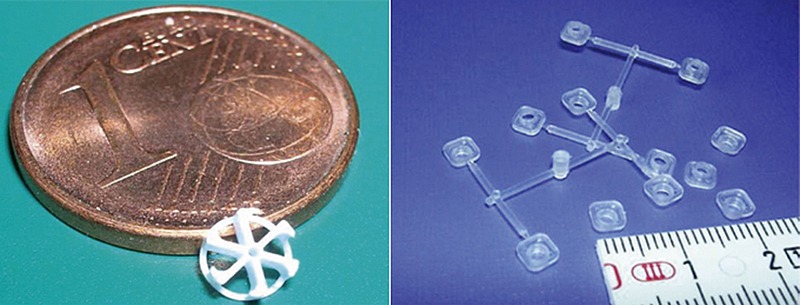
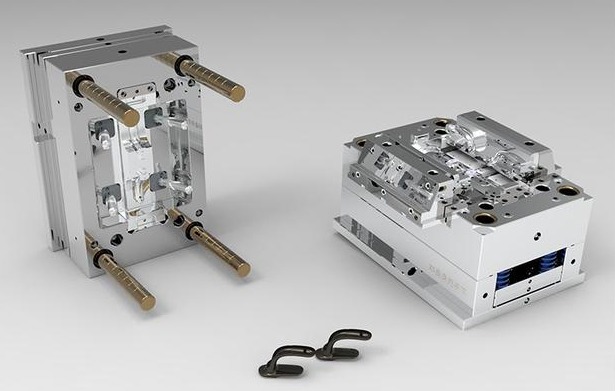
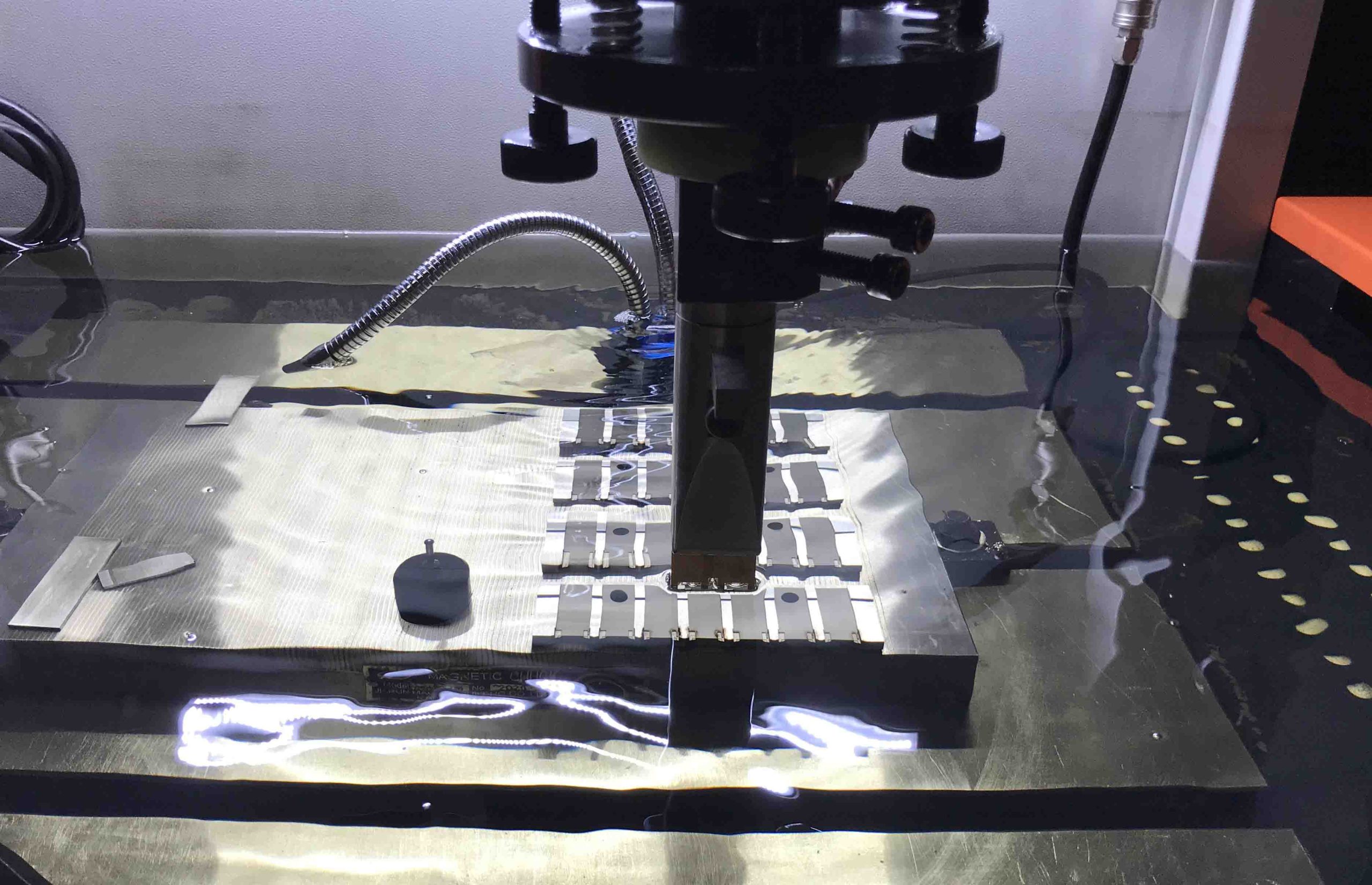
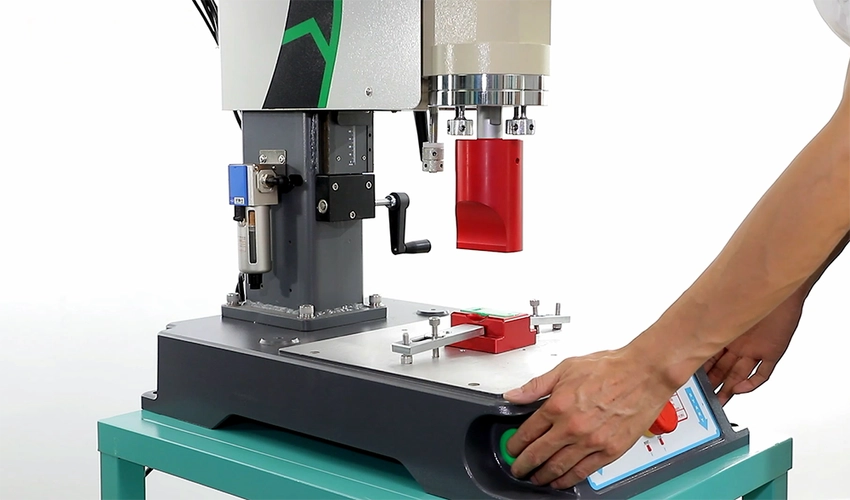
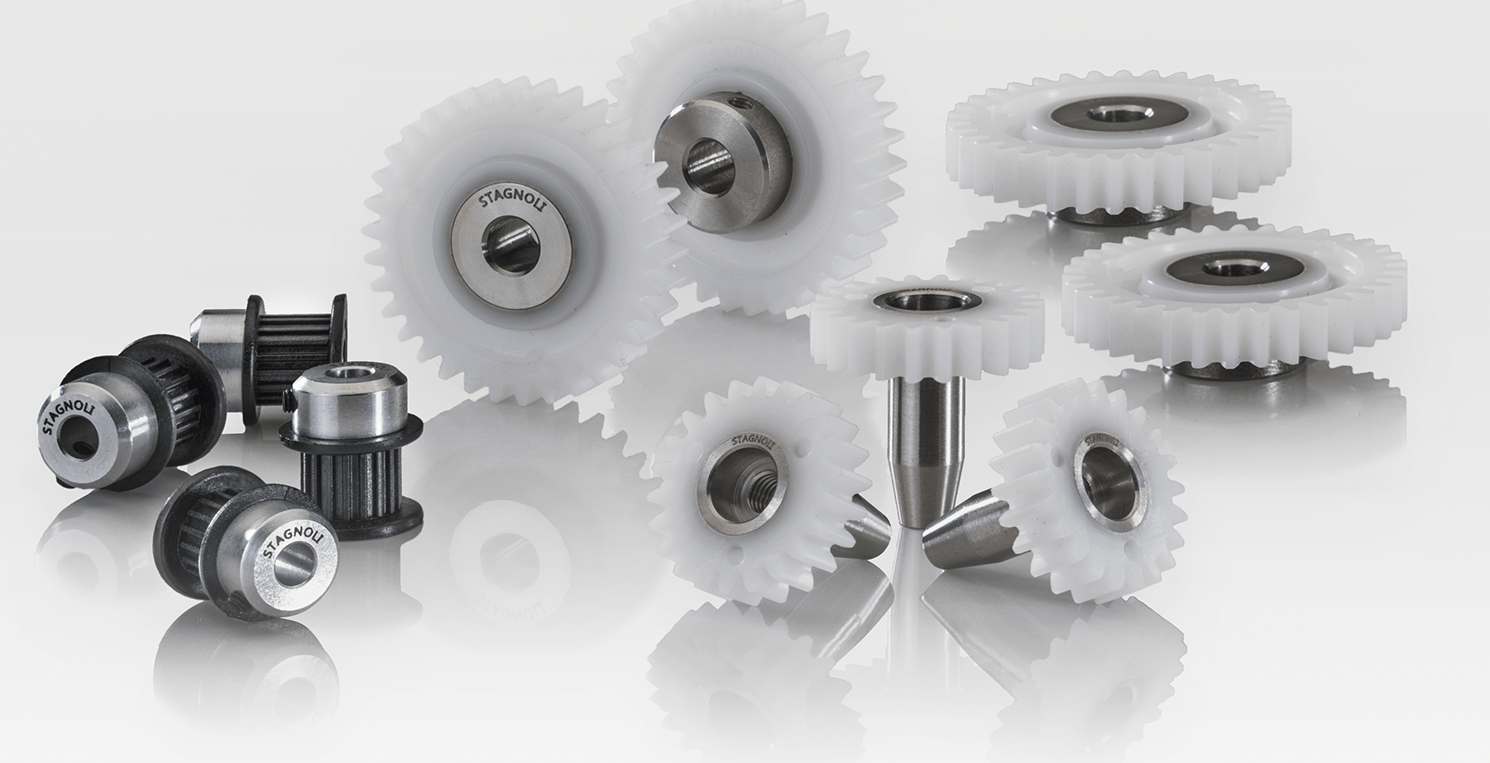
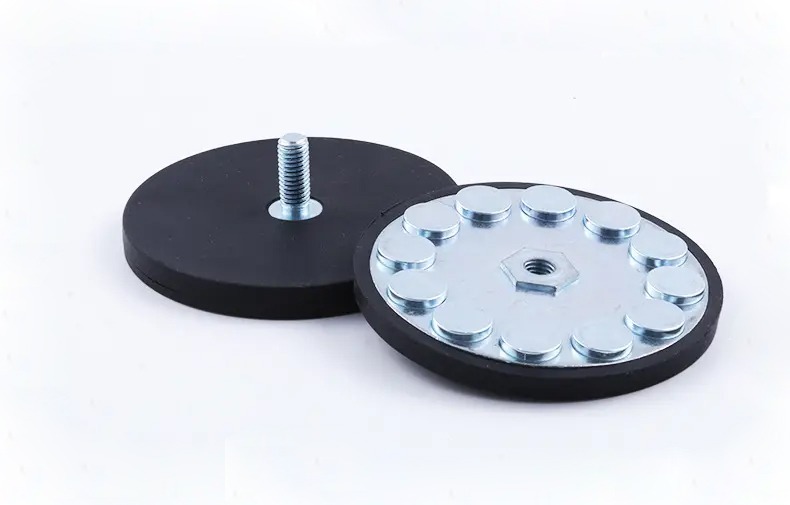
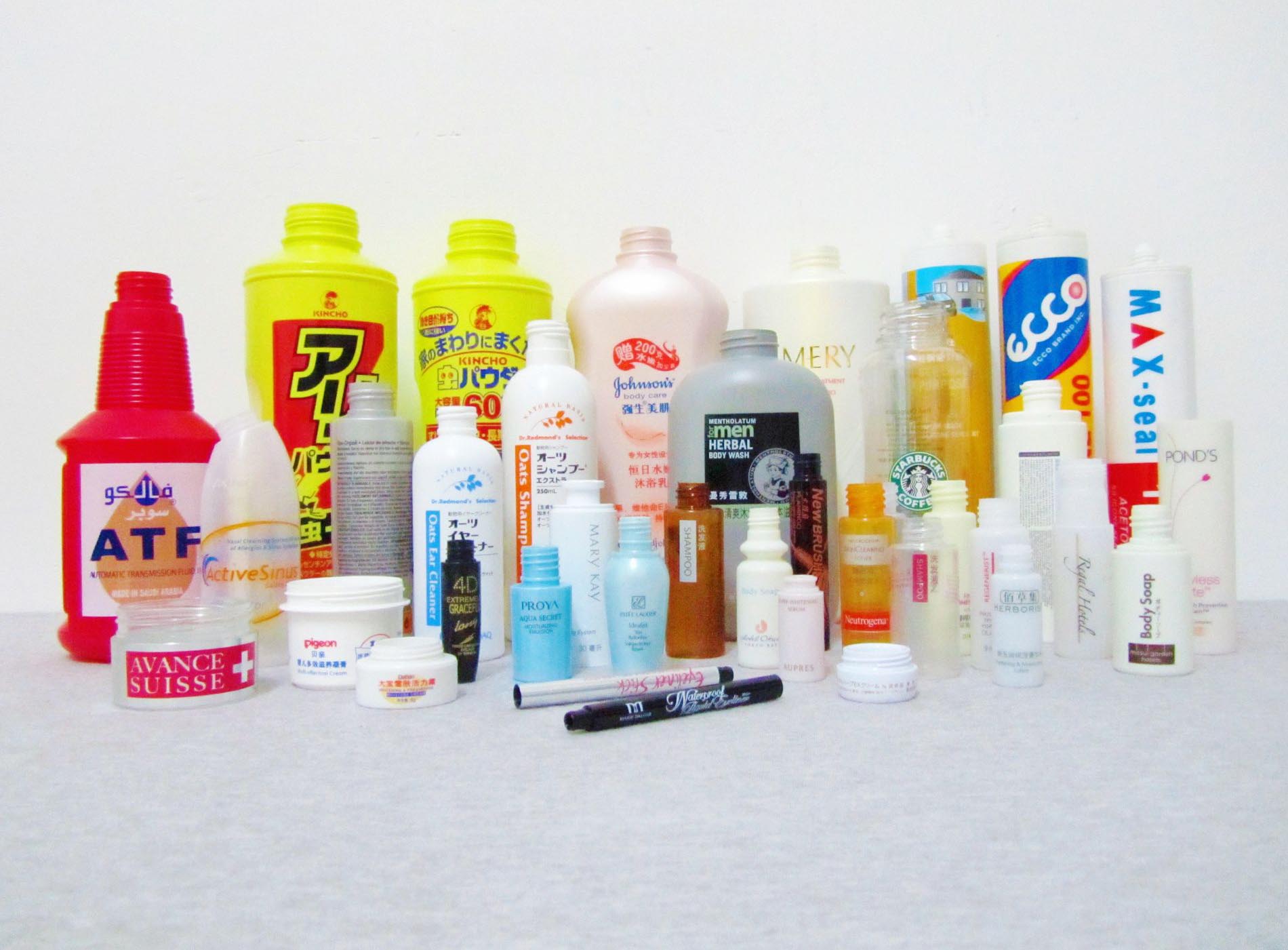
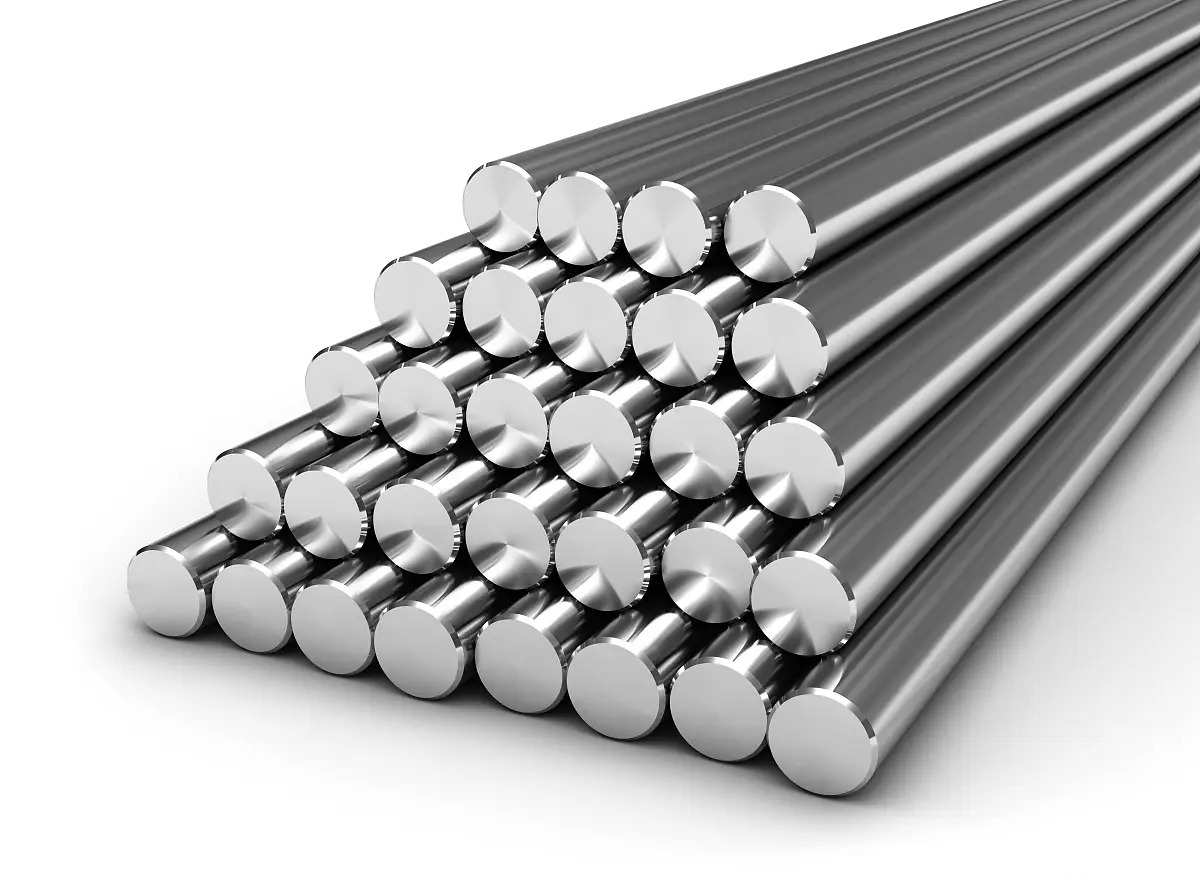
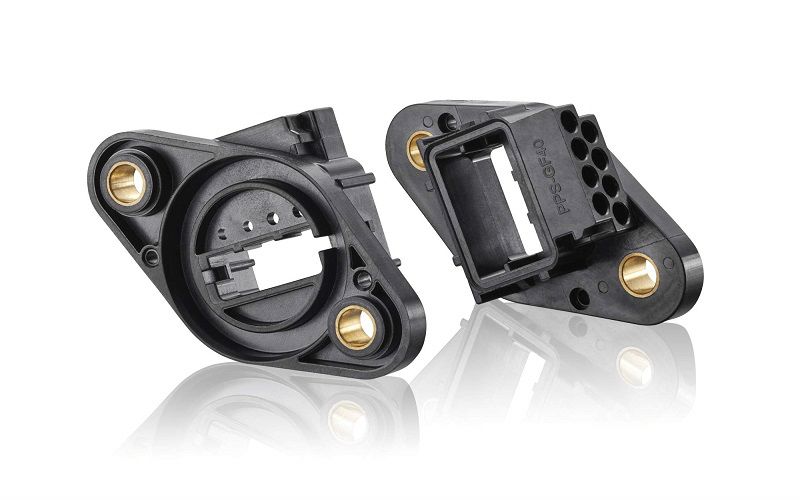
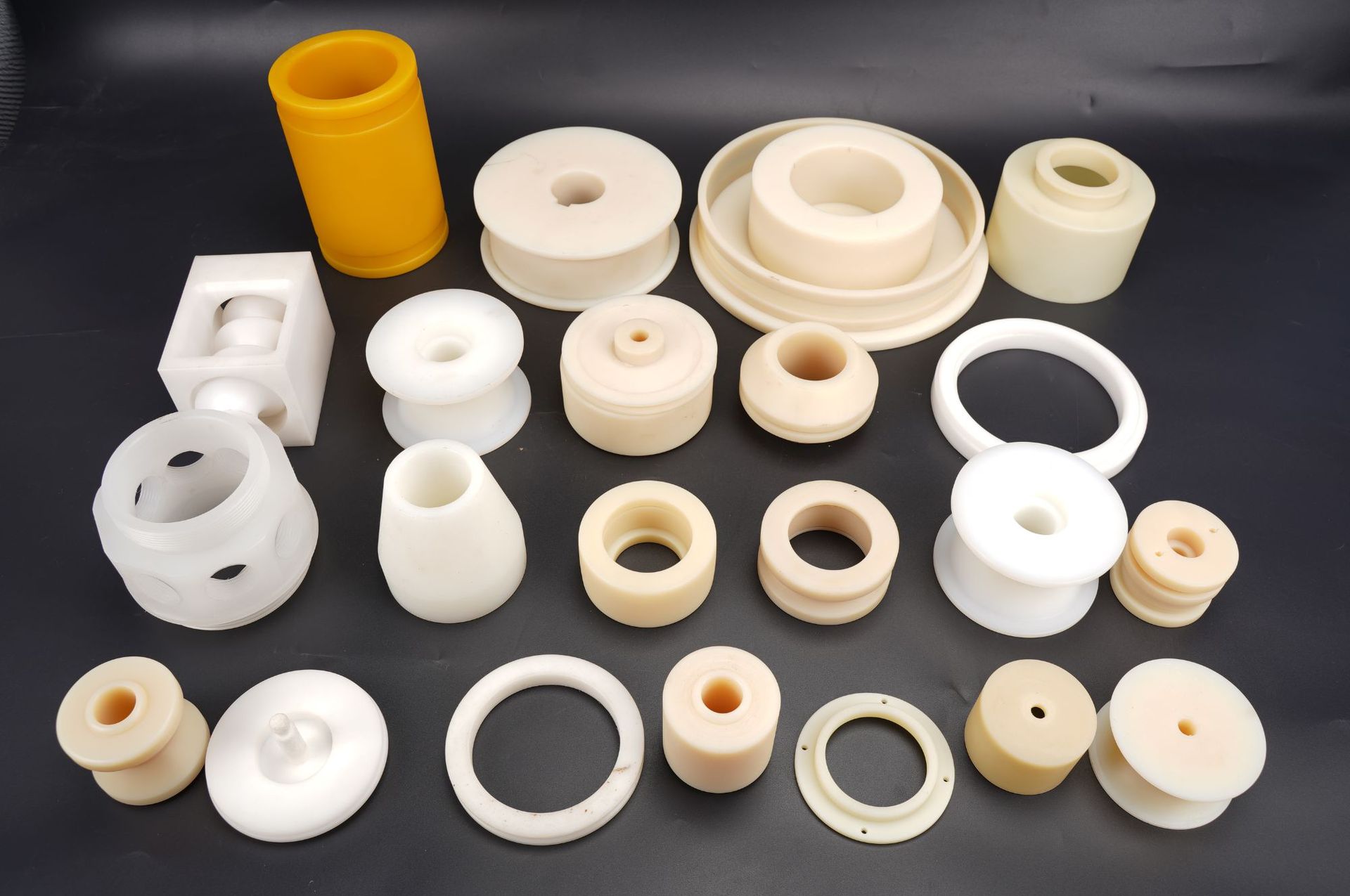
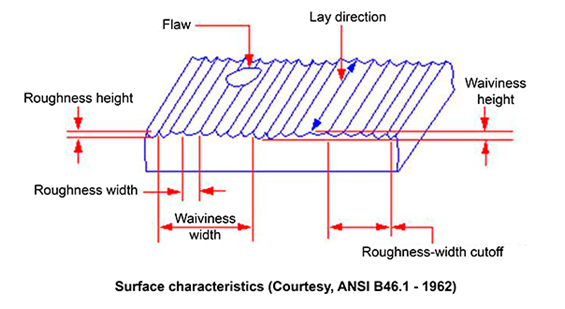
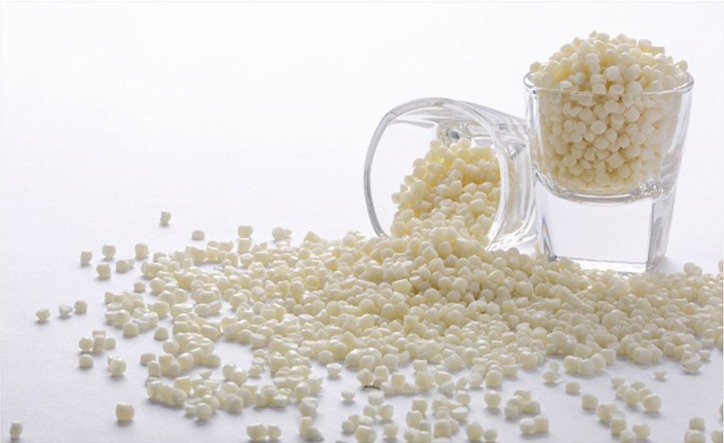
For many molded parts that require assembly, ultrasonic welding is a better connection method compared to adhesives. It is clean, low-cost, has high bonding strength, good stability while avoiding additional components. Ultrasonic welding technology has become an important processing method for many industries thanks to its unique advantages.
This article will take an in-depth discuss the concepts, principles, advantages, design considerations and applications of ultrasonic welding to help better understand this unique technology.
Welding of thermoplastic plastics using ultrasonic technology, as one of the plastic welding techniques, is still in its initial development stage. The theoretical knowledge of ultrasonics can be traced back to 1880 when Curie studied the relationship between materials and electrical and mechanical vibrations. The importance of piezoelectric effect was not fully realized until the late 20th century with the use of submarine echo ranging technology.
During World War II, echo ranging technology was applied and improved, giving birth to sonar technology. In 1945, the use of ultrasound for defect detection in objects entered the application stage. The technology was also used for ultrasonic cleaning and degreasing.
The plastics commonly used in our daily life mainly include thermoplastics, thermosets and elastomers. In 1960, welding of engineering plastics using ultrasonics was practically implemented, and high-energy ultrasound was introduced. Plastic ultrasonic welding was achieved in 1963.
In 1965, Robert Soloff and Seymour Linsley were granted a patent for the ultrasonic method for welding rigid thermoplastic parts. This was the first application of ultrasonic welding technology in the plastics industry. Ultimately, ultrasonic welding started to be widely used in the plastics sector in 1972.
Ultrasonic welding is a process that uses high-frequency vibrations to achieve welding by friction melting the material molecules in contact surfaces.
Ultrasonic welding is commonly used for welding plastics, rubber, metals and other materials. It can achieve precision welding, high-speed welding and automated welding. It has advantages such as fast welding speed, high welding quality, beautiful seam and no need to add welding wire or rods. It is widely used in automotive, electronics, medical, packaging and other fields.
The principle of ultrasonic welding is mainly based on the propagation and conversion of high-frequency vibrating waves. In short, it works by using an ultrasonic generator to convert electrical energy into high-frequency mechanical vibrations, and then transmitting the vibrational energy to the materials to be welded through a welding head, causing friction heat between the material molecules and thus melting the materials to form a welded joint.
The working process is to transform the current 50/60 Hz electric frequency into a high electric energy of 15 KHz to 40 KHz through a piezoelectric device. Then the electric energy is supplied to the converter. The converter converts the electric energy into mechanical vibrational energy for ultrasound. Subsequently, the mechanical motion is transmitted to the welding head through an amplitude conversion rod assembly that can change the amplitude. The welding head transmits the received vibrational energy to the surfaces of the objects to be welded, and forms a molten bond between the molecular layers of the two objects through pressure and friction
First, the ultrasonic generator converts the 50/60 Hertz electric current into high-frequency electric energy, such as 15, 20, 30 or 40 KHz. This conversion process endows the electric energy with the high-frequency characteristics needed for ultrasonic welding.
Next, the converted high-frequency electric energy is further converted into mechanical vibrations of the same frequency by the transducer. The transducer plays a critical role in this process, as it can efficiently convert electric energy into mechanical energy.
Then, these mechanical vibrations are transmitted to the welding head through an amplitude conversion rod assembly that can change the amplitude. After the welding head receives the vibrational energy, it directly transmits it to the joining area of the workpieces to be welded.
At the joining area, due to the friction between the welding head and workpieces under high-frequency vibrations of tens of thousands of times per second, a large amount of heat is generated. When the heat accumulates to a certain degree, the component area of the workpieces to be welded will be melted. Due to the poor heat conductivity of plastics, the heat can’t be dissipated in time, so the contact surface is rapidly melted.
Finally, a certain pressure is applied in the molten area to fuse the two components together in the molten state. When the ultrasonic effect stops, pressure is maintained for a period of time to solidify and shape the molten area, forming a solid molecular chain and achieving the welding purpose.
An ultrasonic welder is a device that utilizes ultrasound for welding, commonly used for connecting plastics, metals and composite materials.
An ultrasonic welding machine mainly consists of the following parts:
An ultrasonic welding machine has various functions, not only can it complete plastic welding, embedding, operations, but also be used for metal welding and riveting, etc. Different welding heads can be replaced to meet different welding requirements.
The price of ultrasonic welding machines varies depending on factors such as brand, model, functions and market. In general, the price of ultrasonic welding machines ranges from $1000 to $10,000 USD. If equipped with automated devices, the price may exceed tens of thousands of USD.
Common ultrasonic welding frequencies are 15 kHz, 20 kHz, 30 kHz, 35 kHz and 40 kHz. Lower frequencies (such as 15 kHz, 20 kHz) are suitable for thicker materials and larger welding areas as they can provide larger vibration amplitudes and higher energy transfer. Higher frequencies (such as 30 kHz to 40 kHz) are suitable for thinner materials and finer welds as they can produce smaller vibration amplitudes and higher vibration frequencies, thus allowing for more precise weld control. The selection of these specific frequencies depends on the particular welding requirements and application scenarios.
Inserting ultrasonic welding is commonly used for inserting threaded inserts, studs or other hard materials into plastic components. Under the action of ultrasonic vibration and pressure, the plastic melts and forms around the insert to create a solid bond. This method is often used to manufacture plastic parts with embedded metal inserts, such as plastic parts with metal screws, to achieve a more robust connection.
Staking is a method of connecting two or more parts together. In plastic staking, plastic staking pins or pillars are usually used. Through the effect of ultrasonic energy, the ends of the pins or pillars will melt and fuse with the connected parts to form a robust connection. This method is suitable for applications requiring high-strength connections, such as automotive components, electronic device housings, etc.
Spot welding is a localized ultrasonic welding technique used to create small area bonds at specific locations on plastic components. During spot welding, ultrasonic energy is only concentrated at the tip of the welding head, causing the plastic at the contact point to melt and solidify. This method is suitable for applications requiring precise control of welding locations and strength, such as assembly of small electronic components and manufacturing of medical devices.
Swaging is a method of changing the shape of plastic parts through compression and deformation. In ultrasonic swaging, the plastic part is placed in a die and then ultrasonic vibration energy is applied. This energy causes the plastic material to deform within the die to form the desired shape or dimension. Swaging can be used to manufacture complex shapes, increase part thickness or change material characteristics.
Ultrasonic welding machines can complete welding work in an extremely short time, with pulse intervals of sound reaching thousands of times per second, far higher than conventional welding methods. This high-speed welding process means a significant improvement in production efficiency and reduction in production costs. In addition, since the welding process is rapid, it also reduces thermal deformation of workpieces during welding, further improving production efficiency.
The strength and sealability of ultrasonic welding joints are high and can withstand large tensile and pressure loads. This is because during the welding process, ultrasonic energy can vibrate and fuse the molecules of the material together to form a solid joint.
Ultrasonic welding is applicable to welding of various materials, including metals, plastics, fibers and non-wovens. It can also realize welding of parts with different shapes and sizes
No smoke, toxic gases or other hazards are produced during ultrasonic welding, which is harmless to the environment and human health. Additionally, ultrasonic welding does not require the use of welding rods or wires, thus reducing waste generation.
Ultrasonic welding can achieve precision welding, and the accuracy and appearance of the welded joints are very high. This is because ultrasonic energy can precisely control the temperature and pressure in the welding area to achieve high-quality welding.
Ultrasonic welding equipment can be integrated with automated production lines to achieve automated production. This not only improves production efficiency but also reduces labor costs and workload. At the same time, automated welding can also reduce the problem of unstable welding quality caused by human factors and improve the consistency of welding quality.
Ultrasonic welding equipment is simple to use and operate, and does not require professional technicians. No additional welding materials or adhesives are needed during welding.
Ultrasonic welding produces durable seals that can withstand high pressures, suitable for waterproof products. This is achieved by melting materials through molecular friction.
Compared with other techniques such as thermal welding, very little heat is generated during ultrasonic welding. It takes advantage of high energy efficiency. Meanwhile, this can maximize the reduction of thermal stress deformation of thermoplastic components.
Although ultrasonic welding can reduce costs in the long run, the initial equipment investment may be high, especially for high-power equipment. The cost will be even higher if automated equipment is involved. In addition, equipment maintenance and servicing require certain costs and time investment.
The quality of ultrasonic welding is greatly affected by the materials. There may be differences in weldability performance between different materials, which requires testing and optimization.
While ultrasonic welding can be applied to many materials, the welding effect may not be ideal for some special materials, such as brittle materials. Additionally, limitations of ultrasonic metal welding are more significant, usually only thin metal foils or fine metal wires can be welded, and it may be difficult to achieve ideal welding effects for thicker or larger metal pieces.
Ultrasonic welding produces piercing noise, especially when large workpieces are welded, the noise may be greater. This may adversely affect the working environment and operators’ health. Soundproof casings can be added to machines to reduce noise, but this may also increase equipment costs and complexity.
Ultrasonic welding requires control of many parameters such as vibration frequency, amplitude, welding time, pressure, etc. Improper operation may lead to degradation of welding quality. Significant testing and process parameter adjustments are needed to achieve optimal welding effects, increasing process complexity and uncertainty.
Ultrasonic welding has certain size and thickness limitations for workpieces, which can’t exceed a certain range, otherwise welding quality will be affected. The welding size of standard ultrasonic machines usually has an upper limit. Non-standard ultrasonic machines or other welding processes need to be considered if the size of welded workpieces exceeds this range.
Ultrasonic welding typically can only form point or linear joints. Other welding methods may need to be used for complex shaped parts.
When welding using ultrasonic technology, the compatibility of materials is a primary concern. If materials are incompatible, even if they are melted together, there will be no bonding between molecular bonds, and good adhesion will not exist. Like polypropylene and polycarbonate can never be welded together. Similarly, only amorphous polymers with similar properties have a good chance of bonding to each other, while semi-crystalline materials can only be welded to themselves. Common materials suitable for ultrasonic welding processes include plastics, metals, composites, etc.
All thermoplastics can be connected using ultrasonic welding. The most common ultrasonic welding plastics include PP, ABS, SAN, PS, NYLON, PC and so on. However, it is recommended to weld between the same materials. Different plastics have different melting points and welding characteristics. Suitable welding parameters and processes need to be selected according to the specific material type when using an ultrasonic welding machine to ensure welding quality and efficiency.
Ultrasonic welding can quickly connect metal materials like aluminum, copper, steel, titanium, nickel, tin etc. without using welding wire or rods. However, it is mostly applicable to welding between thin metal sheets.
Ultrasonic welding can achieve material connections without damaging composite materials, such as carbon fiber reinforced plastics (CFRP), glass fiber reinforced plastics (GFRP), etc.
Ultrasonic welding can also be used for connecting other materials such as non-woven fabrics and leather. Something like the main body and straps of a mask are ultrasonically welded.
Selecting the correct ultrasonic welding frequency is a comprehensive process that involves multiple factors. The following are some key guiding principles:
Different materials have different characteristics in absorbing and transmitting ultrasonic energy. Generally, harder and higher density materials require lower frequencies, while softer and lower density materials can use higher frequencies.
Weld thickness also affects frequency selection. Thicker materials typically require lower frequencies as lower frequencies can provide larger amplitudes for better material penetration. Thinner materials can use higher frequencies to achieve finer weld control.
Welding requirements also impact frequency selection. Lower frequencies are generally selected if high strength welds are required. Higher frequencies can be selected if high precision welds are needed.
The size and shape of workpieces also affect ultrasonic welding frequency selection. Larger workpieces may require lower frequencies to provide sufficient energy for welding, while smaller or more delicate workpieces may be more suitable for high frequency welding.
Ultrasonic welding equipment of different frequencies have different cost and performance characteristics. Frequency selection needs to balance equipment purchase and maintenance costs against production needs.
Testing and experience can help determine the optimal ultrasonic welding frequency. It is recommended to do some tests when selecting a frequency to evaluate weld effects at different frequencies and adjust accordingly based on actual conditions.
For welding tasks requiring high precision, such as electronics or medical device manufacturing, higher ultrasonic frequencies are generally preferable as they can provide more precise energy transfer and smaller weld areas.
The ultrasonic welding of dissimilar plastics is the process of connecting two different types of plastics together through ultrasonic welding technology. Different plastic materials have different melting points, physical properties and chemical properties. Therefore, when performing ultrasonic welding of dissimilar plastics, special attention needs to be paid to selecting suitable welding parameters and processes. There are considerations in ultrasonic welding of dissimilar plastics:
Different types of plastics may have different chemical properties and physical properties. It needs to be ensured that they can be mutually compatible during the welding process. If the chemical properties of the two plastics differ greatly, it may be necessary to add a certain amount of compatibilizer or adhesive during welding to improve their adhesion. It is possible to weld two different plastics as long as their properties are compatible. For example, ABS can be firmly welded with PMMA, PC.
Different types of plastics have different melting points. Suitable welding parameters need to be selected to ensure that the plastics can be sufficiently softened and undergo plastic deformation during welding.
Different types of plastics have different thicknesses. Suitable welding parameters need to be selected to ensure welding strength and stability.
A reasonable head design can reduce stress concentrations during welding and improve welding quality. Special head forms or transition layers may need to be adopted for welding dissimilar plastics to optimize welding effects.
Ultrasonic Weldability Compatibility Chart for Thermoplastics | ||||||||||||||||||||
ABS | ABS/PC | POM | PMMA | LCP | NYLON | PC | PBT | PET | PEEK | PEI | PE | PPO | PPS | PP | PS | PSU | PVC | SAN | K-Resin | |
ABS | ||||||||||||||||||||
ABS/PC | ||||||||||||||||||||
POM | ||||||||||||||||||||
PMMA | ||||||||||||||||||||
LCP | ||||||||||||||||||||
NYLON | ||||||||||||||||||||
PC | ||||||||||||||||||||
PBT | ||||||||||||||||||||
PET | ||||||||||||||||||||
PEEK | ||||||||||||||||||||
PEI | ||||||||||||||||||||
PE | ||||||||||||||||||||
PPO | ||||||||||||||||||||
PPS | ||||||||||||||||||||
PP | ||||||||||||||||||||
PS | ||||||||||||||||||||
PSU | ||||||||||||||||||||
PVC | ||||||||||||||||||||
SAN | ||||||||||||||||||||
K-Resin |
Ultrasonic welding has advantages such as low cost, automation, short cycle time and flexibility. This has led to its wide range of applications across many industries. Common applications of ultrasonic welding include:
Many automotive plastic parts adopt ultrasonic welding for connections. like car doors, dashboards, bumpers, headlights, fuel tanks, and automotive interiors, engine components.
In the medical industry, ultrasonic welding is used to manufacture various medical products such as catheters, dialysis tubes, masks, air filters and plastic textile clothing. This is because ultrasonic welding does not involve adhesives or generate dust, making it particularly suitable for the manufacturing of medical products requiring high cleanliness. Additionally, ultrasonic welding can also be used to manufacture medical plastic containers such as infusion bottles and blood bags to ensure the sealing performance and pressure resistance of the containers, thereby ensuring the safety and reliability of medical devices.
Ultrasonic welding is widely used in the electronic and IT industry to connect electronic components such as microchips, micro conductors, computer hard disk drives, etc. Due to the possibility of damaging small wires and circuits through vibration welding, ultrasonic welding presents no such problem, making it the ideal choice for connecting these sensitive components.
In the packaging industry, ultrasonic welding is commonly used to seal containers, envelopes and cardboard boxes to form robust bonds. This technology is particularly suited for products requiring air-tight sealing, such as those containing hazardous materials or high-value products, in order to improve retail safety.
Ultrasonic welding is also used for a range of consumer goods industries, including fireworks, lighters, milk boxes, assembly of dangerous materials such as explosives or active chemicals. The inner shells of the especially popular “Gatling” fireworks in recent years are assembled using ultrasonic assembly processes.
Proper design must be carried out at an early stage of product design in order to apply ultrasonic welding for assembly. Ultrasonic welding design requires comprehensive consideration of multiple factors such as materials, joints, welding parameters and equipment.Here are some key points to consider when designing for ultrasonic welding
Ultrasonic welding is applicable to most thermoplastics, but the welding performance of different materials varies. Factors like melting point, hardness, and resilience of materials should be considered to ensure welding quality.
The design of ultrasonic welding joints needs to consider factors such as welding area, welding depth, welding angle. The shape and size of the joint greatly affect the welding effect. Generally, larger welding area means higher welding strength; deeper welding depth also means higher welding strength; the welding angle is usually between 60°-90°. Joint design should be simplified as much as possible to reduce stress concentration and energy loss.
Ultrasonic welding surface should be flat as possible, with no sharp angles if irregular. This can avoid damage to product surfaces caused by mismatches between the shapes of welding molds and products themselves. The reasons for such situations include flexing of molded parts, inaccurate shrinkage matching, or poor quality of welding molds.
Ultrasonic welding parameters include welding time, welding pressure, welding frequency. Selection should be based on material characteristics, joint design, product size etc. to ensure welding strength.
Welding mold design considers welding surface shape, size, accuracy etc. Mold material should also consider numbers to be welded.
Ultrasonic welding generates high-frequency vibration and noise, so safety factors like prevention of harm to human body should be considered.
Choosing a suitable ultrasonic welding equipment is critical to ensure welding quality. Equipment power, frequency and amplitude parameters need to match welding requirements. Stability and precision should also be considered.
Welding quality needs strict control during ultrasonic welding. This includes checks on joint appearance, dimensions, strength and sealing. Welding parameters or other remedies should be adjusted promptly if quality is found to not meet requirements.
The ultrasonic mold is an indispensable part of the ultrasonic welding process, and its material selection will directly affect the quality and efficiency of welding. When choosing an ultrasonic mold material, factors such as production order quantity, product material, precision requirements, processing difficulty and cost should be comprehensively considered according to the specific situation. When the quantity is large, the requirements are high and long service life is needed, it is recommended to use titanium alloy to manufacture ultrasonic molds, while aluminum alloys with good cost performance can be selected for medium quality products. These are common ultrasonic mold materials:
Aluminum alloy is one of the most commonly used materials for ultrasonic molds. It has good thermal conductivity and wear resistance, suitable for welding most plastic materials.
Titanium alloy has higher strength and corrosion resistance, suitable for welding high-strength plastic materials and plastics used in harsh environments. It has high machining accuracy, stability, durability, but also has a higher cost.
Stainless steel has good wear resistance and corrosion resistance, suitable for welding high-precision plastic products and plastics used in humid environments.
Tungsten steel has extremely high hardness and wear resistance, suitable for welding high-hardness plastic materials and plastics used in high temperature environments.
Copper alloy has good thermal and electrical conductivity, suitable for plastics with higher thermal conductivity requirements.
In the design of molded parts with ultrasonic welding, the triangular section on the welding joint is used to concentrate ultrasonic energy and melt the connecting surfaces. The following is common joints using energy directors include:
A butt joint directly connects the ends of two components to form a flat connection. This joint is commonly used to connect two flat or approximately flat components. The advantages of a butt joint are simple production and low cost, suitable for situations with low welding strength requirements. However, due to its large contact area, it is easy to produce a large heat concentration, which may cause unstable welding quality in some cases.
A step joint is suitable for situations requiring high welding strength and stability. It is a joint that connects the ends of two components in a stepped shape. This joint is commonly used to connect components with different thicknesses or heights. This design can also effectively disperse heat during welding and reduce the risk of heat concentration.
A tongue and groove joint achieves connection by inserting the tongue of one component into the groove of the other component. This joint is commonly used to connect two components that require precise alignment. The tight fit formed after the tongue inserts into the groove improves welding strength and sealing. This design is suitable for situations with high requirements for sealing and strength of the welded joint, such as liquid containers or pipes.
A criss-cross joint connects two components in a crisscross pattern. This joint is commonly used to increase the strength and stability of the connection.
A textured surface joint increases the frictional force and stability of the connection by creating textures or patterns on the connecting surfaces. Surface texturing joints are suitable for situations with high stability and reliability requirements for welded joints in harsh environments.
A perpendicular joint connects two components perpendicular to each other. This design can achieve more uniform propagation of ultrasonic energy at the joint, helping to improve welding quality. Perpendicular joints are relatively complex to produce and have higher costs.
An interrupted joint creates an interrupted connection form on the connecting surfaces. These interruptions can act as channels for the escape of gas bubbles or molten material during welding, helping to reduce welding defects and stress concentration.
A chisel joint is a joint that is connected by using a chisel to create grooves or protrusions on the connection surface. It allows the ultrasonic energy to be better focused and spread at the joint by designing the contact surface of the parts to be welded into an oblique shape.
A shear joint achieves connection by applying shear stresses to the connecting surfaces. This joint is commonly used to connect two thin and resilient materials.
Ultrasonic welding is a mature and widely used solid state welding technique. It has advantages such as simplicity, no pollution, and high joint strength. It is widely used in the assembly of products in industries such as electronics, communications, medical equipment, automobiles and more. In this article, we analyzes the working principles and key influencing factors of ultrasonic welding and explores the advantages of different joint designs in improving welding quality. The goal is to help you systematically understand ultrasonic welding technology.
Are you looking for quality welding of plastic and metal parts? Contact us now and let us help you produce competitive priced products with confidence in quality.
Ultrasonic welding can provide water resistance, but the level of water resistance depends on various factors such as the size and structure of plastic parts, plastic materials, welding parameter settings, etc.
Ultrasonic welding itself is not dangerous. But during welding, earplugs need to be worn to avoid excessive noise stimulating the ear tissue. The main working principle of ultrasonic welding equipment is to tightly bind two parts needed for welding through high-frequency vibration energy. This process does not involve the generation or release of hazardous substances.
The maximum frequency used for ultrasonic welding is 70 kHz, and the minimum frequency is 15 kHz.
Generally can’t, because the melting temperature of high temperature plastics are generally more than 300 ℃, ultrasonic friction heat is not enough to melt these high temperature plastics, so can’t achieve the purpose of welding. Such as PTFE and PTFE can’t ultrasonic welding, PFA and PFA can’t be ultrasonic welded.