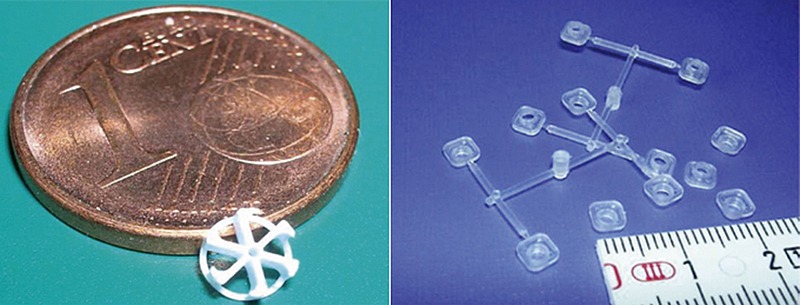
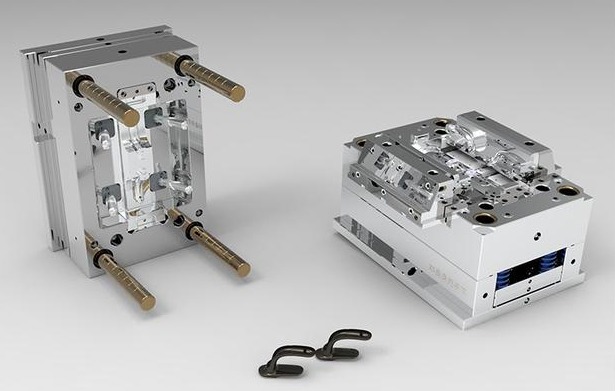
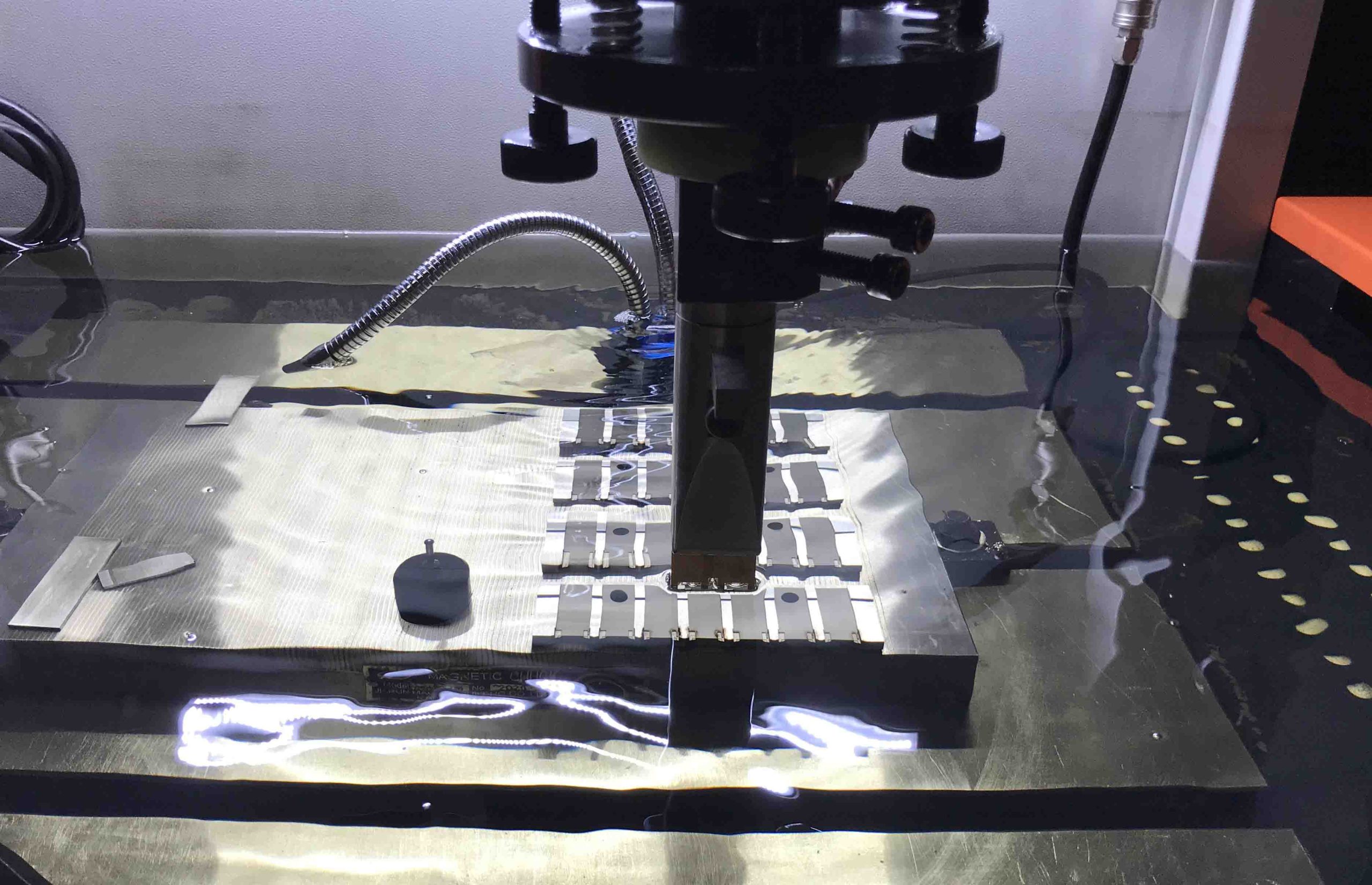
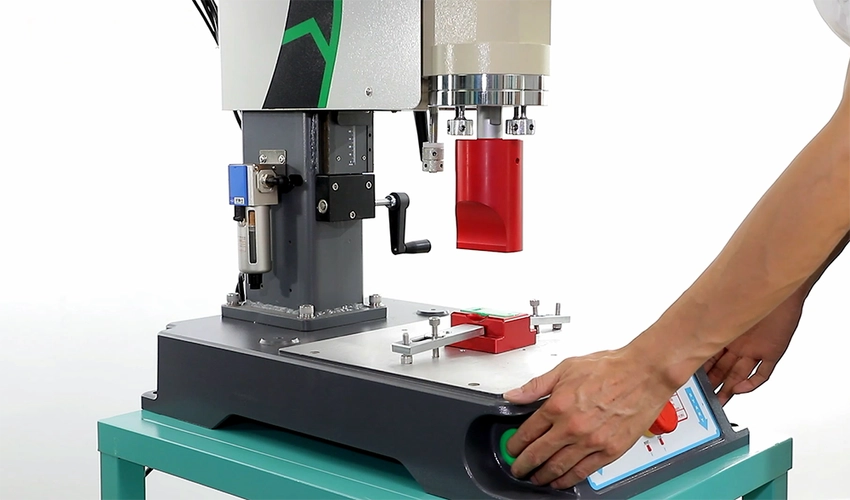
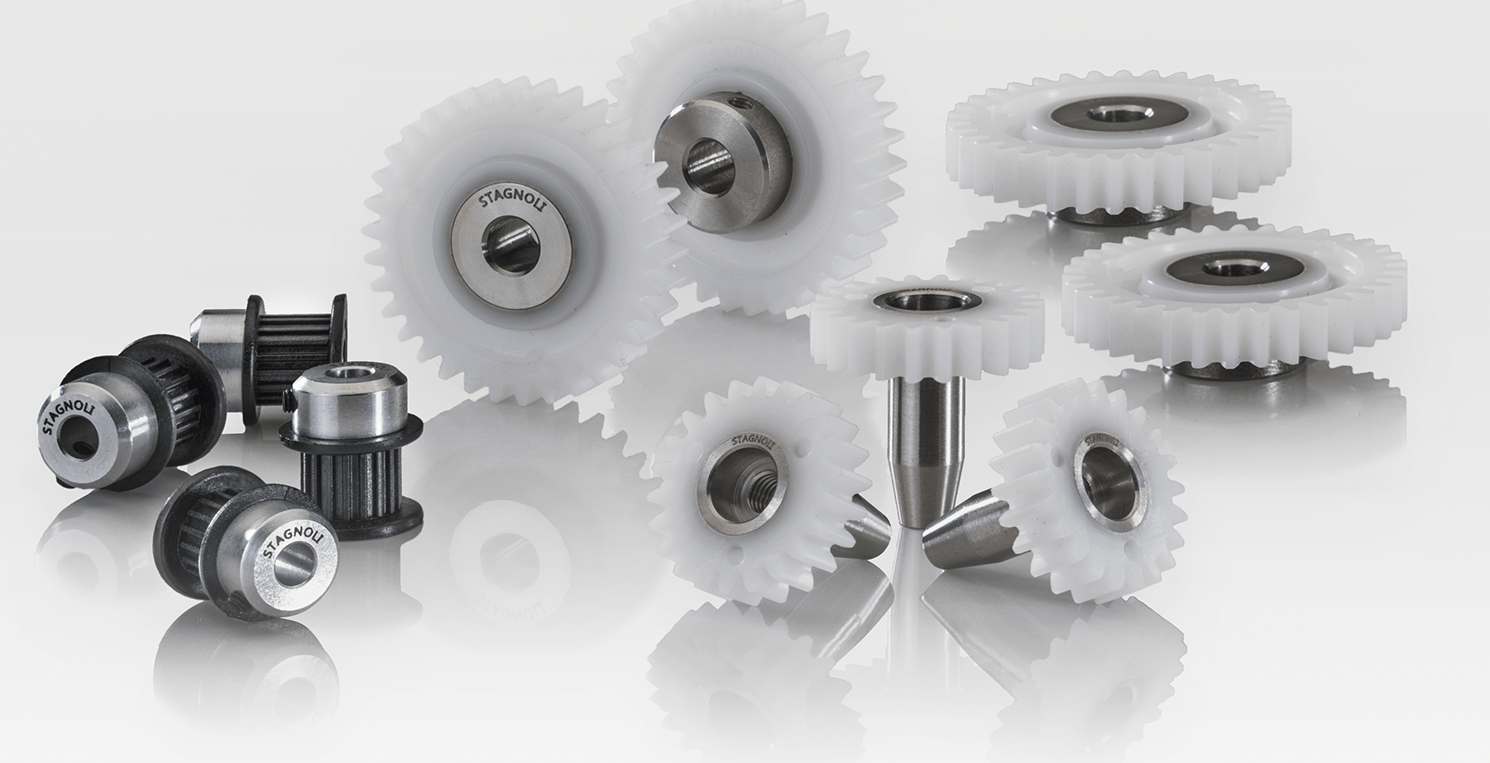
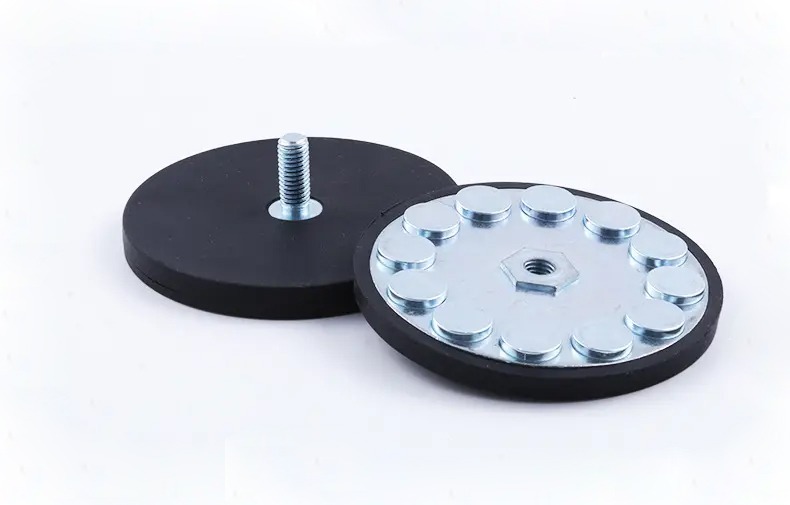
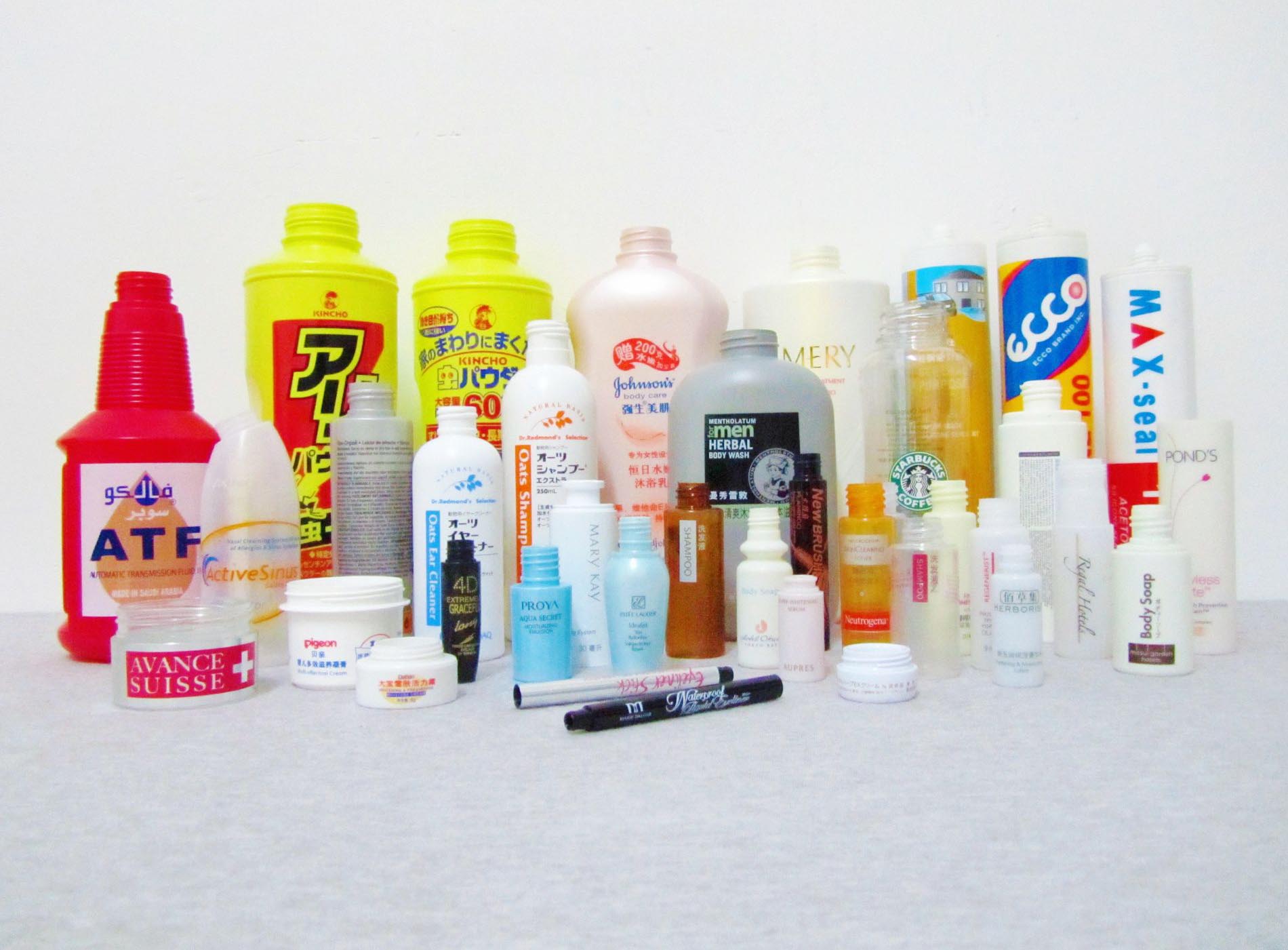
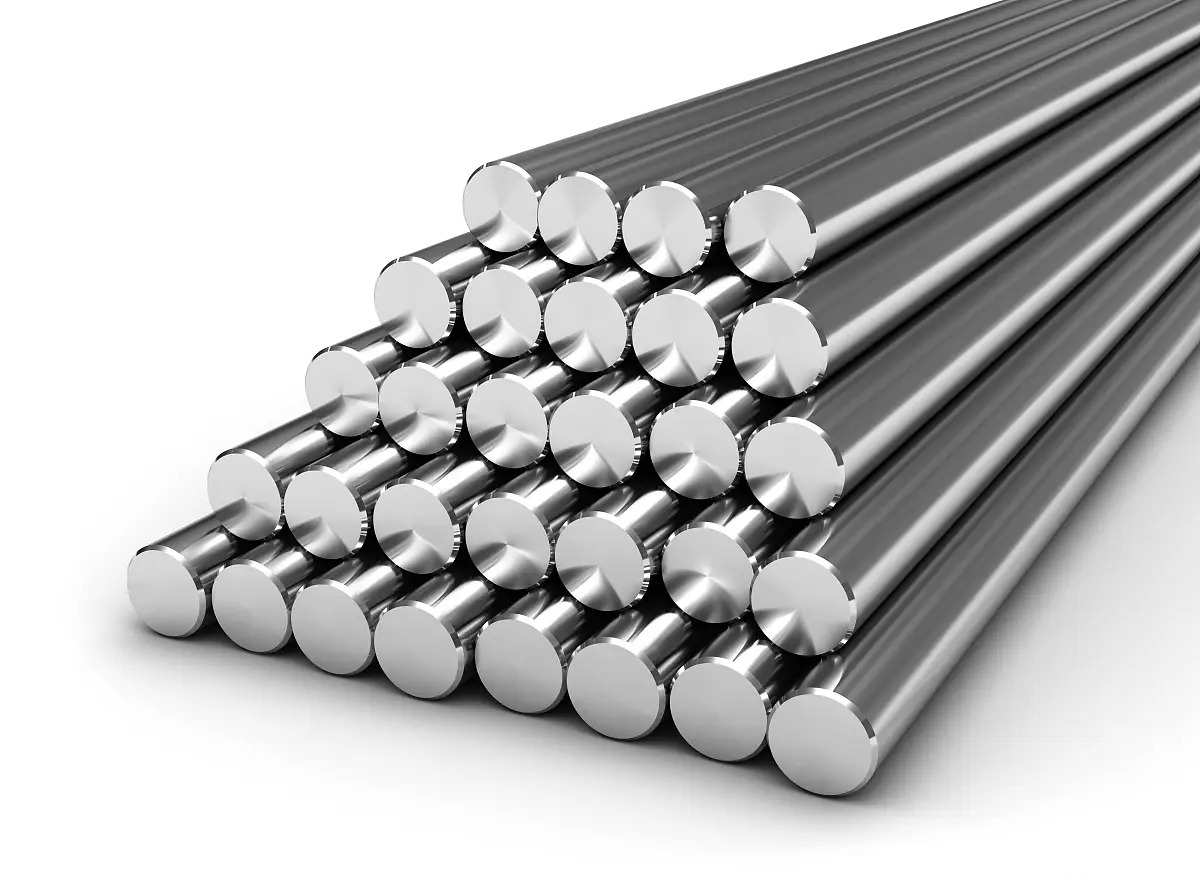
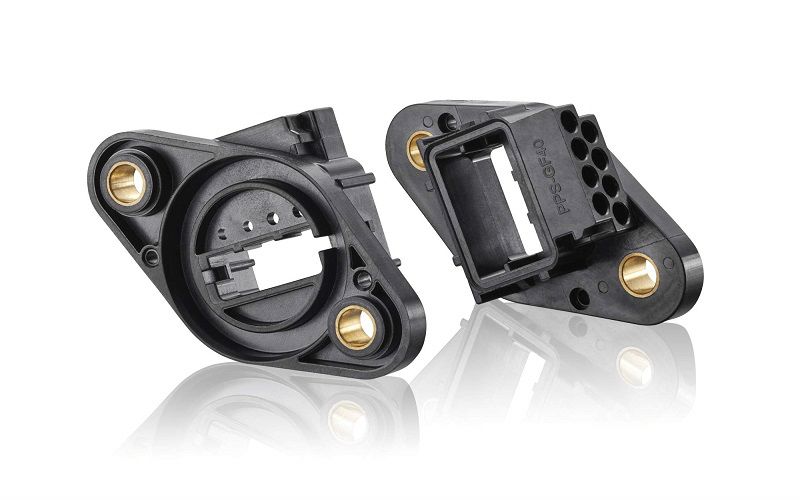
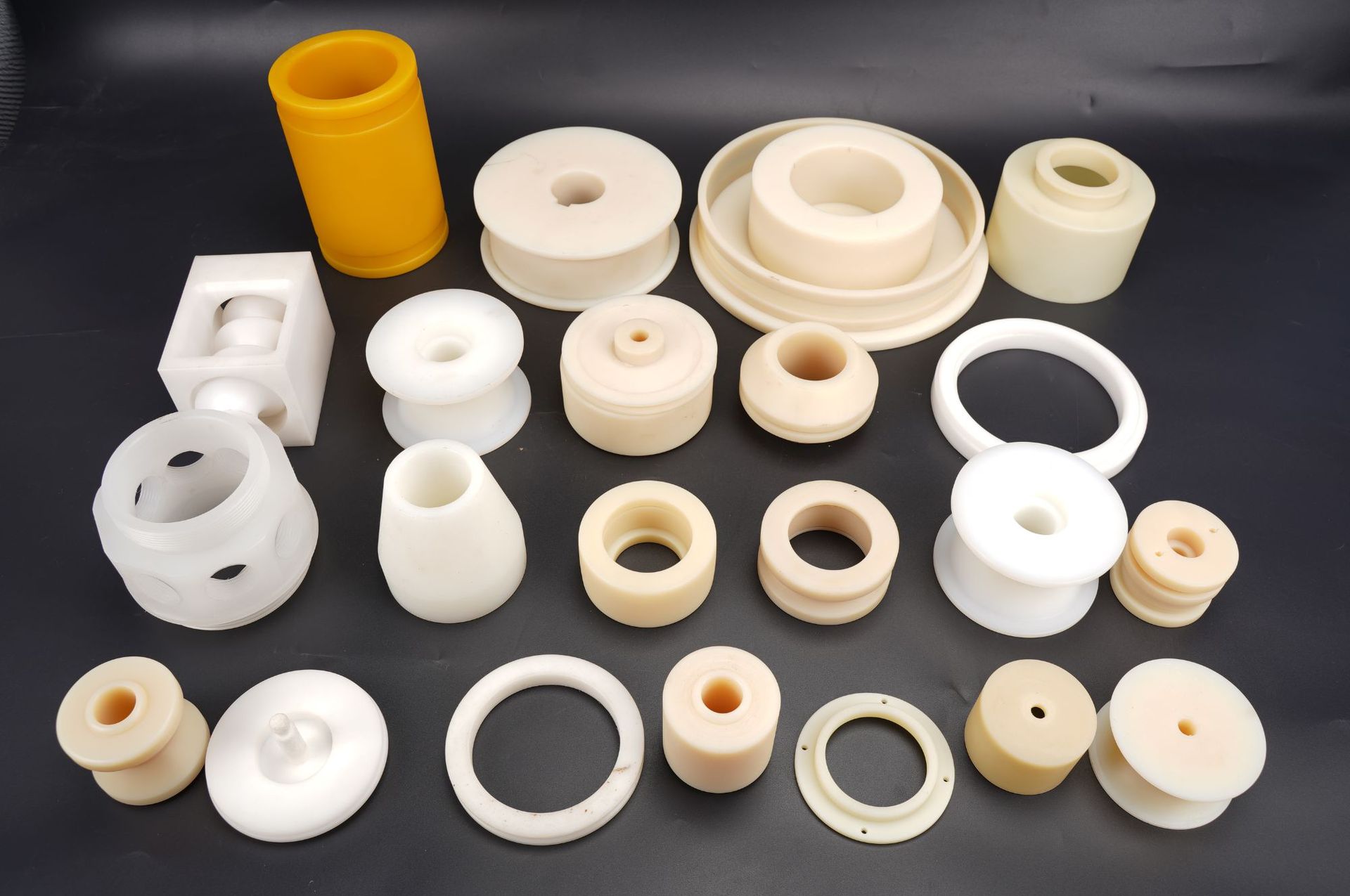
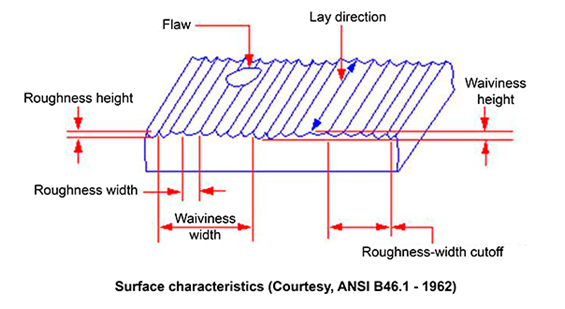
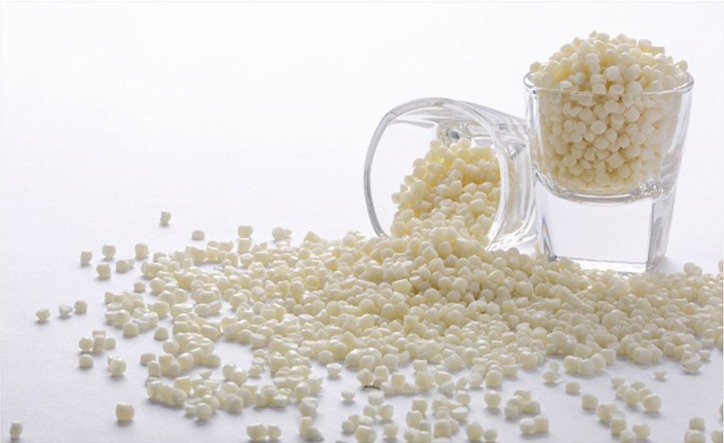
As a key field in modern manufacturing, micro injection molding technology has become increasingly important. Micro-molding is often used to make small parts with delicate features, thin walls, micro holes and tight tolerances. It is often used to make tiny electronic, medical and high-precision products such as automotive parts.
Microinjection molding is a highly specialized process that requires precise control and in-depth understanding. This article will give you an in-depth analysis of the principles, processes and applications of micro-injection molding to help you gain a deeper understanding of this delicate and complex technology.
Micro molding is a highly specialized manufacturing process used primarily to produce extremely small, high-precision thermoplastic parts and assemblies with micron tolerances. This technique involves using well-designed micro molds and micro injection machine to molding tiny plastic parts.
Micro injection molding is characterized by small injection volume, high injection pressure, precise mold temperature control, and good material fluidity. Micro-molding has higher requirements on mold design and manufacturing, and requires the use of high-precision CNC machine tools for processing.
In the micro injection molding process, materials usually enter the mold through high temperature and high pressure, waiting to cool and solidify. Since the part size is very small, injection speed and pressure need to be strictly controlled to avoid part defects such as sink marks, weld lines, etc.
Micro plastic parts, that is, tiny plastic parts, are plastic parts with tiny sizes manufactured through micro-injection molding or other micro-molding technologies. The size of microplastic parts is not fixed. The size of these micro-parts usually ranges from microns (μm) to several millimeters (mm), and the specific size varies depending on the application.
Some micro electronic components or micro medical device plastic parts may be only a few microns, and some micro plastic parts used in automotive parts or consumer products may be hundreds of microns to 1mm.
Micro injection molding is derived from conventional injection molding. Its principle is the same as traditional injection molding, that is, the plastic material is heated, melted, and extruded through the barrel and screw of the micro injection molding machine. Under the action of injection pressure, the molten material passes through the nozzle of the injection molding machine. The main channels, shunt channels and gates of the mold enter the mold cavity for molding, and then undergo pressure holding, cooling and demoulding to obtain the molded product. The molding process mainly includes five processes: plasticization, injection, pressure holding, cooling, and demoulding. Micro molds are the core of micro injection molding, and their accuracy directly determines the quality of injection molded parts. The cost and life of micro molds are key factors affecting mass injection molding production.
The plastic material selection for micro-molding should be determined based on specific application requirements, and factors such as material performance, processing technology and cost, and use environment need to be comprehensively considered. Micro-injection plastics should meet the special requirements of the micro-injection molding process, such as low viscosity, good fluidity, rapid solidification, and high dimensional stability. In addition, micro-injection molding also requires materials with good thermal and chemical stability to cope with the high-temperature and high-pressure environment during the micro-molding process. Common micro-molding materials include ABS, PEEK, PP, LCP, PET, PPS, PBT, POM, PEI, TPU, PPS, PPA, PSU, PC
Micro injection molding materials mainly include the following categories:
The 8 top considerations or tips for micro molding design are as follows:
The limitations of the micromolding process should be considered when designing micro plastic parts. The structure of the plastic part should be as simple as possible. Features like thin walls, small holes, or complex geometries can pose great molding challenges and may require special considerations in mold design or material selection.
Design for manufacturing (DFM) is essential in microinjection molding as it is the basis for ensuring parts, molds and processes. Manufacturers should ensure that parts can be molded easily and consistently while increasing production efficiency and reducing costs by considering DFM principles such as optimizing part geometry, material selection and mold design. and continues to produce high-quality micro-injection molded components.
Unlike conventional injection molding, the choice of plastic material is crucial for micromolding. Micro-injection molding raw materials must have excellent fluidity to enter tiny flow channels, low viscosity and high dimensional stability, while ensuring no loss of mechanical strength.
These commonly used thermoplastics include polyimide (PI), polyetherimide (PEI), polyetherketone (PEK), polyetheretherketone (PEEK), polysulfone (PSU), and polyphenylene sulfide (PPS) , liquid crystal polymer (LCP), cyclic olefin copolymer (COC), etc. Due to its excellent thermal and mechanical properties, it is more suitable for micro-molding.
The selected materials should also be compatible with the micromolding process, including molding temperature, pressure and cycle time
Mold designers need to consider factors such as mold materials, processing techniques, and mold structure. Mold parts may become extremely small due to their size, and there is a risk of failure. For example, core pins and ejector pins become more fragile and lose stiffness due to being too small. Plastics are also prone to burrs due to excessive shear rates.
When designing micro molds, attention should also be paid to the mold supporting system, cooling system and pouring system to ensure that the parts are correctly ejected, cooled and filled.
Mold flow analysis is essential for micro molds. The size of the micro mold runner is often in the order of tens of microns. It is necessary to optimize the gate position and runner structure through rheological analysis software to ensure that the melt can be fully and evenly injected into the mold cavity.
Because the cavity that needs to be processed in micro molds is extremely small, it needs to be manufactured with extremely precise processing equipment. Sometimes the depth of the flow channel is only a few microns, and CNC processing is also extremely difficult. Therefore, precision processing equipment must be used for mold processing. This is also The key to successful micro mold making.
Process optimization is an important part of micro-injection molding. Small changes in the injection molding process may lead to unqualified parts. The control of filling pressure and speed needs to be more precise. Improper setting of process parameters will directly affect product quality. The following factors are mainly considered:
Ultra-precision injection molding machines are the core equipment of micro-injection molding and need to have the characteristics of high precision, high stability and high repeatability. When choosing injection equipment, consider the following factors:
Because micro injection molded parts are so small, quality issues are difficult to detect and repair. Therefore, a strict quality control system needs to be established to ensure the quality of parts. Statistical process control (SPC) technology can be used to monitor and control the molding process to ensure consistency and repeatability.
Microplastic parts are difficult to observe directly due to their small size. Professional equipment such as optical microscope, scanning electron microscope (SEM) or X-ray computed tomography (CT) is required for non-destructive testing to evaluate the internal and external quality of microparts.
Because micro plastic parts are extremely small, both mold development and final production, including equipment, require careful exploration. Any small detail that is not carefully considered may lead to project failure. The following are 6 challenges of micro molding that we have summarized based on our more than 10 years of experience.
In terms of technical implementation, micromolding requires extremely high precision and stability. Since the physical and chemical behavior at the microscale is significantly different from that at the large scale, more precise control of molding process parameters is required. At the same time, the manufacturing of microstructures involves complex physical and chemical processes, such as melting, flow, solidification, etc. These processes are difficult to control accurately, making it more difficult to achieve dimensional control.
Material selection is also an important challenge. Micromolding has high requirements on materials, which require good fluidity, thermal stability and mechanical properties. However, the types of materials currently available are limited, and some specialty materials may be difficult to obtain or costly.
Mold making is also a challenge for micromolding. Due to the particularity of the tiny structure, the design and manufacturing of molds require extremely high precision and complexity. Mold processing requires precision processing such as laser cutting, EDM, etc., but these processes are still very difficult under micron-level structural dimensions. Small errors in the mold manufacturing process may lead to molding failure or product quality problems. Therefore, the improvement of mold manufacturing technology is crucial to the success of micro-molding.
Production process control is also an important challenge for micromolding. Parameters such as temperature, pressure, and speed during the micro-molding process need to be precisely controlled to ensure product quality and production efficiency. However, the adjustment and optimization of these parameters require a lot of experiments and experience accumulation, and require high technical level of operators.
In actual micro molding, the residence time of raw materials in the barrel is a key point. Due to the light weight of the part and the small injection volume required, the chance of thermal decomposition of the material is greatly increased when using a larger plasticizing device (injection molding machine).
Micro plastic parts are extremely small, and it is difficult to measure defects or dimensional deviations of parts through visual inspection or manual measurement. Microscopes and other advanced detection methods must be used for quality monitoring, and process monitoring and statistical analysis must be performed, which increases the difficulty. and cost.
In micromolding, mold design is a great challenge. Micron-level fine flow channels are more affected by fluid dynamics and are difficult to design empirically, so they need to be optimized using computational fluid dynamics. The same is true for the setting of the gate. The impact of gate marks on micro-molded parts is much greater than that on larger parts.
The development of micro injection molding equipment can be traced back to the 1980s, when some Japanese companies began to develop injection molding equipment for the production of micro parts. With the development of micro-electromechanical systems (MEMS) technology, the demand for micro-injection molding equipment has gradually increased, and companies from various countries have begun to join in the research and development and production in this field.
Starting in the mid-1990s, major machinery manufacturers began to develop specialized micro-injection molding equipment:
Some well-known micro injection molding machine manufacturers include:
On the surface, micromolding is not that different from traditional injection molding. The design department designs and prototypes plastic parts, then manufacturer making molds. An injection molding machine fills the mold with a high-pressure injection of molten plastic, and once the plastic cools and hardens, the part is ejected. Micromolding accomplishes the above in the same way, but each step requires careful validation and careful preparation for testing. This is different from traditional injection molding. The following is a summary of the differences between the two.
Micro-molded plastic products are mainly used to manufacture parts with dimensions in millimeters or even microns, while traditional injection molding is usually used to manufacture parts with dimensions above millimeters and centimeters. This puts forward higher requirements on material performance and molding process.
Micro-molding requires very high precision for parts, usually at the micron level, while traditional injection molding requires relatively low precision, usually at the millimeter level.
The cost of equipment and molds for micro-molding is usually higher, so the manufacturing cost is also relatively higher, while the cost of traditional injection molding is relatively low.
The raw materials selected for micro-injection molding emphasize good rheology and easy control of viscosity to meet the filling needs of micron-level fine channels. This is different from traditional injection molding requirements.
The flow channel depth of micro molds reaches the micron level and requires precision processing techniques such as laser cutting and chemical processing for manufacturing. This is more difficult than traditional CNC machining.
Micro injection molding machine sets higher standards for hardware configurations such as raw material delivery system precision and injection molding unit positioning accuracy to meet micron-level control requirements.
It is necessary to use microscopes and more advanced detection methods to detect micron size and surface quality, which is rare in traditional injection molding.
Micron-scale runner have a more complex impact on fluid flow, requiring the use of computational fluid dynamics for finely optimized design of the flow channel structure.
Micro injection molding has the advantages of high precision, high efficiency, high repeatability, design flexibility, material saving and wide application range, so it has great advantages in manufacturing micro parts.
Micro-injection molding can produce parts with very small sizes and very high precision, which makes it a great advantage in manufacturing micro electronic components, medical devices and other high-precision parts.
Micro-injection molding can achieve high-speed injection and rapid molding, thereby improving production efficiency.
Micro-injection molding can produce parts of various shapes and structures, which allows designers to design parts more flexibly to meet different needs.
Micro-injection molding can accurately control the injection volume, thereby reducing material waste and saving costs.
This technology can ensure product dimensional stability and high quality, meeting the needs of precision manufacturing.
Compared with conventional injection molding, micro-injection molding technology can reduce mold costs while reducing material waste, thereby reducing overall production costs.
This technology is not only suitable for small medical or technological products, but can also be used to form micro-nano structural surfaces with special properties, such as optical components, biomedical devices, gears, bearings, connectors, etc.
Micro-injection molding technology has the capability of automation and batch production, which helps to improve production efficiency and product quality stability.
This technology has a short molding cycle, can quickly respond to market demand, and improves production flexibility.
Although micro injection molding has the advantages of high precision and efficiency, it also has shortcomings such as high equipment cost, difficult processing, low output, limited material selection, and short mold life, which need to be comprehensively considered in practical applications.
Micro-injection molding requires the use of high-precision equipment and molds, which are usually expensive.
Since the size of micro-injection molded parts is very small, the difficulty in processing increases accordingly, requiring higher technical levels and more stringent processing techniques.
Micro-injection molding has high material requirements. Currently, there are relatively few types of materials available for micro-injection molding, which limits its application in certain fields.
Since the mold size of micro-injection molding is very small, the service life of the mold is usually short, and the mold needs to be replaced frequently, which increases production costs.
Micro-injection molding requires precise temperature, pressure and injection speed control, as well as higher requirements for equipment and technical personnel. In addition, the fabrication of micro-nanostructures involves complex physical and chemical processes, which increases the difficulty of technical implementation.
Since micro-injection molding requires the manufacture of high-precision molds, which usually involves precision machining and the use of special materials, the manufacturing cost of molds is high.
At the microscale, the flow, heat and mass transfer behavior of plastics can change, leading to instability and unpredictability during the molding process.
While micro-injection molding can achieve high efficiencies, production rates can be limited due to the need to precisely control injection speed and pressure when manufacturing tiny structures.
Tiny parts produced by micro-injection molding may be difficult to subsequently process or assemble, requiring special processing techniques and equipment.
Due to the complexity of micro-injection molding, quality control may be more difficult, requiring strict process parameter monitoring and sophisticated detection methods.
Micro molding technology has broad application prospects in the electronics, automotive and medical industries. With the continuous development and innovation of technology, micro injection molding will play an important role in more fields.
In the electronics industry, micro injection molding is widely used to manufacture various micro electronic components, such as connectors, sensors, micro switches, integrated circuit packages, etc. These micro parts often require high precision, high reliability and small size, and micro injection molding technology can meet these requirements.
Micro injection molding can also be used to manufacture micromechanical components such as micromotors, microgears, and micropumps, which play a key role in microelectronic devices.
In the automotive industry, micro injection molding is used to manufacture various micro automotive parts, such as fuel injectors, throttle valves, micro bearings, automotive sensors, etc. These micro parts need to have high precision, high strength and corrosion resistance, and micro injection molding technology can meet these requirements.
Micro molding can also be used to manufacture micro decorative parts inside automobiles, such as buttons, knobs, etc. on dashboards.
In the medical and healthcare industry, micro injection molding is used to manufacture various micro medical devices and equipment, such as micro scalpels, micro syringes, micro prostheses, micro diagnostic equipment, implants and prostheses, etc. The high precision, biocompatibility and micro size required of these micro medical plastic parts make them ideal for medical micro applications.
Mini-injection molding can also be used to manufacture micro-drug delivery systems, such as microcapsules, microspheres, etc., which can achieve precise delivery and controlled release of drugs.
Attractive Plastics acts as a reliable partner for comprehensive injection molding services. We have the necessary skills and expertise to ensure the quality of micro-molding. Backed by decades of experience and a team of knowledgeable engineers, our team has a deep understanding of micro plastic part design, materials, molds and micro molding processes.
We have experience in successfully producing many micro plastic parts used in medical equipment, robotics, pharmaceutical, industrial, automotive, and electronic industries. Our engineers will be eager to do whatever it takes to assist you with your micro project. Contact us today to learn more about micromolding and discuss the possibility of micromolding components to meet your needs.
Micro injection molding has experienced rapid growth in recent decades, driven by the miniaturization of technology in many industries. What was previously thought to be impossible to manufacture using traditional technologies can now be achieved through specialized micromolding processes, advanced processing methods and specialized machinery. While technical challenges remain in areas such as microscopic size control and optimizing tiny flow paths, the field continues to make progress through computational modeling, improved materials and metrology equipment. Going forward, micromolding will become an even more indispensable manufacturing solution as applications requiring micro-precision proliferate in areas such as electronic components, medical devices and sensing technology.