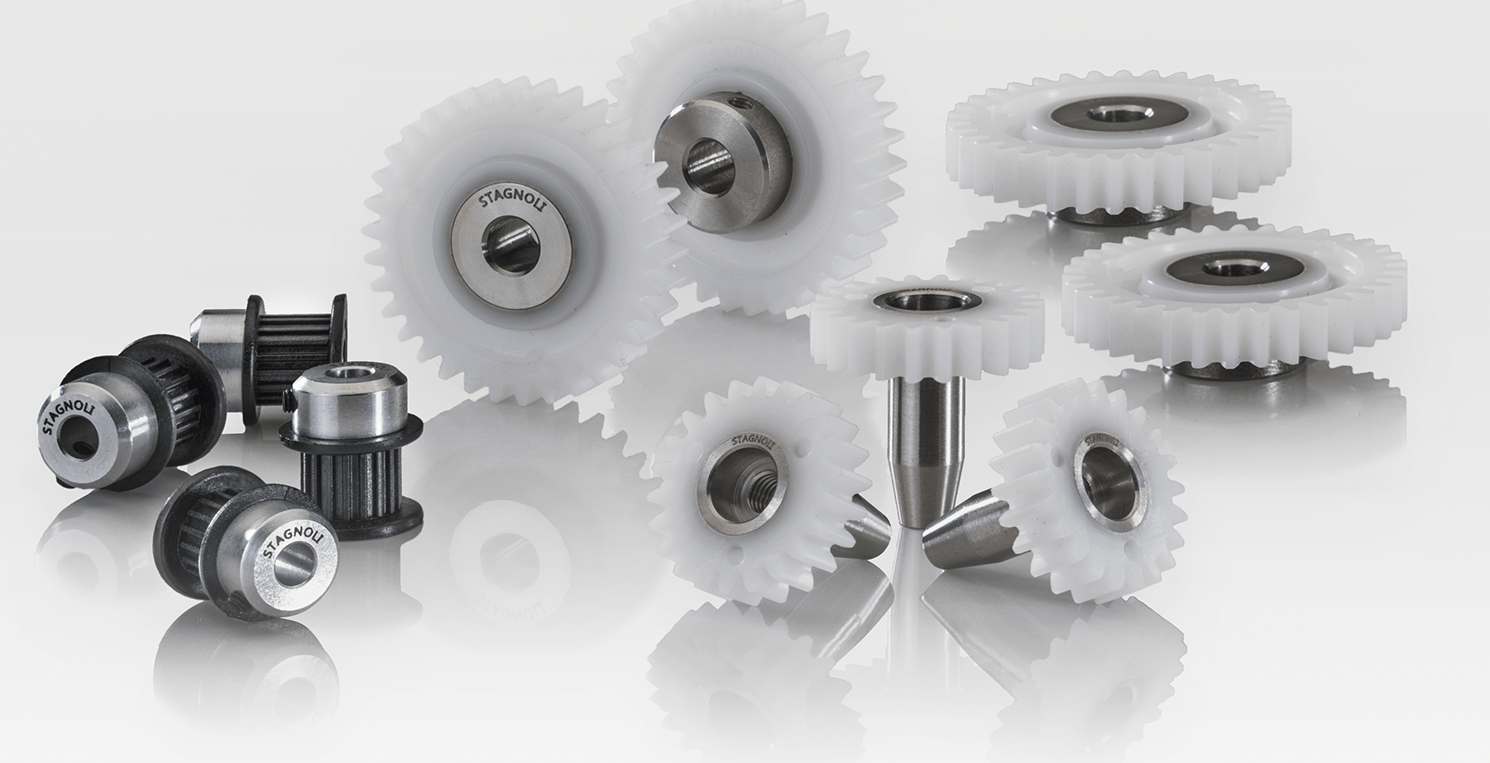
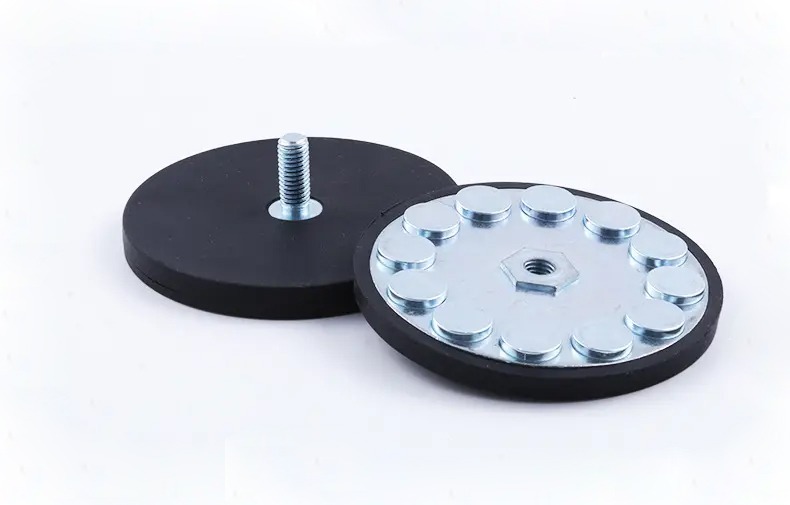
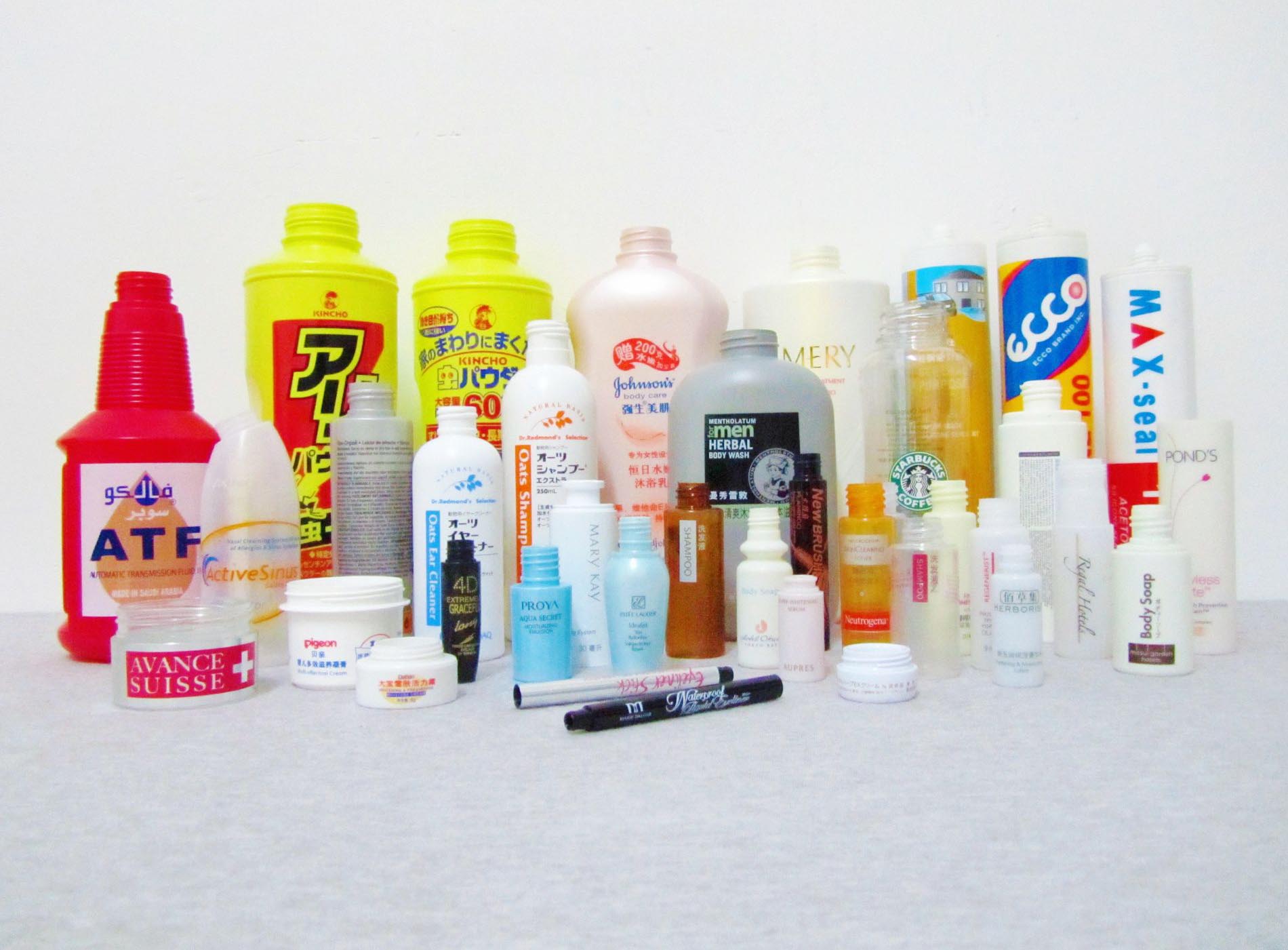
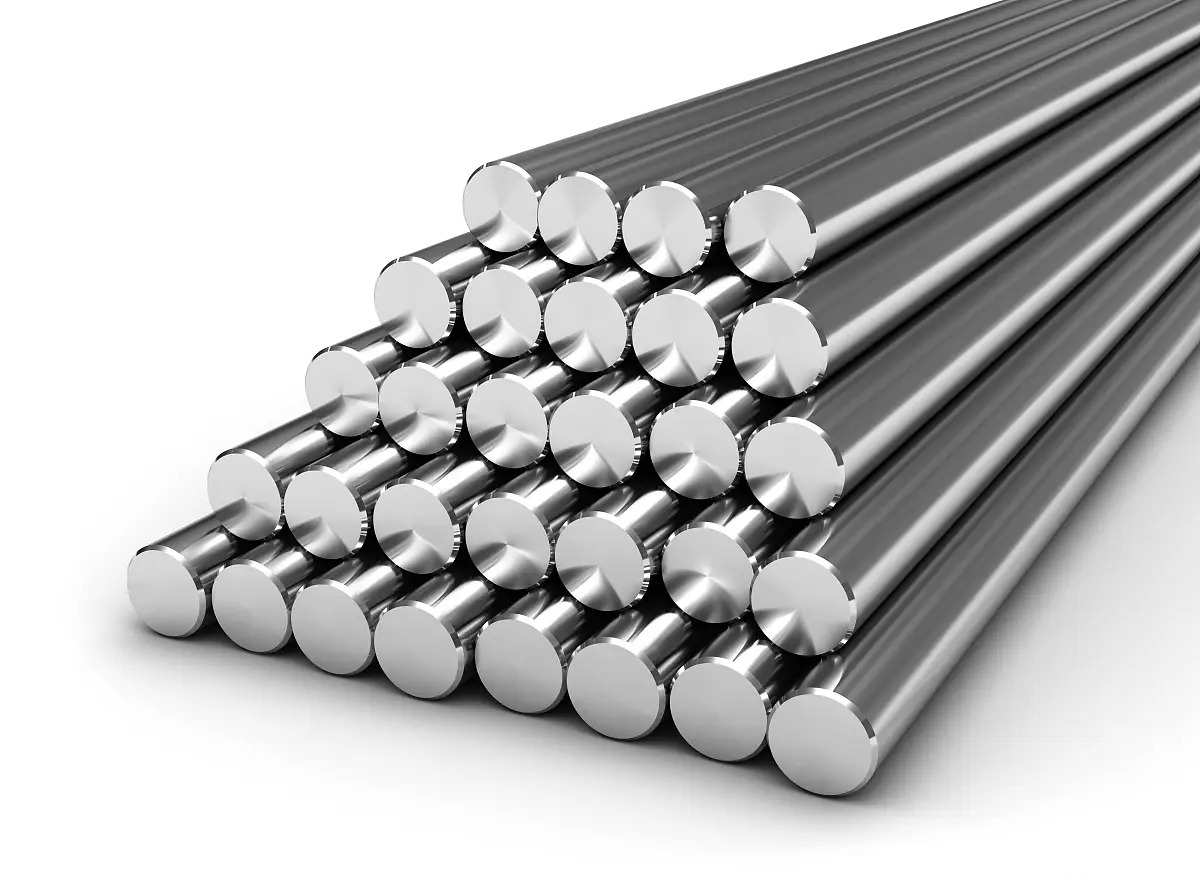
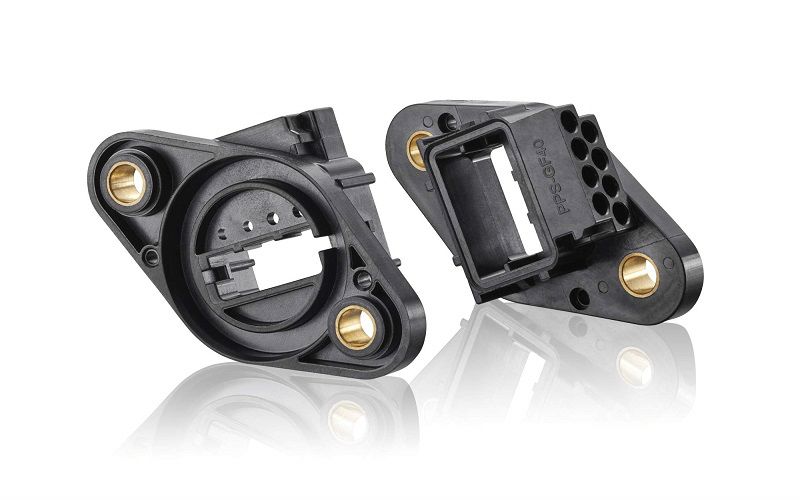
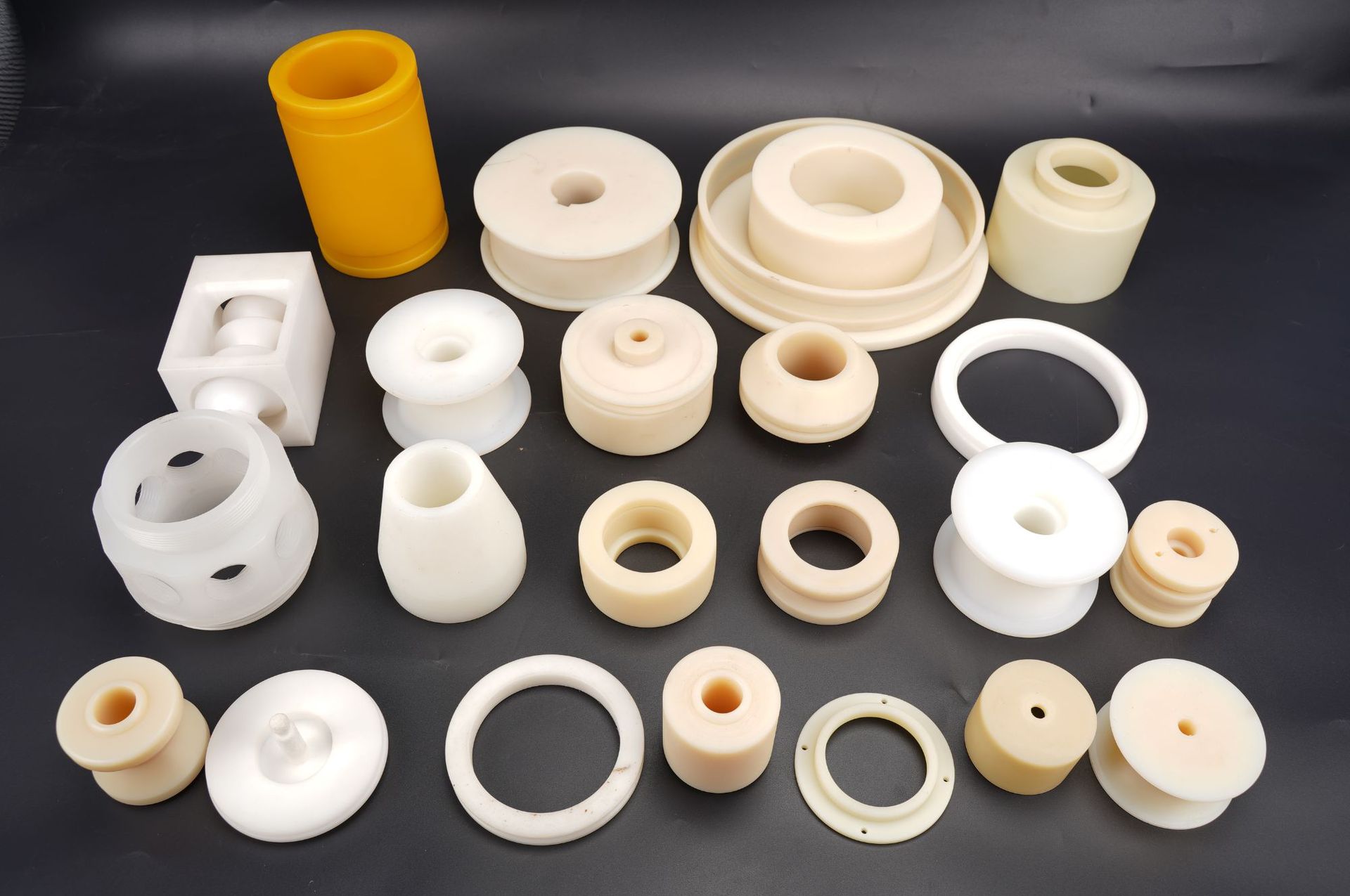
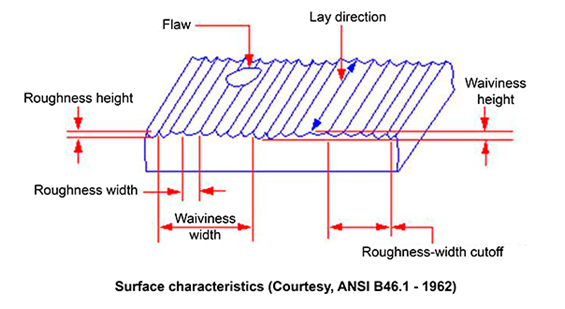
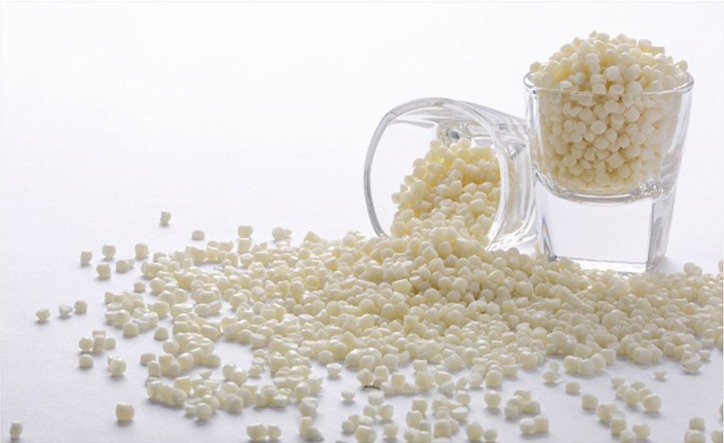
In engineering design and production, the correct selection and use of carbon steel materials can effectively improve the performance and quality of products, but also be able to reduce the production cost and improve production efficiency.
It can also reduce the production cost and improve the production efficiency. Understanding the characteristics and classification criteria of different carbon steels is essential for the rational selection of materials, optimization of product design and improvement of product quality.
This article will introduce the basic concepts of carbon steel, characteristics, welding, applications, etc. I hope that through the introduction and discussion of this article, can let you more in-depth understanding of carbon steel material knowledge, for your practical production to provide reference.
According to the chemical composition of steel can be divided into two categories of carbon steel and alloy steel.
Carbon steel is further divided into
① Low carbon steel, carbon content of less than 0.25%;
② Medium carbon steel, carbon content of 0.25%-0.6%;
③ High carbon steel, carbon content of more than 0.6%;
Steel is an alloy of iron and carbon smelted by melting. Carbon steel is used to indicate the steel with carbon as the main alloying element. Most have a carbon content of 0.2% to 2.1%. Although carbon is the main component of carbon steels, other trace elements such as tungsten, chromium, and manganese are also used to improve properties. The amount and type of alloying elements directly determine the hardness, ductility and tensile strength of the steel. Alloying elements maintain the lattice structure of steel by preventing dislocations of iron atoms. Therefore, it acts as a hardening agent in steel. The density of steel varies between 7,750 and 8,050 kg/m 3 and is also influenced by the alloying composition.
According to the quality of the product, it is divided into ordinary carbon structural steel and high-quality carbon structural steel. In carbon steels, the properties are mainly determined by the amount of carbon they contain. For this alloy, the content of other alloying elements such as chromium, manganese, cobalt and tungsten is not defined. There are four types of carbon steel. The classification is based on carbon content. Low carbon steels contain a very low percentage of carbon. There are three other types of carbon steel such as medium carbon steel, high carbon steel and ultra high carbon steel. In higher carbon steels, the carbon content varies between 0.30 and 1.70% by weight. Medium carbon steel has a carbon content of 0.30-0.59%, while high steel has a carbon content of 0.6-0.99%. Ultra-high carbon steels contain 1.0-2.0% carbon. They can be successfully heat treated.
Mild steel usually has a carbon content of 0.04% to 0.04. It is one of the largest types of carbon steel. It is also known as soft steel because of its low strength, low hardness and softness. It covers a wide variety of shapes; from flat plates to structural beams. Depending on the desired properties, other elements can be added or enhanced. For example: drawing quality (dq) – carbon level is kept low and aluminum is added, for structural steels, carbon level is higher and manganese content is increased. Mild steel is a type of carbon steel that contains very small amounts of carbon. It is about 0.16-0.29% by weight. This type of steel is very cheap and most commonly used. It is ductile and malleable but has low tensile strength. Mild carbon cannot be hardened by heat treatment.
The annealed organization of mild steel is ferrite and a small amount of pearlite, which has low strength and hardness and good plasticity and toughness. Therefore, its cold forming good can be used to crimp, bending, stamping and other methods of cold forming. This steel has good weldability. Very low carbon content of low carbon steel hardness is very low, cutting and machining is not good, quenching treatment can improve its cutting and machining. Mild steel is generally rolled into angles, channels, I-beams, tubes, strips, plates, used to make a variety of building components, containers, boxes, furnaces and farm equipment. High-quality mild steel rolled into thin plates, the production of automobile cabs, generator covers and other deep-drawn products; also rolled into bars, for the production of mechanical parts with low strength requirements. Mild steel is generally not heat-treated before use, carbon content of 0.15% or more by carburizing or cyanide treatment, for the requirements of the surface layer of high degree of good wear resistance of shafts, bushings, sprockets and other parts. Low carbon steel due to low strength, the use of limited. Appropriate increase in the manganese content of carbon steel, and add trace vanadium, titanium, niobium and other alloying elements, can greatly improve the strength of steel. If you reduce the carbon content of steel and add a small amount of aluminum, boron and carbide-forming elements, you can get ultra-low carbon bainite group enough to its high strength, and maintain good plasticity and toughness.
Low carbon steel has a greater tendency to aging, both quenching aging tendency, and deformation aging tendency. When the steel from the high temperature faster cooling, ferrite carbon, nitrogen in the oversaturated state, it can also be slowly formed at room temperature iron carbon and nitrogen, and thus the strength and hardness of the steel to improve the plasticity and toughness is reduced, this phenomenon is known as quenching aging. Mild steel even without quenching and air cooling will produce aging. Low-carbon steel by deformation produces a large number of dislocations, ferrite carbon, nitrogen atoms and dislocations in the elastic interaction, carbon, nitrogen atoms gathered around the dislocation line. This carbon, nitrogen atoms and dislocation line of the combination of the body is called the age of Kirchner’s air group (Kirchner’s ear air group). It will make the steel strength and hardness and plasticity and toughness decrease, this phenomenon is called deformation aging. Deformation aging than quenching aging on the plasticity and toughness of mild steel has more harmful, in the tensile curve of mild steel has a clear upper and lower two yield points. Since the upper yield point appears until the end of the yield extension, in the specimen surface appears due to uneven deformation and the formation of the surface wrinkles band, known as Lüders band. Many stampings are often scrapped as a result. There are two methods for its prevention. The other is to add aluminum or titanium to the steel, so that it and nitrogen to form a stable compound, to prevent the formation of Kirchhoff’s gas group caused by deformation aging.
Mild steel is generally rolled into angles, channels, I-beams, steel tubes, steel strips or plates, used to make a variety of building components, containers, boxes, furnaces and farm equipment. High-quality mild steel rolled into thin plates, the production of automobile cabs, hoods and other deep-drawn products; also rolled into rods, for the production of mechanical parts with low strength requirements.
Mild steel is a ductile material. Its stress-strain curve in tension is mainly divided into four stages: elastic stage, yielding stage, strengthening stage, local deformation stage, in the local deformation stage there are obvious yielding and necking phenomenon. At the beginning of the elastic stage, fully comply with the Hooke’s law along the straight line, the proportion of the limit after the deformation accelerated, but there is no obvious yielding stage.
Medium carbon steel is carbon steel with 0.25% to 0.60% carbon. There are a variety of products such as sedentary steel, semi-sedentary steel, boiling steel and so on. In addition to carbon can also contain a small amount of manganese (0.70% ~ 1.20%). Usually, the manganese content of medium carbon steel ranges from 0.060% to 1.65%. This product is stronger than mild steel and is more difficult to form, weld, and cut. Medium carbon steels are often hardened and tempered using heat treatment.
Medium-carbon steels have good hot-working and cutting properties and poor welding properties. Strength and hardness are higher than mild steel, while plasticity and toughness are lower than mild steel. Can not be heat-treated, direct use of cold-rolled material, cold-drawn material, can also be used after heat treatment. Quenched and tempered medium carbon steel has good overall mechanical properties. Can achieve the highest hardness of about HRC55 (HB538), σb for 600 ~ 1100MPa. so in the medium strength level of various uses, medium carbon steel has been the most widely used, in addition to as a building material, but also a large number of used in the manufacture of a variety of mechanical parts. Medium carbon steel belongs to the sub-eutectic steel, its annealed organization for pearlite and ferrite. With the increase of carbon content in the steel, the number of pearlite in the organization increases, while the number of ferrite decreases. Carbon content greater than 0.40% of the steel quenching organization for martensite; carbon content greater than 0.40%, in addition to martensite there is a small amount of residual austenite, residual austenite with the increase in carbon content of steel and increase.
Medium carbon steel carbon content than low carbon steel, high strength, poor weldability. Commonly used 35 #, 45 #, 55 # steel. The main characteristics of medium carbon steel electrode arc welding and its casting welding repair are as follows:
(1) the heat affected zone is prone to produce hardened organization. The higher the carbon content, the greater the plate thickness, the greater this tendency. If the welding material and process specifications are not properly selected, it is easy to produce cold cracks.
(2) Due to the higher carbon content of the base metal, the carbon content of the weld is also higher, which is prone to hot cracking.
(3) Due to the increase of carbon content, so the sensitivity to porosity increases. Therefore, the requirements for deoxidizing the welding material, degreasing and descaling the base metal, and drying the welding material are more stringent.
The final heat treatment of medium-carbon steel has tempering, low-temperature tempering after quenching, low-temperature tempering after high-frequency quenching, isothermal quenching and medium-temperature tempering after quenching.
(1) Tempering. The organization is tempered sohnite. This organization has good comprehensive mechanical properties, high strength, good plasticity and toughness. Compared with alloy steel, carbon steel hardenability is poor, so only suitable for cross-section size is not large medium carbon steel parts for tempering.
(2) low temperature tempering after quenching. Organization for tempered martensite, this organization has high strength and appropriate plasticity and toughness.
(3) High-frequency quenching and low-temperature tempering. High-frequency quenching is generally tempered or normalized before quenching. So after high-frequency quenching and tempering, the heart of the part has high strength, good plasticity and toughness, while its surface layer has high hardness and good wear resistance. In addition, high-frequency quenched parts surface layer produces compressive stress, its fatigue limit is high, long service life.
(4) Isothermal quenching. The organization is bainite, this organization has high strength and good plasticity and toughness.
(5) Medium temperature tempering after quenching. The organization is tempered austenite.
High-strength medium-carbon tempered steel, with a certain degree of plasticity, toughness and strength, good cutting, tempering treatment has a very good comprehensive mechanical properties, hardenability is poor, easy to produce cracks, welding performance is not high, the need to weld before a very good preheating, post-weld heat treatment.
Medium carbon steel is mainly used in the manufacture of higher strength moving parts, such as air compressors, pumps, pistons, steam turbine impellers, heavy machinery, shafts, worms, gears, etc., the surface of the wear-resistant parts, crankshafts, machine tool spindles, rollers, clamping tools and so on.
High-carbon steels, also known as tool steels, usually have a carbon content of 0.61% to 1.70% and can be hardened and tempered. High carbon steel is difficult to cut, bend and weld. Once heat-treated, it becomes extremely hard and brittle.
After appropriate heat treatment or cold-drawing hardening, high carbon steel has high strength and hardness, high elastic and fatigue limits, moderate cutting performance, but poor welding performance and cold plastic deformation ability. Due to the high carbon content, water quenching is prone to cracking, so more double liquid quenching, small cross-section parts more oil quenching. This type of steel is generally used after quenching by medium temperature tempering or normalizing or in the surface quenching condition. Mainly used in the manufacture of springs and wear parts, can also be used for injection molds, die casting molds, stamping dies. Carbon tool steel is basically do not add alloying elements of high-carbon steel, but also tool steel in the lower cost, good hot and cold machinability, the use of a wider range of steel. High carbon steel density 7.81g/cm³. It can be used in the production of fishing gear.
High-carbon steel hardness, strength depends mainly on the amount of carbon solidly dissolved in steel, and with the increase in the amount of solidly dissolved carbon and improve. Solid dissolved carbon more than 0.6%, the hardness after quenching no longer increases, just the number of excess carbides increased, the steel wear resistance increased slightly, while the plasticity, toughness and elasticity has been reduced. For this reason, often according to the conditions of use and the strength of steel, toughness matching to choose a different steel number. For example, the manufacture of the spring or spring-type parts of the force is not large, you can choose a lower amount of carbon 65 steel. General high-carbon steel available in electric furnaces, flat furnaces, oxygen converter production. Requirements for higher quality or special quality can be used in electric furnace smelting and vacuum self-consumption or electroslag remelting. Smelting, strict control of the chemical composition, especially sulfur and phosphorus content. In order to reduce segregation and improve isotropic properties, the ingot can be high temperature diffusion annealing (especially important for tool steel). Hot processing, over eutectic steel stop forging (rolling) temperature requirements are low (about 800 ℃), forging and rolling into material should be avoided after the precipitation of coarse mesh carbides, in 700 ℃ should pay attention to the slow cooling, in order to prevent cracking caused by thermal stress. Heat treatment or hot working process to prevent surface decarburization (especially important for spring steel). Hot working should have enough compression ratio to ensure the quality and use of steel performance.
Heat-treated high carbon steel is very hard and has good wear resistance, so it is commonly used in the manufacture of high-quality CNC machining equipment cutting tools, such as cutting tools, saw blades and drills, reamers, machine parts, after the electroslag remelting of high carbon steel is commonly used in injection molds, die casting molds, as well as stamping molds.
Because high carbon steel can withstand high levels of stress and pressure without deformation or fracture, it is an ideal material for many heavy equipment. Its durability and toughness also make it a common choice for construction and engineering projects that require a reliable and long-lasting material.
Ultra-high carbon steel is an iron-based alloy material with a carbon content of 1.0-2.1%. The earliest industrial example of ultra-high carbon copper was Damascus. Its carbon content is 1.5%. In the mid-1970s, Stanford University in the United States first carried out research on the superplasticity of ultra-high carbon steel, and then the U.S. National Laboratory also carried out research on ultra-high carbon steel . And obtained a series of patents. In addition. China has also carried out research in ultra-high carbon steel. The use of appropriate preparation process to obtain ultra-fine grain ultra-high carbon steel without reticulated carbide. Not only in the middle and high temperatures with high deformation rate of superplastic properties. And at room temperature has good comprehensive mechanical properties. Ultra-fine crystal ultra-high carbon steel is not only expected to replace part of the high carbon steel production molds, steel wires, structural components, thereby significantly improving its service life, and the use of which, high temperature under the good solid state connection characteristics, but also with their own or other metal-based materials connected to the preparation of a new type of high-performance laminated composite materials. It is a new class of materials with great prospects for industrial application.
Low carbon steel (mild steel) for the carbon content of less than 0.25% of carbon steel, because of its low strength, low hardness and soft, so also known as soft steel. It includes most of the ordinary carbon structural steel and a portion of high-quality carbon structural steel, most of which are not heat-treated with dry engineering structural parts, some of which are used for the requirements of wear-resistant mechanical parts by carbon and other heat treatment are mild steel.
Medium carbon steel hot working and cutting performance is only good, poor welding performance. Strength, hardness is higher than mild steel, while plasticity and toughness is lower than mild steel. Can not be heat-treated, direct use of cold-rolled material, cold-drawn material, can also be used after heat treatment. Quenched and tempered medium carbon steel has good overall mechanical properties. Can achieve the highest hardness of about HRC55 (HB538), ob for 600 ~ 1100MPa. so in the medium strength level of the various uses, medium carbon steel has been the most widely used, in addition to as a building material, but also a large number of used in the manufacture of a variety of mechanical parts.
High carbon steel (High Carbon Stee) often called tool steel, carbon content from 0.60% to 1.70%, can be quenched and tempered, Minamata welding performance is not good. Common hammers, clubs, etc. by the carbon content of 0.75% of the steel manufacturing; cutting tools such as drills, taps, reamers, etc. by the carbon content of 0.90% to 1.00% of the steel manufacturing.
low carbon steel is more amenable to welding due to its lower carbon content, which results in better ductility and reduced risk of hardening and cracking. High carbon steel, on the other hand, presents greater challenges in welding due to its high carbon content, which leads to increased hardness, brittleness, and susceptibility to cracking. Special precautions and welding techniques are necessary to achieve satisfactory welds in high carbon steel
Low carbon steel, with a carbon content of less than 0.25%, is also known as mild steel. It is characterized by its low strength, low hardness, and ductility. This steel is widely used in engineering structures and mechanical parts that require good toughness and ductility. The welding performance of low carbon steel is generally good due to its low carbon content, which reduces the risk of hardening and淬火 during welding. The low carbon content also results in minimal risk of cold cracking, making it suitable for various welding processes without the need for special procedures. The welds made on low carbon steel typically have good impact toughness and ductility, and post-weld heat treatment is usually not required.
In contrast, high carbon steel, with a carbon content ranging from 0.60% to 1.70%, is often referred to as tool steel. It is known for its high hardness and wear resistance but has poor weldability due to its high carbon content. The high carbon content leads to a greater tendency for quenching and the formation of hard and brittle martensitic structures in the heat-affected zone (HAZ), which significantly reduces the ductility and toughness of the weld. This makes high carbon steel more susceptible to cold cracking and other welding defects. Special welding techniques and materials are required to ensure the performance of the welds in high carbon steel. Preheating and the use of low hydrogen electrodes are often necessary to minimize the risk of cold cracking in the HAZ. Additionally, the selection of welding consumables is critical; low hydrogen type electrodes with good sulfur removal capabilities and low diffusible hydrogen content are preferred.
High carbon steel has a greater tendency to develop hot cracks compared to medium carbon steel during welding. This is due to its high carbon content, which makes it more susceptible to rapid hardening and cracking under welding heat.
High carbon steel is more sensitive to quenching, which means it is prone to forming martensite, a hard and brittle microstructure, in the heat-affected zone (HAZ) during welding. If improper welding procedures are used, cold cracks may develop in the HAZ.
Due to the high welding temperatures, the grain size in high carbon steel grows rapidly, and carbonides tend to accumulate and grow at grain boundaries. This leads to embrittlement of the weld and a reduction in the strength of the welded joint.
High carbon steel has poorer thermal conductivity compared to low carbon steel. This results in rapid cooling of the weld pool, which can induce high internal stresses in the weld and increase the likelihood of crack formation.
Due to its poor weldability, special welding processes and precautions are required to ensure the performance of the welded joint in high carbon steel. These may include preheating, using low hydrogen electrodes, and post-weld heat treatment to relieve stresses and prevent cracking.
The choice of welding materials for high carbon steel depends on factors such as the carbon content of the steel, the design of the workpiece, and the operating conditions. Low hydrogen electrodes with good desulfurization ability and low hydrogen content in the deposited metal are commonly used. If the strength of the weld metal is required to match the base metal, electrodes of corresponding grade should be selected.
To limit the carbon content in the weld metal and reduce the fusion ratio, U-shaped or V-shaped grooves are typically used for welding high carbon steel. The grooves and the surrounding areas should be cleaned of oil, rust, and other contaminants before welding.
Preheating the workpiece before welding and controlling the inter-pass temperature are crucial steps in welding high carbon steel to reduce the hardness and brittleness of the HAZ and to facilitate hydrogen diffusion from the weld.
Stress relief annealing at a temperature of around 650°C is often performed after welding to relieve internal stresses and further prevent cracking.
High carbon steel refers to steel with higher carbon content, usually between 0.6-1.7% carbon content. And low carbon steel, as the name suggests, refers to the lower carbon content of steel, its carbon content is generally between 0.2-0.4%. This difference in carbon content leads to the two in the physical properties and the use of the obvious difference.
Due to the different carbon content, high carbon steel and low carbon steel in the mechanical properties show greater differences. High-carbon steel has higher strength and hardness due to its higher carbon content, but lower plasticity and greater brittleness. Low carbon steel shows good plasticity and toughness, but also relatively high strength, has excellent welding properties.
High carbon steel because of its high hardness, usually need to be quenched and tempered to achieve the desired mechanical properties. It is mainly used in the manufacture of wear-resistant requirements of high, withstand large loads of parts. Mild steel, on the other hand, is more commonly used to make structural parts and products with high strength requirements, such as bridges, construction and automotive parts. Mild steel is also widely used in the production of welded structural parts due to its good welding properties.
The manufacturing process of mild steel is relatively complex, requiring specific heat treatment and processing equipment, and is relatively costly. Mild steel, on the other hand, is relatively more economical in terms of manufacturing process and cost, and is therefore used as a more economical choice in many applications.
Mild steel and high carbon steel in the chemical properties and mechanical properties have obvious differences. Mild steel has a high degree of plasticity and malleability, and is easy to mold. High carbon steel, on the other hand, is stronger and harder, but less ductile. High carbon steel is more suitable for the production of some of the higher strength requirements, hardness requirements of the parts or products.
Mild steel is widely used in construction, machinery, automobile, building and other fields, used to make parts, components and structural components, such as bolts, nuts, steel plates, tubes and so on. Because mild steel is easy to process, low cost, so the use of a wider range. While high carbon steel is mainly used in the production of scissors, knives, springs and other products that require high strength and cutting ability.
Low carbon steel is easier to heat treatment, can control the cooling rate and temperature to change its mechanical properties. At the same time, the lower carbon content of mild steel makes it less prone to carbide precipitation during welding, thus reducing the possibility of brittle welds. However, high carbon steel due to the higher carbon content, easy to cold crack and hot crack phenomenon in the welding process, requiring more delicate welding process.
Mild steel has a low carbon content, which makes it more resistant to corrosion. Low carbon steel is usually plated with a layer of corrosion inhibitor or galvanized on the surface to improve its corrosion resistance. While high-carbon steel due to the high carbon content, in the external environment is prone to corrosion, the need for surface treatment or the use of stainless steel and other corrosion-resistant processes.
Low carbon steel production and processing of low energy consumption, less impact on the environment. Because of the low carbon content of mild steel, and elemental carbon is the main component of carbon dioxide, the production and use of mild steel reduces the contribution to carbon dioxide emissions. In contrast, the production and use of high-carbon steels may generate more greenhouse gas emissions and place greater pressure on the environment.
Attractive Plastics is China one-stop custom plastic injection molding manufacturer, China quality injection molded manufacturer. We’re good at injection molded magnets, overmolding magnets, plastic integrated magnets, plastic encapsulation magnets, silicone rubber integrated magnets, metal insert molding, we have more than 20 years experience in plastic injection molding field.
At Attractive Plastics, we’re committed to transforming your concepts into reality. With our cutting-edge technology and unwavering dedication to innovation, we specialize in guiding your products from the prototype stage to full-scale production. Let us be your partner in bringing your ideas to life. Reach out to us today to explore the possibilities of custom injection molding. Contact us now.
To summarize, the main differences between high-carbon and low-carbon steels are in their carbon content, mechanical properties, heat treatment and use, as well as process costs and economic benefits. In practical application, it is necessary to choose the appropriate type of steel according to the specific requirements and conditions of use.