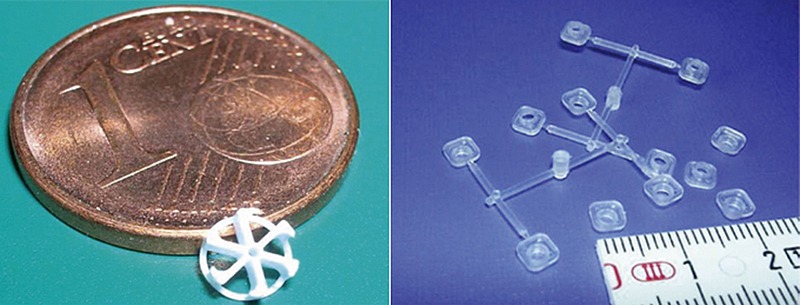
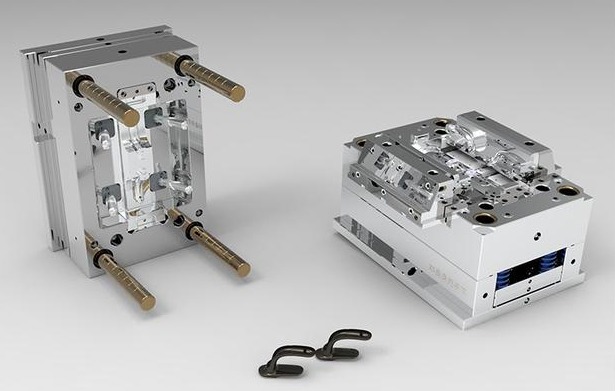
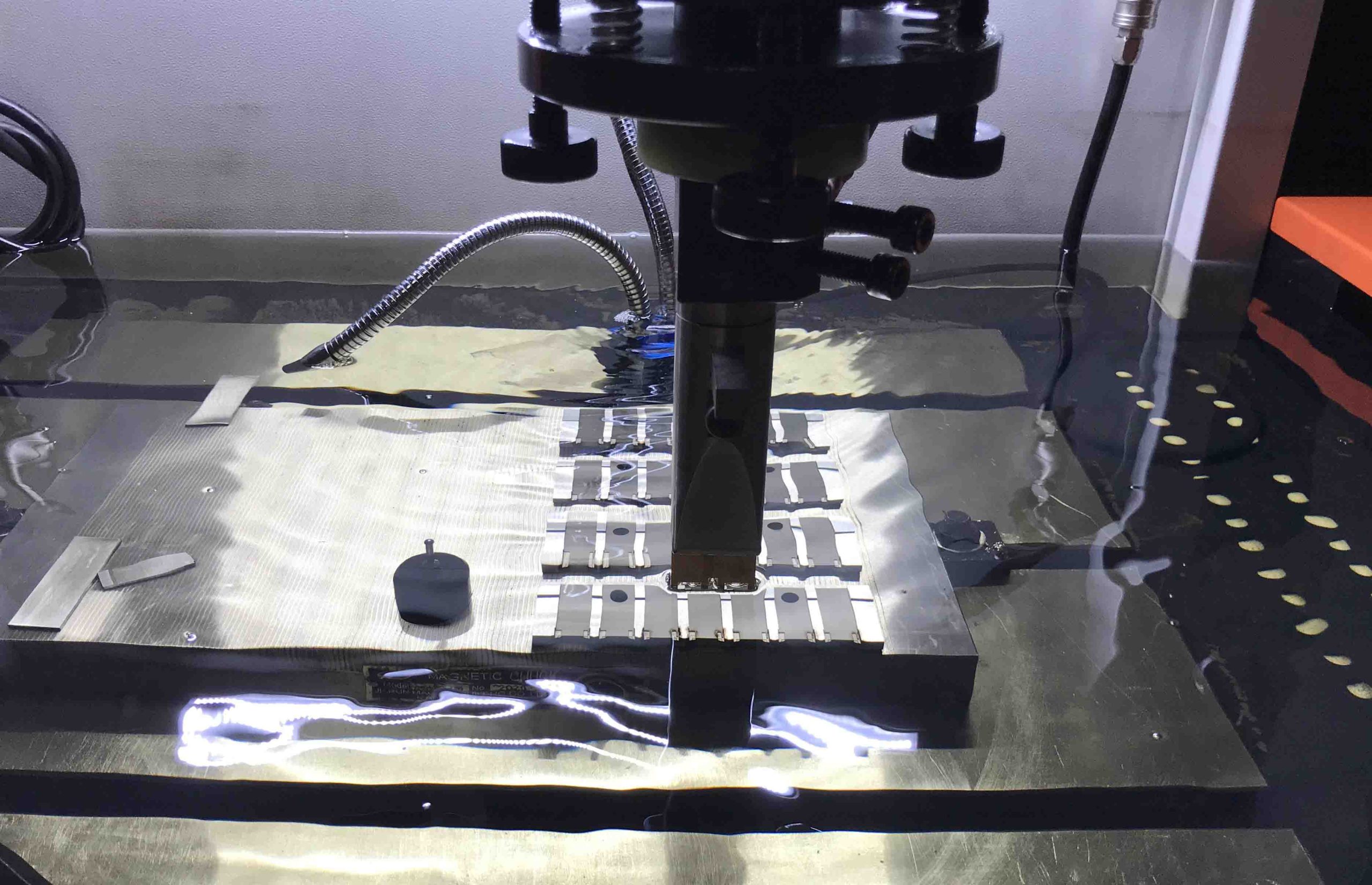
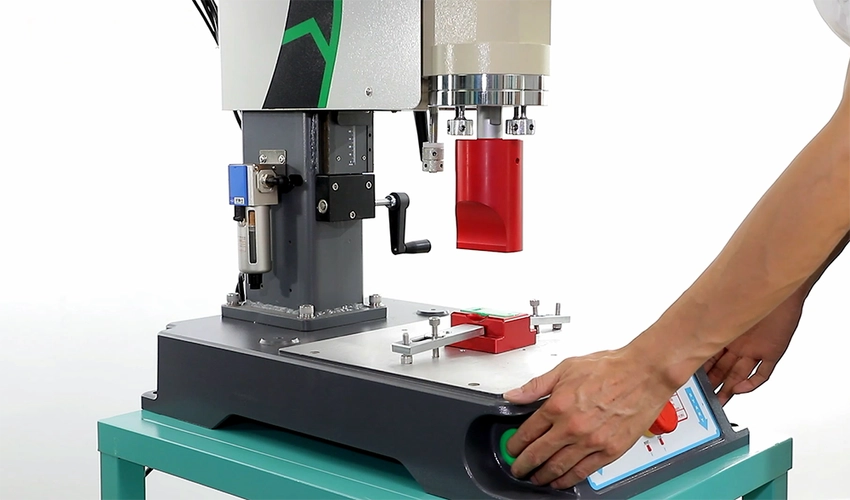
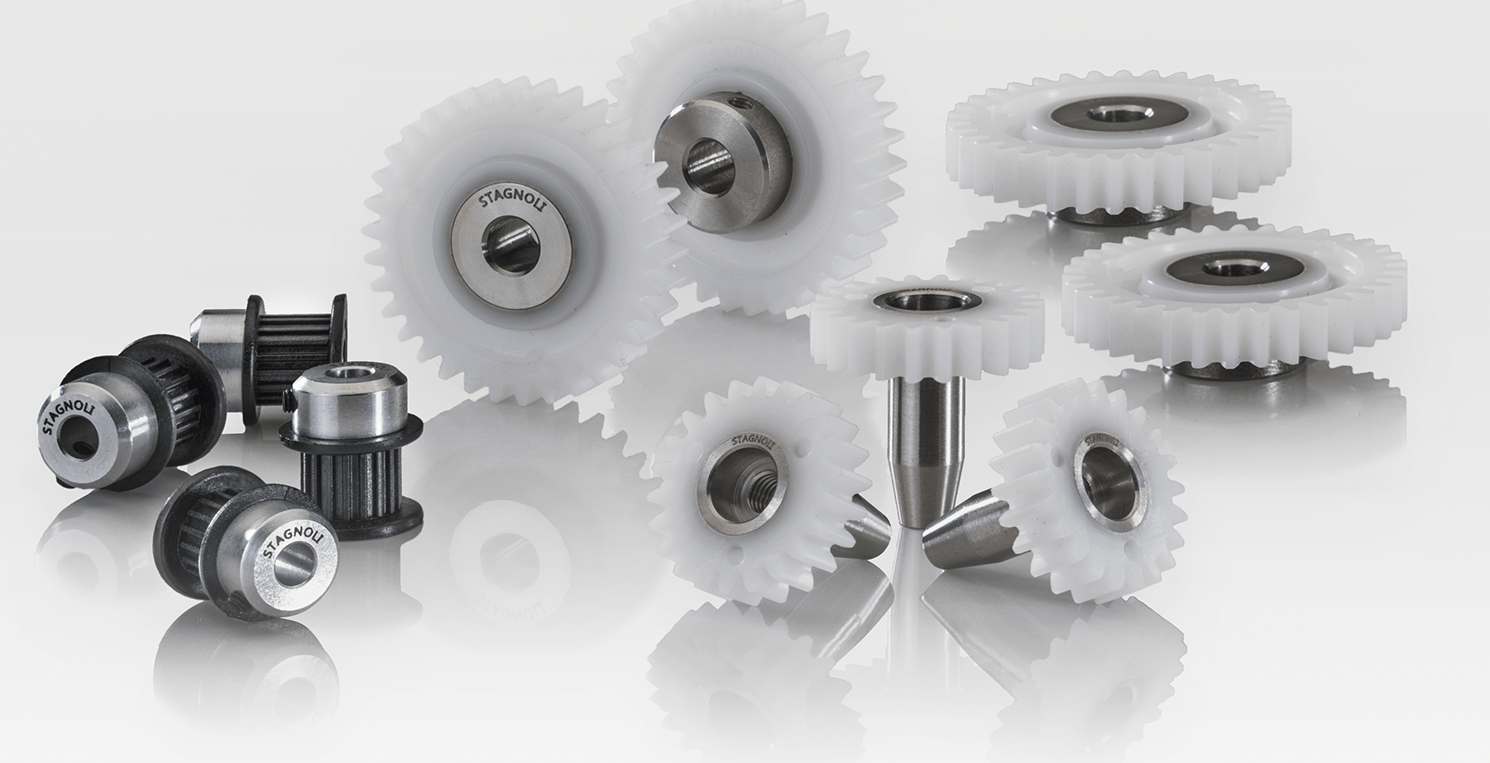
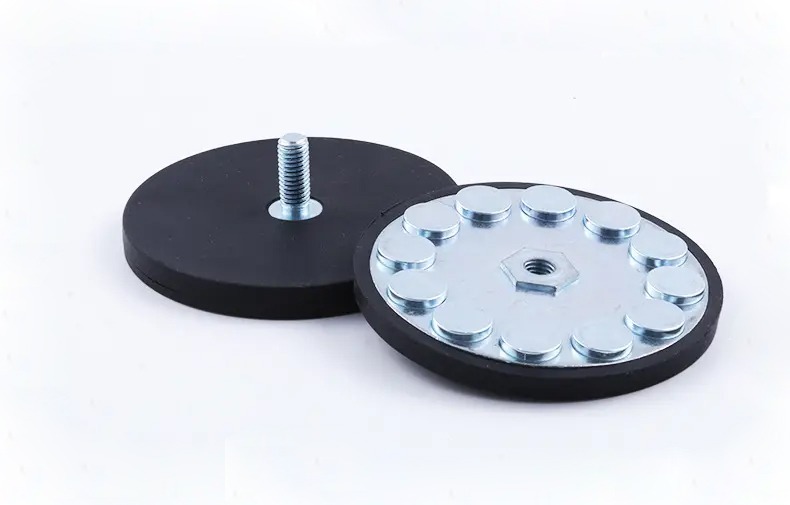
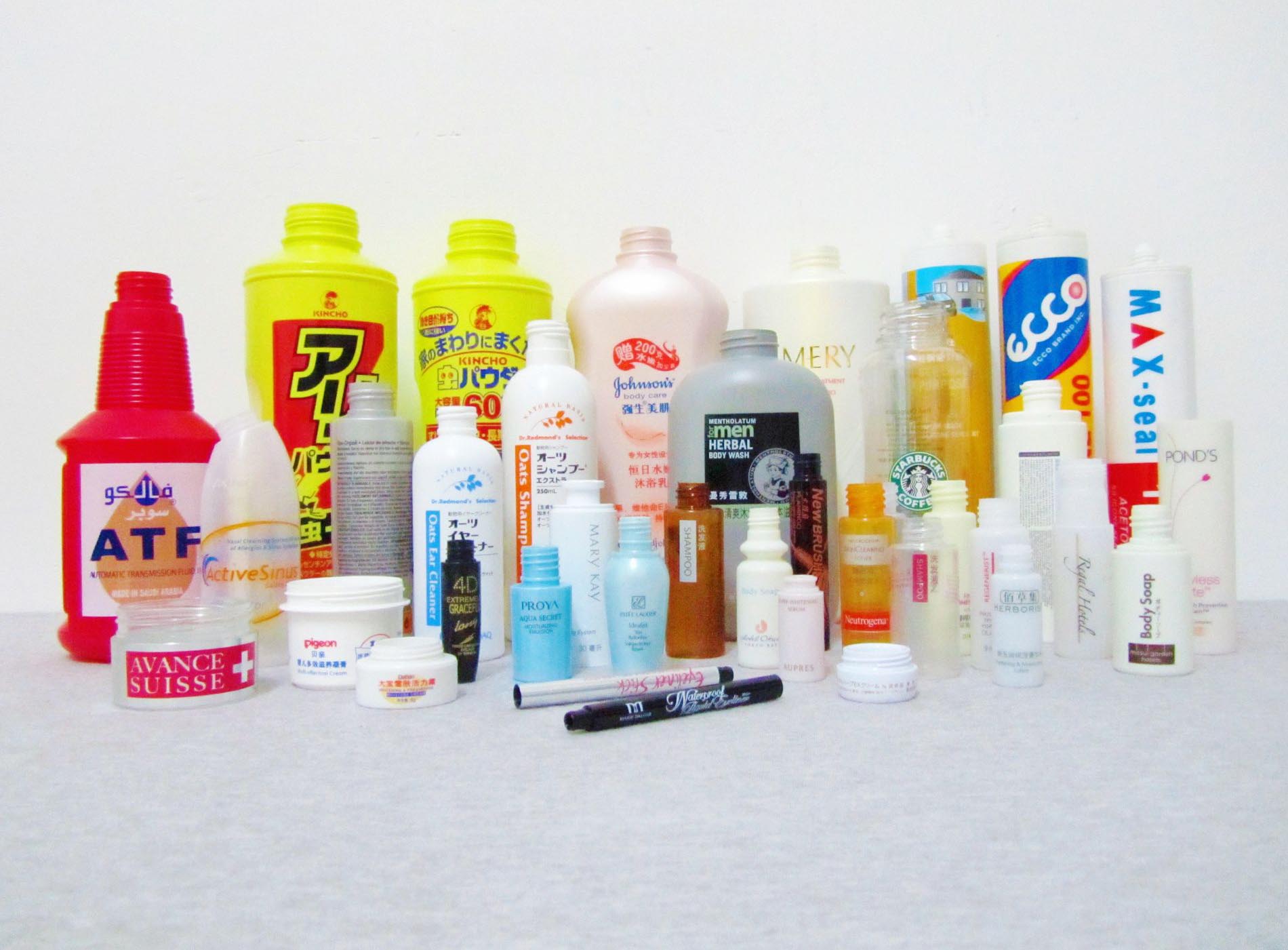
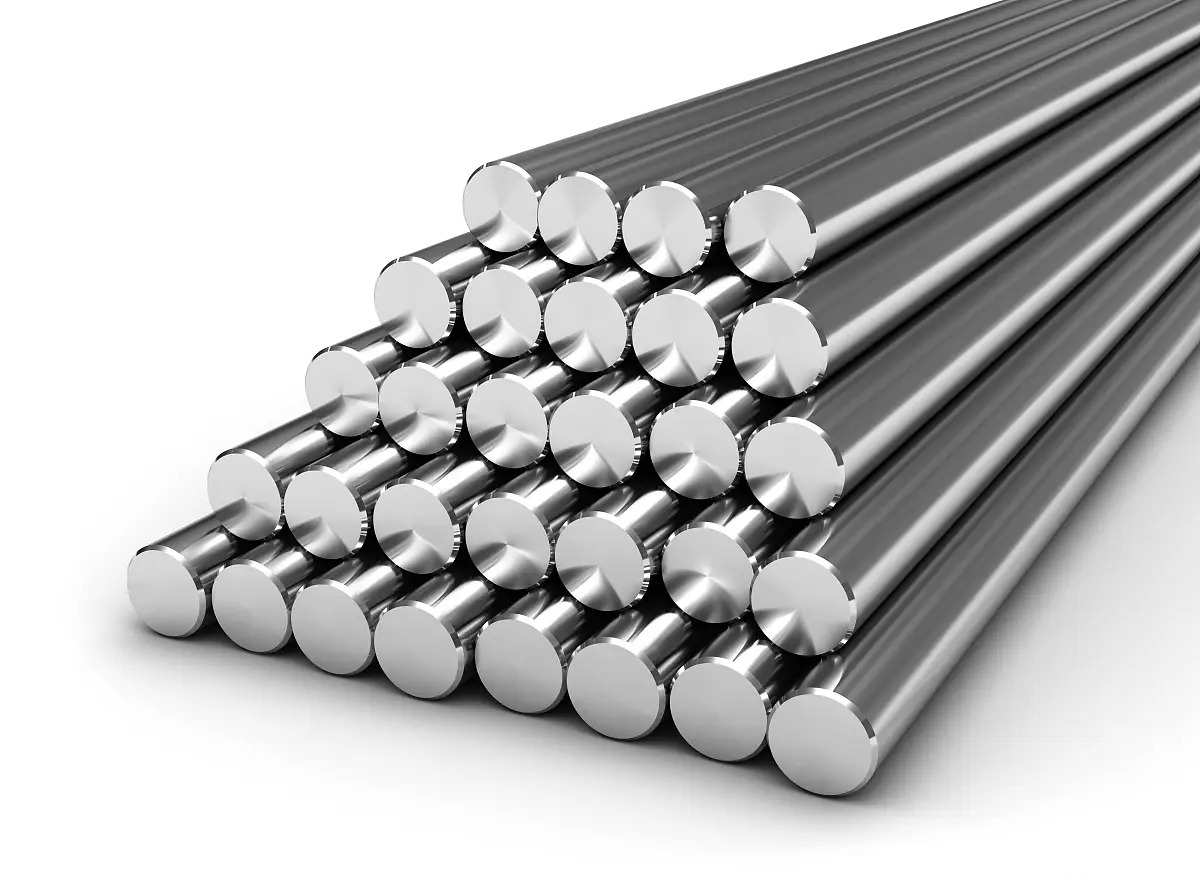
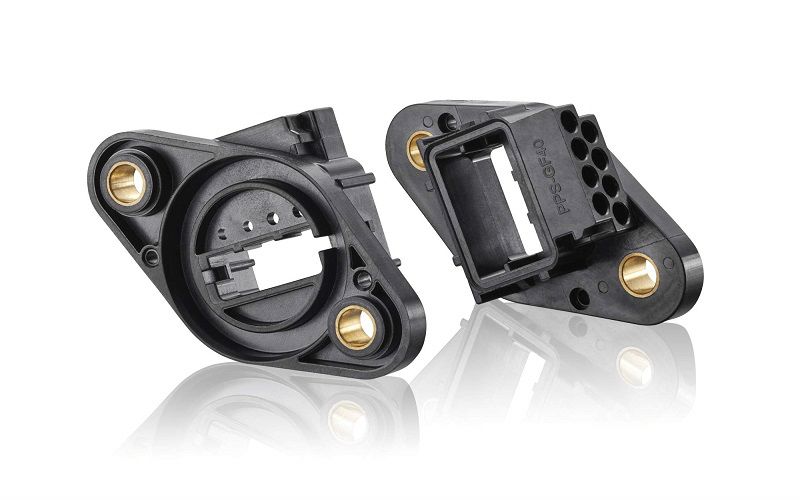
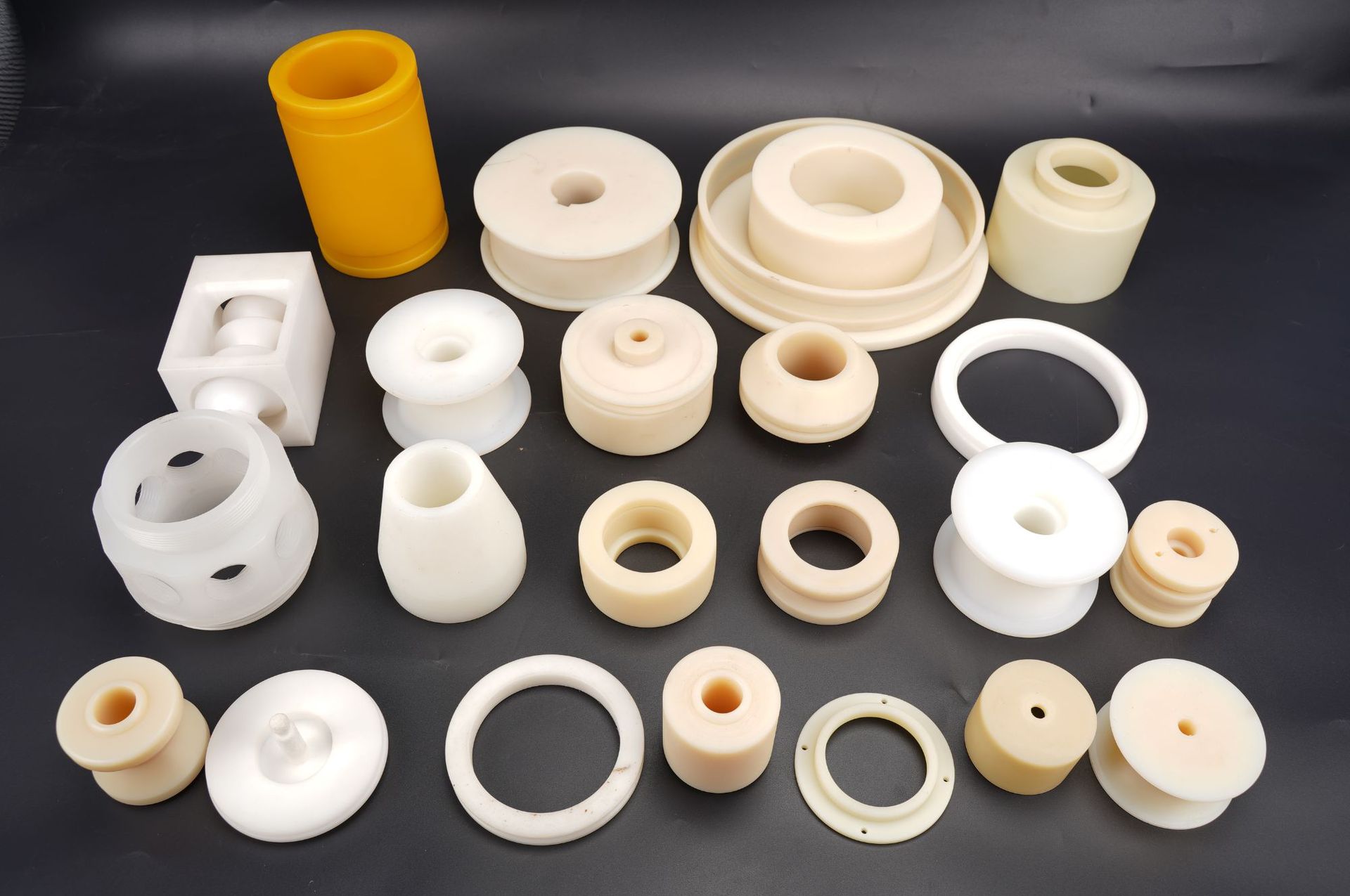
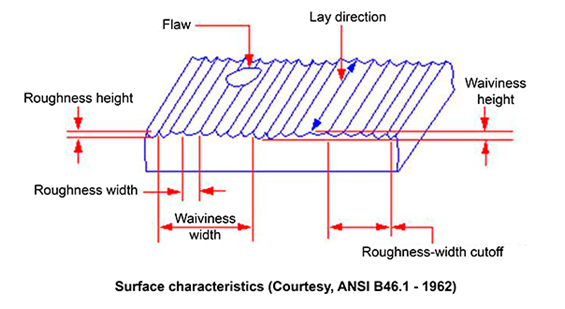
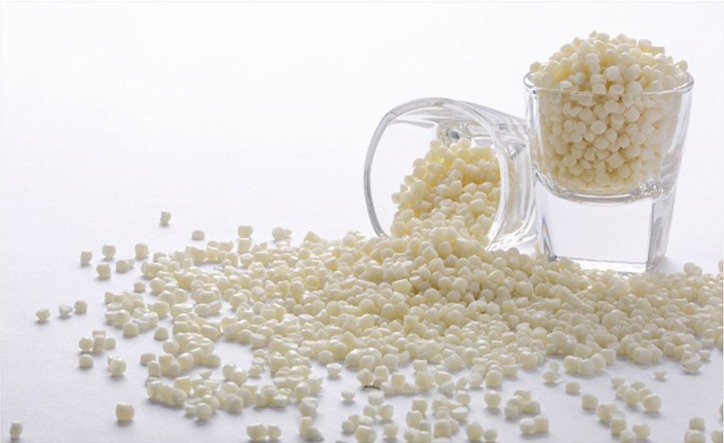
Insert molding is a subset of injection molding that is becoming increasingly popular due to its high durability, reliability, and economy. With insert molding, you can seamlessly integrate metal into plastic, producing a strong metal-to-plastic component.
This article will explain insert molding design tips as well as a hands-on guide to common insert molding problems and solutions and best practices, providing you with valuable insights into this manufacturing technology.
Insert molding is an injection molding process that involves placing a prefabricated insert component (usually metal) in a mold during a molding cycle and then encapsulating the insert with plastic to produce a strong combination of metal and plastic. By combining dissimilar substances, insert molding enables the creation of hybrid components with enhanced aesthetics, functional properties and reduced costs compared to multi-material production methods. It finds wide application in automotive, consumer electronics and industrial equipment industries.
Key features of insert molding include:
Inserts are used to connect and position plastic parts with other components, or to achieve electrical conductivity, adsorption, or connection. Different materials are available depending on the application. Here is a list of the most common insert materials:
Insert molded parts are relatively precise, so they require high-end injection molding machines to ensure the accuracy of the parts. Any small error in injection molding may cause the failure of such products or damage to the mold. Because vertical injection molding machines are convenient for placing inserts, vertical injection molding machines are usually used for production to increase speed and efficiency.
Manually or automatically position the insert precisely in the cavity using locating pins, slots or clamps.
With the molding parameters correctly set, molten plastic is injected into the mold cavity to encapsulate the carefully positioned insert and waits to cool and solidify.
After the plastic has fully cooled and solidified, open the mold and remove the plastic part. This can be done manually or with an automated robotic arm, where the plastic and metal inserts are combined into a solid combination.
Separate the plastic parts or components from the runners according to the actual situation. Some molds use hot runners without runners, which saves costs, but will increase the cost of the mold.
Depending on the specific requirements of the product, post-processing steps may be required. This may include additional processing, quality inspections, surface treatments, etc. to ensure the part meets the required specifications. Here are some common ways manufacturers post molding insert-molded parts:
Insert Molding Design Guidelines
These are some design tips we have summarized based on our 10 years of experience in insert injection molding. We hope to help you better design insert molded plastic parts.
Sharp interior corners act as stress risers where cracks can more easily propagate. This weakens the joint between the insert and molded material. Sharp corners are difficult areas for the flowing molding material to completely encapsulate, potentially leaving voids. This reduces bonding effectiveness. Rounded corners help the material flow through easily, and rounded corners or smooth transitions reduce stress while also reducing the difference in shrinkage of the material as it cools.
Design vents in mold to remove air and facilitate complete encapsulation of insert during mold fill.
As the injected resin shrinks and cools, the plastic and metal parts can easily separate and be destroyed. This is mainly caused by hoop stress and solutions should be planned in advance.
Proper draft facilitates uniform filling while allowing robust, high-quality parts to readily pop out after molding for best productivity and lowest rejects. .Typically provides 1-3 degrees of draft on all vertical surfaces, However, depending on the roughness of the surface texture, consider using a draft angle of 5 degrees or more per side.
Due to gravity, vertical injection molding makes it easier to load and place inserts without moving the position, which ensures the accuracy and reliability of insert placement. If the order volume is larger, consider investing in a robot or automated system to load the inserts into the mold.
Proper bonding is critical to part strength. Metal and plastic usually cannot be bonded. In order to ensure bonding, mechanical bonding such as holes, grooves, etc. is usually used, or an adhesive coating is used to enhance the bond between the metal and plastics.
All sharp corners and edges on the insert should be gently rounded with small radii or filleted to reduce concentrations of molding stresses. A radius of 0.5-2mm is generally suitable.
A boss is a prominent feature on a molded plastic part, often used to join two parts, fit a shaft hole, or assemble with self-tapping screws. When designing the boss, its diameter should be considered to ensure adequate strength and durability. Typically, the boss diameter should be 1.5 times the insert’s diameter.
When designing inserts in insert molding, the main consideration is the strength of the package, that is, the encapsulated inserts can’t be easily separated from the plastic. Add locator pins, grooves or holes into the insert design so it can be accurately positioned and held securely in place within the mold cavity prior to injection
Maintaining uniform wall thickness of plastic parts is crucial to the appearance and function of plastic parts. Uneven wall thickness will lead to defects such as size, appearance, deformation, etc. that are difficult to control. Insert-molded inserts increase internal stress, and the uniform wall thickness makes internal stress uniform and less prone to cracking and other phenomena.
Cracks in the plastic around the metal insert are one of the most common defects in insert molding. This is caused by molding hoop stress. Choosing the right materials is critical to solving this shortcoming. Correct workmanship should also be maintained.
Carefully select materials for the insert and molded plastic that will be chemically compatible and not prone to corrosion, cracking or delamination over time.
Carry out test molds and process trials to verify the insert design provides a strong bond with the plastic without defects after molding. Make refinements as needed.
Although most injection molding is done using horizontal presses, vertical molding machines are ideal for insert molding and overmolding. In a vertical injection molding machine, the mold is mounted vertically, and the mold opens and closes on the y-axis, using gravity to hold the insert in the mold. Once placed, no deflection occurs, which greatly increases success. The probability.
Insert injection molding can also be done on a horizontal injection machine, but may increase the cost of the insert mold and operating costs. For insert molding of large plastic parts, horizontal injection molding machines are still the ideal choice. Conventional vertical molding machines have relatively small tonnage and can’t meet demand.
The choice of insert material determines the intended application and expected performance of the product to a large extent. The appropriate and unique plastic material should be selected for your application based on the product’s intended use, use environment, and adhesive properties. These are some of the major materials used for insert molding. The selected plastic depends on the required properties, processing considerations, and economics of the application.
ABS is a low-cost material that is easy to process. It has good impact strength and toughness. ABS is widely used for internal components and housings in electronics and appliances.
PC has high clarity and scratch resistance. It gives smooth and shiny surfaces. These properties make it suitable for optical applications like lenses and displays. PC products have better aesthetics but higher costs than ABS.
POM possesses exceptional toughness, low friction, and wear resistance. It retains these properties over a wide temperature range. Automotive and industrial components operating under heavy loads often use POM.
Nylon have good mechanical properties and chemical resistance at a low cost. They are easy to process and commonly used for internal parts, gears, and handles. The versatile properties of nylons make them a preferred engineering plastic.
PBT has excellent heat resistance and can operate continuously at 150°C. It is used for demanding applications requiring durability at high temperatures, such as electrical components.
PPS offers outstanding resistance to heat, chemicals, and wear & tear. It is suitable for parts working under extreme conditions at temperatures up to 230°C. PPS is increasingly used in automotive and aerospace components.
Insert molding process delivers lower per-unit production costs, higher design versatility, improved quality and reliability for modern injection molded applications. With advanced techniques, it remains a very competitive manufacturing process. It has the following advantages:
Inserts allow placement of non-plastic features like metal, magnets, wood, PCB or ceramic parts where needed in complex geometries without limits of mold tooling contours. This expands part design possibilities.
Robust mechanical and chemical bonds form between materials during molding. This ensures long-term reliability of material joints, reducing wear and corrosion weak points compared to fastened assemblies.
Single molding manufacturing simplifies assembly operations and eliminates secondary joining steps like gluing or fastening to boost throughput rates and minimize labor costs.
The mechanical bond formed during molding between the insert and molded material integrates components securely and reliably. This joint can withstand stresses, chemicals and temperatures better than adhered bonds.
Robust process controls in injection molding yield highly consistent dimensional accuracy and mechanical properties batch-over-batch for inserts permanently secured within plastic casings.
Inserts such as decorative inlays, emblems or nameplates blend seamlessly into the plastic substrate during molding, enhancing the finished product appearance in a robustly bonded design.
It may seem that insert molding is no different from conventional injection molding. In fact, insert molding is a precise injection molding process, and any small deviation may lead to project failure. Therefore, before starting the project, there are some factors that need to be considered:
The order quantity directly determines whether to load the inserts manually or automatically. If the order volume is large, the investment in automatic loading can be cost-effective as production quantities increase.
Every project has a budget. The budget includes the initial mold investment and the unit price of the product. If the production quantity is small, you can consider manually placing the inserts with fewer mold cavities. If the expected quantity is large, the investment return ratio can be calculated based on the order quantity.
The type of insert is the first factor to consider before insert molding. No matter what material the insert is made of, it should be able to withstand the high temperatures and pressures used during the molding process. Insert size, tolerances. Materials will all have an impact on costs. Some will also have a significant impact on the process, such as magnet insert molding. Magnets are fragile, and the high temperature during molding will demagnetize them. Therefore, some magnet insert molding must be magnetized after molding. It is also difficult to achieve tight tolerances on magnets, which can easily cause flash during molding. All of these details are carefully considered before the project begins.
The main costs of insert molding include: mold cost, insert material cost, plastic material cost, automation equipment cost, and operating cost. All of these costs will ultimately be reflected in the unit price of the product.
The positioning and fixation of inserts in the mold are very important. How to fix the insert and how adhesive it is. It is best to add grooves, holes, and other undercut structures on the insert to increase adhesion. You can also apply adhesive. The amount of plastic used to secure the insert must also be considered, too little and the plastic can easily fall off.
Insert tolerances and mold tolerances play a key role in the stable operation of the project. Excessive tolerances can easily cause flash and even damage the mold.
Insert molding materials and molding processes are also very important. Comprehensive considerations must be taken, including cost, use environment, firmness, tolerance, internal stress, sealing, etc.
Insert molding molds must be carefully designed, and inserts must be easily placed and fixed to avoid molding defects. Therefore, using the correct injection mold plays a key role in the success of the entire project.
In insert molding, mold design is a key link in manufacturing. Insert molding mold design requires comprehensive consideration of multiple factors, including insert positioning, fixation, mold structure, exhaust system, heating and cooling system, mold material, and safety protection measures. wait. Only by designing a reasonable mold can we produce high-quality embedded plastic products. The following are the key points of insert mold design that we often refer to:
Consider the structure of the insert itself to ensure precise positioning of the insert in the mold without affecting the overall performance to ensure the quality and dimensional accuracy of the product. The shape, size and location of the positioning holes of the insert, as well as its cooperation with other parts of the mold, should be considered during design.
When designing the mold, the local temperature distribution around the insert should be calculated to avoid uneven heat insulation or thermal stress concentration.
The surface roughness of the insert affects the strength of the bond between the plastic and the insert. Often, the surface of the insert needs to be polished or coated to improve bonding with the plastic.
A fixed insert device should be designed in the insert mold to prevent it from moving or falling off during the molding process, and it should be easy to operate. Appropriate fixing methods, such as springs, buckles, etc., should be considered during design to ensure the stability and reliability of the insert during long-term mold operation.
Add a special heat conduction channel according to the insert material to promote uniform cooling without temperature difference. You can choose mold steel with good thermal conductivity to enhance heat conduction capabilities.
The mold needs to design an effective cooling system to ensure that the plastic is cooled evenly in the mold and avoid internal stress caused by temperature differences.
The mold structure should be reasonable and easy to operate and maintain. Molds for manual placement of inserts should be designed to facilitate placement of inserts. When designing insert molds, the opening and closing, ejection, cooling and other actions of the mold, as well as the strength and stiffness requirements of the mold, should be considered.
Mold plastic parts are made of different materials, and a reasonable exhaust system needs to be designed to prevent gas from being retained in the product to form bubbles or trapped air that affects the quality of the product.
According to the insert material and molding process requirements, a reasonable heating and cooling system is designed to ensure the molding quality and efficiency of the product.
Select the appropriate mold material to meet your insert molding requirements. Mold materials should have good wear resistance, corrosion resistance and high temperature performance. The pop-up surface of the insert is made of wear-resistant material to avoid loss of the insert surface. Quenched steel is most suitable for mass production. Commonly used quenched steels include S136, M316, and HRC50-5, which can ensure the stability and efficiency of mass production.
Safety factors should be considered during the design process, such as preventing workers from operating errors and avoiding mechanical failures. Corresponding safety protection measures can be taken, such as safety doors, limit switches, etc.
Common problems in insert molding need to be comprehensively considered and solved from multiple aspects such as mold design, operating procedures, molding processes, plastic raw materials, and mold steel material selection. Through reasonable prevention and solution measures, the quality and efficiency of insert molding can be effectively improved. We have listed some common insert molding issues to better help you solve your insert molding plastic product problems.
Reason: No adhesive is applied and no mechanical bonding structure is used.
Solution: Apply adhesive to the insert to increase adhesion. Add mechanical structures to the insert, such as holes, grooves, etc.
Reason: Warping is mainly caused by uneven shrinkage
Solution: Make the mold surface temperature uniform by increasing the cooling time and adding cooling channels.
Reason:
Solution:
Reason:
Solution:
Reason: The insert tolerance is too large. The molding parameters are unreasonable, the pressure and speed are too high.
Solution: Use tighter tolerances when making inserts. On the premise that the product can be made perfectly, it can be formed with less pressure and speed. Adjust the speed and pressure of opening and closing the mold during molding to minimize damage to the insert from external forces.
Reason: Flash is one of the most common defects in insert-molded plastic parts. The main reason is generally that the tolerance of the insert is too large. A small number of reasons may be mold problems, process problems such as insufficient mold manufacturing accuracy, too much molding pressure, etc.
Solution: Strengthen the control of insert tolerances and try to avoid flash due to too large insert tolerances. If it is a mold problem, repair the mold and adjust the molding process.
Reason: The wall thickness of the part is uneven and some areas are too thick. The ribs are too thick
Solution: Reduce shrinkage by adjusting the molding process, such as increasing pressure, increasing cooling time, etc. If it still can’t be solved, we have to modify the wall thickness of the part or reduce the thickness of the ribs. Such issues should be paid attention to during part design.
Reason: Because the thermal expansion coefficients of the insert and plastic are different, the hoop internal stress exceeds its maximum limit.
Solution: Heat-treat inserts before molding. During molding, the molding pressure should be as small as possible and the molding temperature should be as low as possible to reduce internal stress during molding. Heat treatment the components after molding reduces internal stress concentration.Use toughened, more durable resins because these materials have better elongation and resistance to breakage.
Reason:
Solution:
Reasons:
Solution:
Reasons:
Solution:
Products manufactured through insert molding have higher mechanical strength and service life. The material interface is firmly bonded and is not prone to quality problems such as peeling. It is widely used in electronics, automobiles, household appliances and other industries. Here are some common applications of insert molding and example products:
Common in interior and exterior automotive parts. Electric window switches, door handles, rearview mirrors, ignition keys inserted into thermoplastics.
Heating elements and control interfaces inserted for dryers, washing machines, ovens, water heaters. Thermostats, dials, displays integrated cleanly.
Valves, fittings inserted for flame detectors, flow meters, hydraulic cylinders. Metal parts protected while enabling component assembly.
Electrodes, cannulas molded for defibrillators, blood pressure monitors. Lens assemblies, sensors inserted for MRI machines, ultrasound wands, lab equipment, medical equipment accessories.
Used in consumer electronics like smartphones, tablets, remote controls. Metal inserts for antennas, connectors, switches molded into plastic housings.
Tags molded for luggage, inserts for keyboards, buttons for remote controls. Metal-plastic integration enables resistant casings.
Outdoor furniture handles, locks inserted for durability in plastic casings. Storage containers with metal ribbing, hinges.
Insert molding is often used to create lightweight, durable and precise aircraft parts, helping to improve fuel efficiency and safety standards.
There are some challenges when using insert molding. Manufacturing review designs must therefore be carefully weighed, and attention must be paid to a number of factors that may directly or indirectly affect the efficiency and success of the entire process.
The material directly affects the quality of the final product. Compatibility and durability between the insert material (usually metal) and the plastic material must be considered to prevent warping, cracking, sinking and other molding defects.
Placement and positioning of inserts should be carefully designed to accommodate the insert and prevent any movement during the molding process. It should also allow for easy and safe placement of inserts, while tolerances in this area should be controlled to ensure reliable and accurate placement of inserts.
For insert molding, mold damage is inevitable, whether it is manual or automated loading. Improper manual placement, out-of-tolerance inserts, and mold problems can all damage the mold, especially the area where metal inserts are placed. In order to save the time of repairing the mold as much as possible, replaceable mold inserts are made in the mold area where the insert is placed. Once the mold is damaged, the replaceable mold insert in this area is immediately replaced, saving time and increasing efficiency.
The process parameters during injection molding play a key role in the success of the project. Avoid stress warpage, cracking, shrinkage and other problems caused by excessive pressure and temperature.
If the temperature of the plastic is too high, it may increase the risk of stress cracking or even damage the insert, while if the pressure and temperature are too low, it may result in short shot.
Regular inspection of molds for wear and damage, replacement of worn parts, first article inspection during production, and inspections are all key preventive measures to ensure consistent product quality.
Whenever possible, use automated systems to load and place inserts into the mold. This not only improves production efficiency and reduces labor costs, but also ensures part quality consistency and production reliability.
Insert molding and overmolding are both injection molding processes. They look very similar, but they are two different molding processes. Let’s compare them:
Insert molding is a single injection molding that can be completed in one step. It involves placing a prefabricated insert into a mold and then injecting molten plastic to encapsulate the insert. The main purpose is to create a single integrated part (metal + plastic) that increases strength, reduces assembly and improves functionality.
Overmolding involves molding a layer of plastic over an existing plastic part (substrate). It requires two or multi- steps to complete and is a double-injection or multi-injection molding technology. And it is usually molding from two different materials, but of course it can also be molding from two same materials. Our common power tool handles are mainly used to improve grip, enhance aesthetics and ergonomics.
In conclusion, Insert injection molding is an efficient manufacturing process that allows for the precise integration of different materials into a unitary structure through injection molding. Insert molding eliminates the complexity of multiple assembly, reduces costs, and increases durability, stability.
Material selection, mold design, automation and molding process control are key factors in the success of insert molding. By tightly controlling these key variables and following insert molding design guidelines, manufacturers can avoid many potential problems and increase their probability of success.
For over 20 years, Attractive Plastics has been a one-stop supplier for China insert injection molding manufacturer. We have applied this technology across many industries, providing viable customized insert molding solutions for them.
If you are interested in exploring any issues with insert injection molding or overmolding. Our team of experts are ready to help with any questions you may have. Contact us and we can help you realize your project.