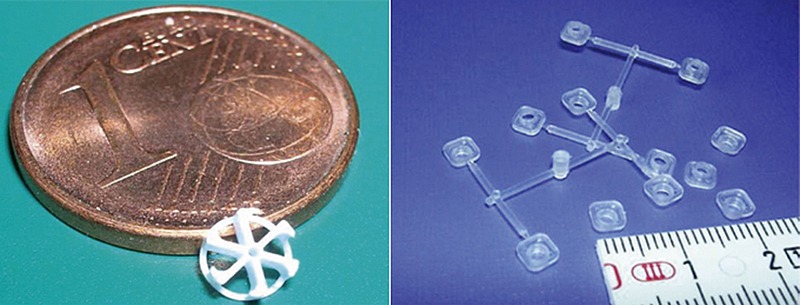
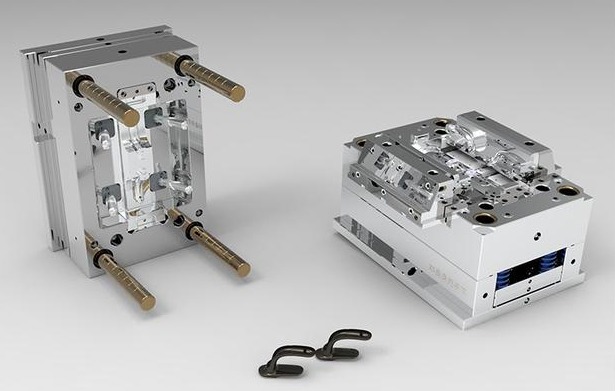
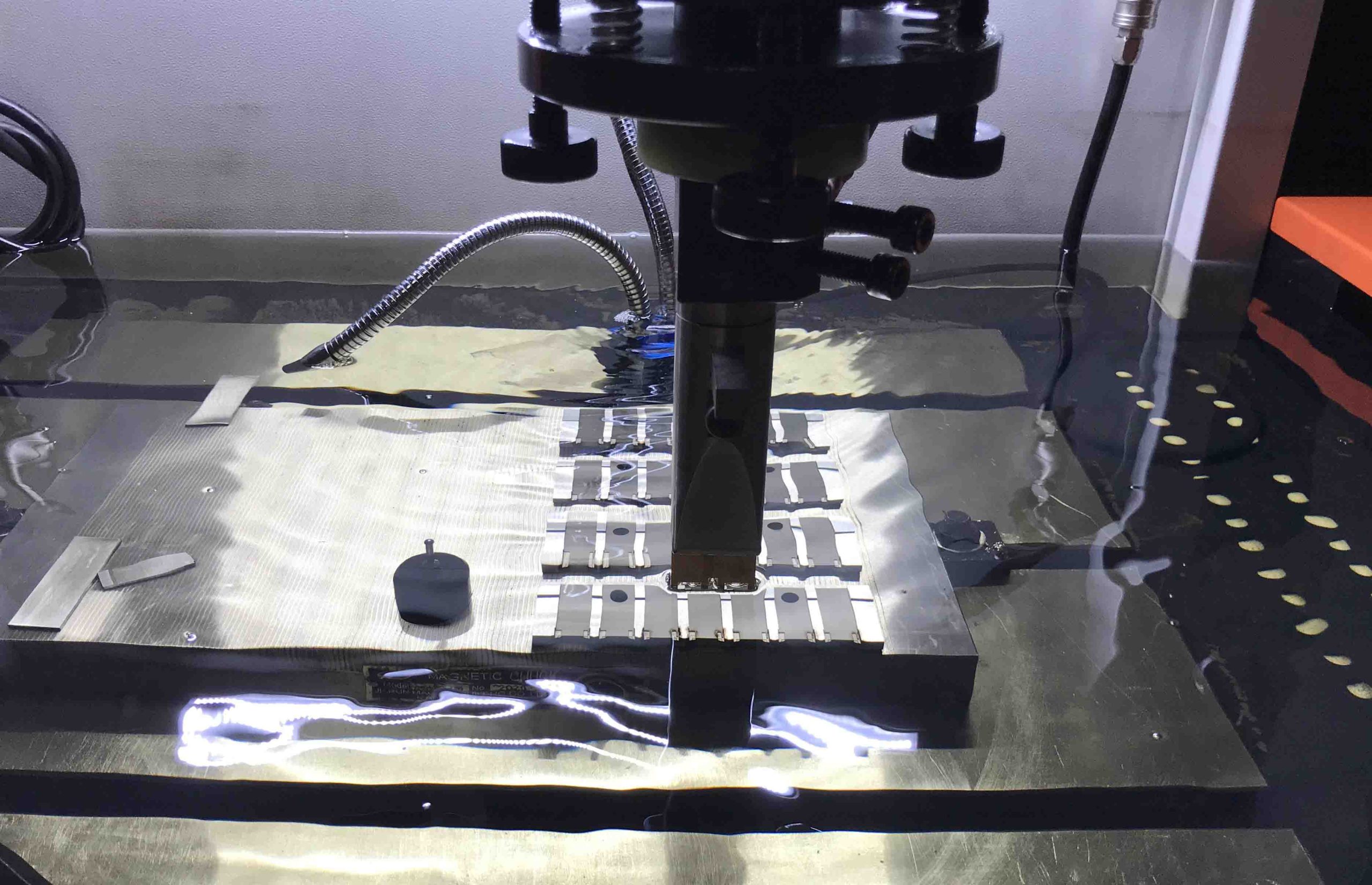
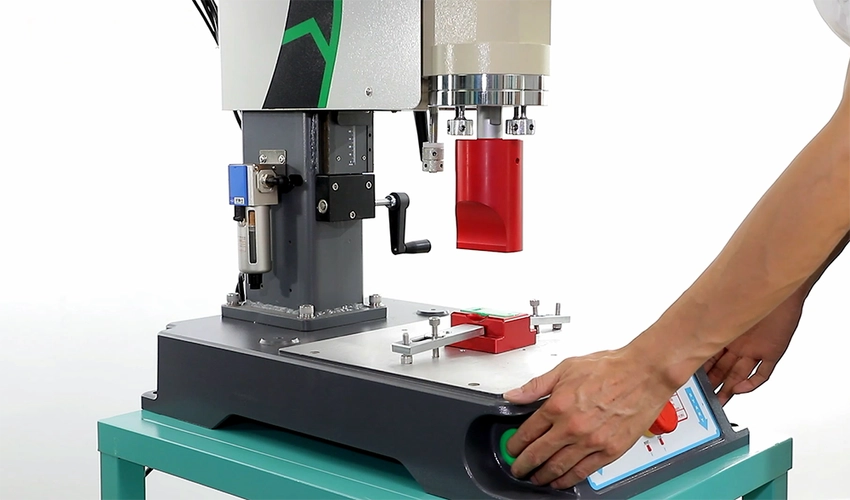
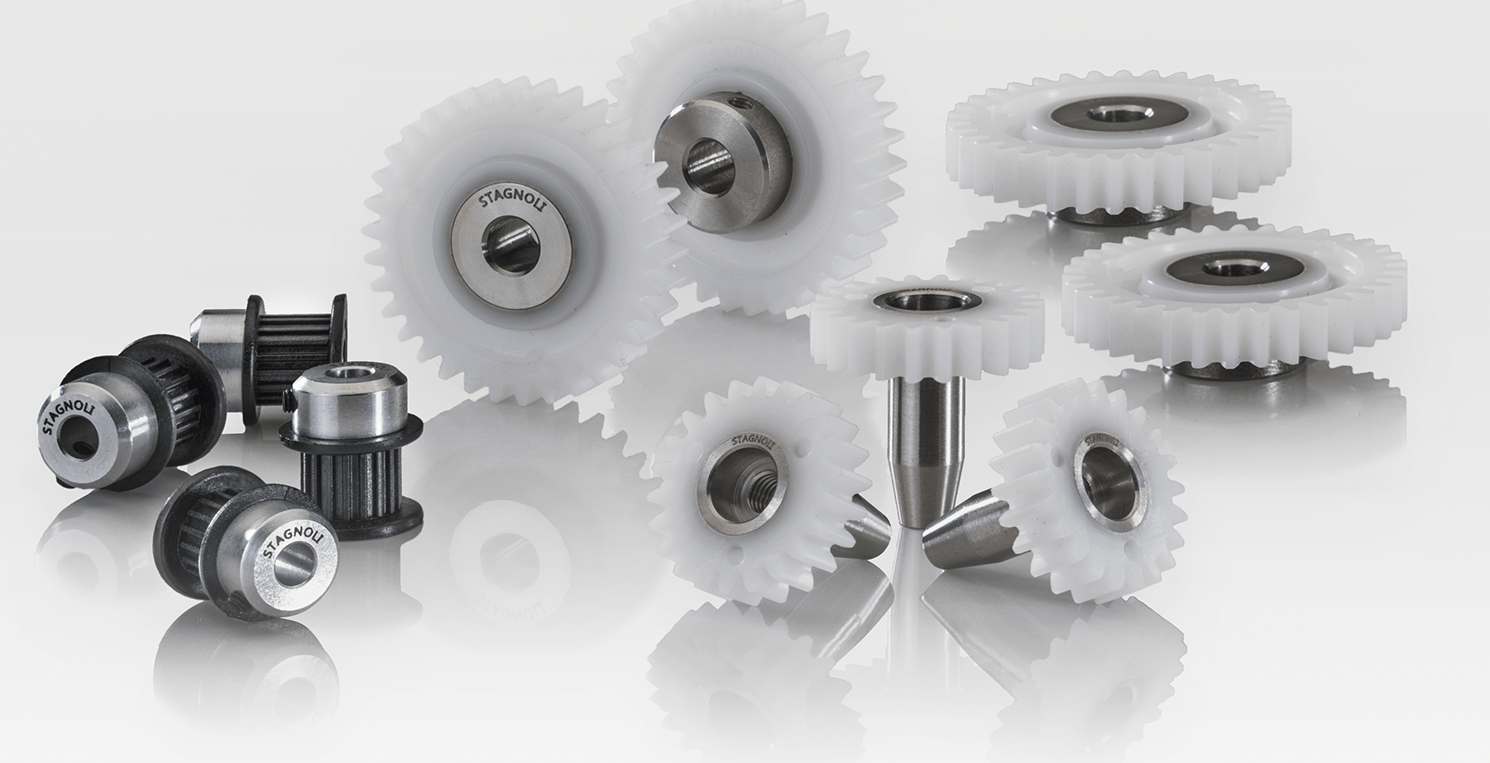
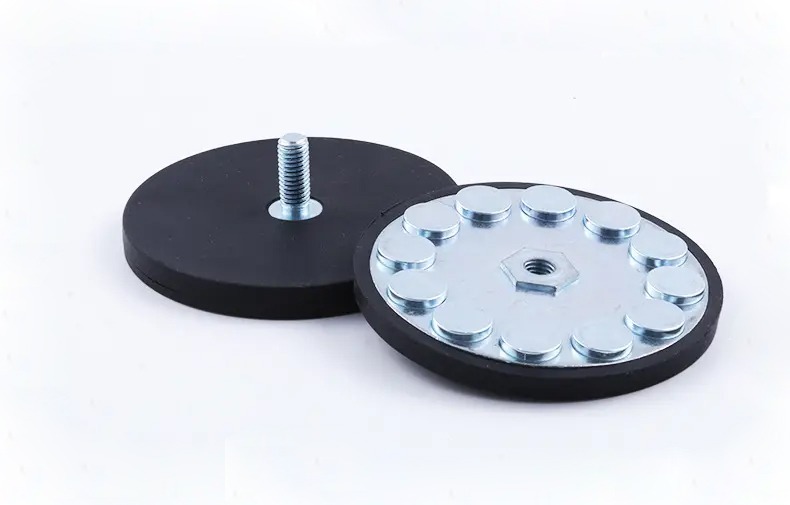
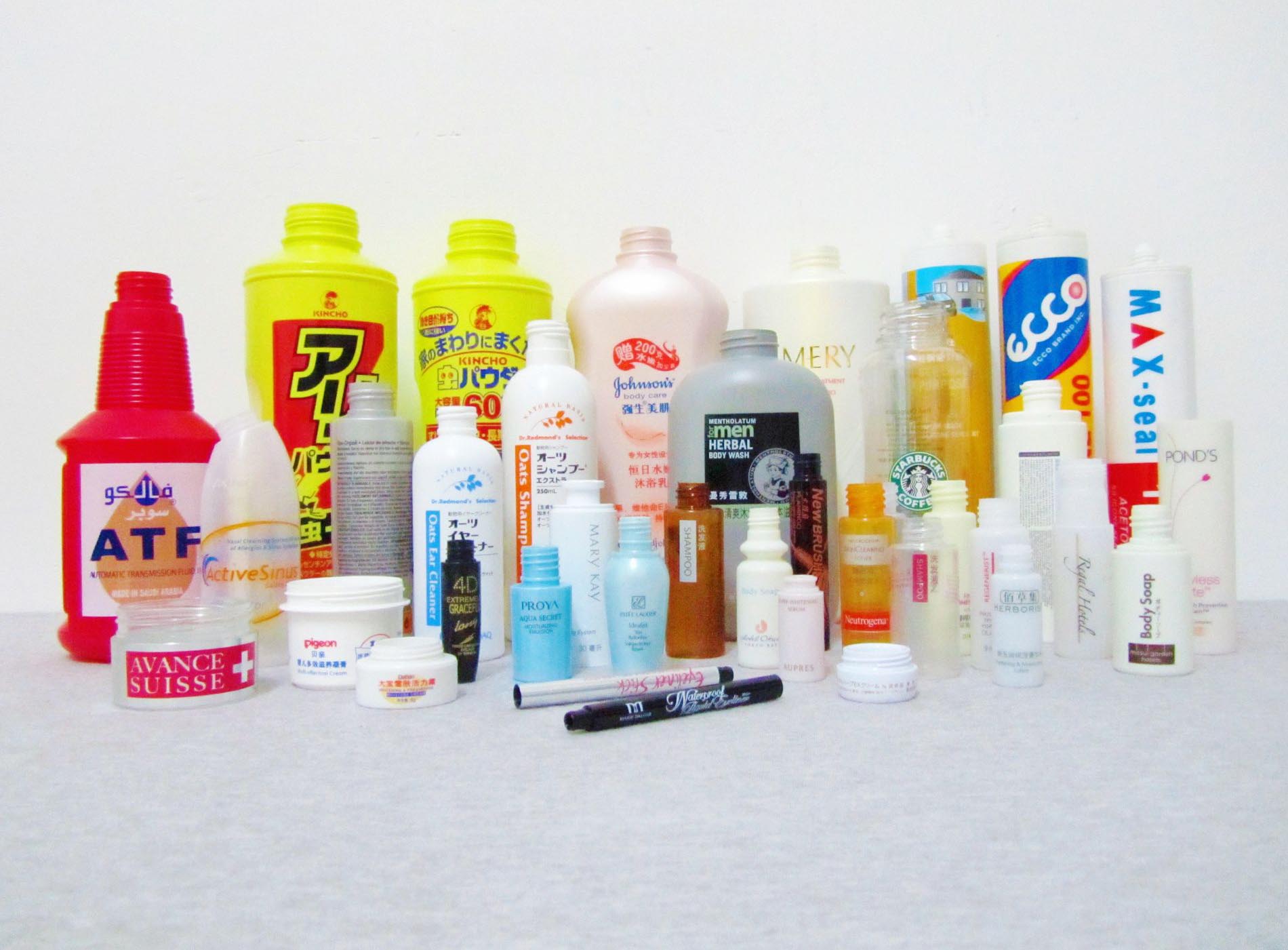
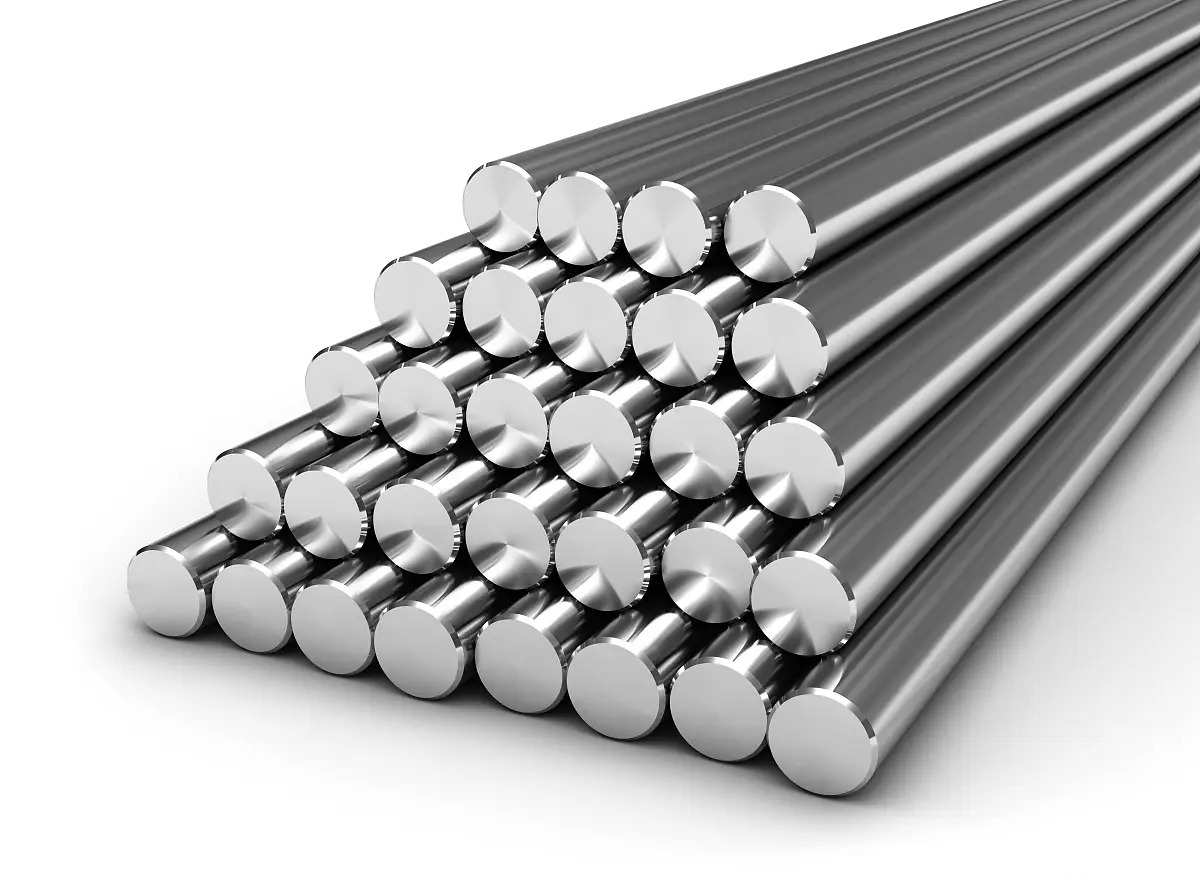
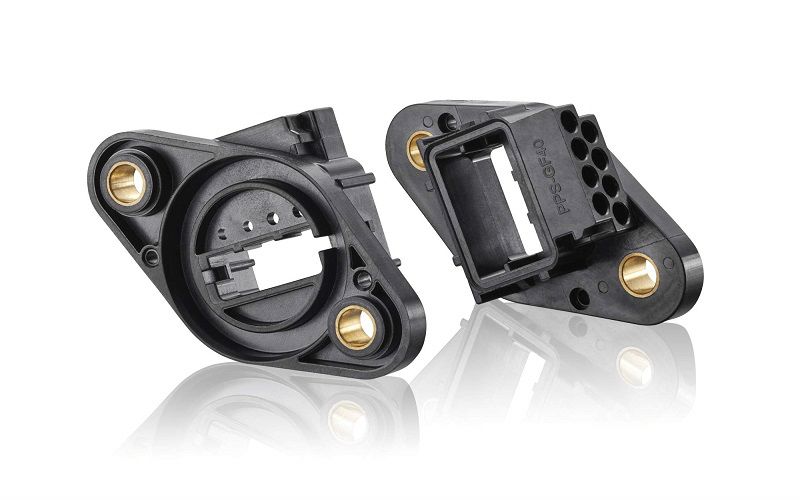
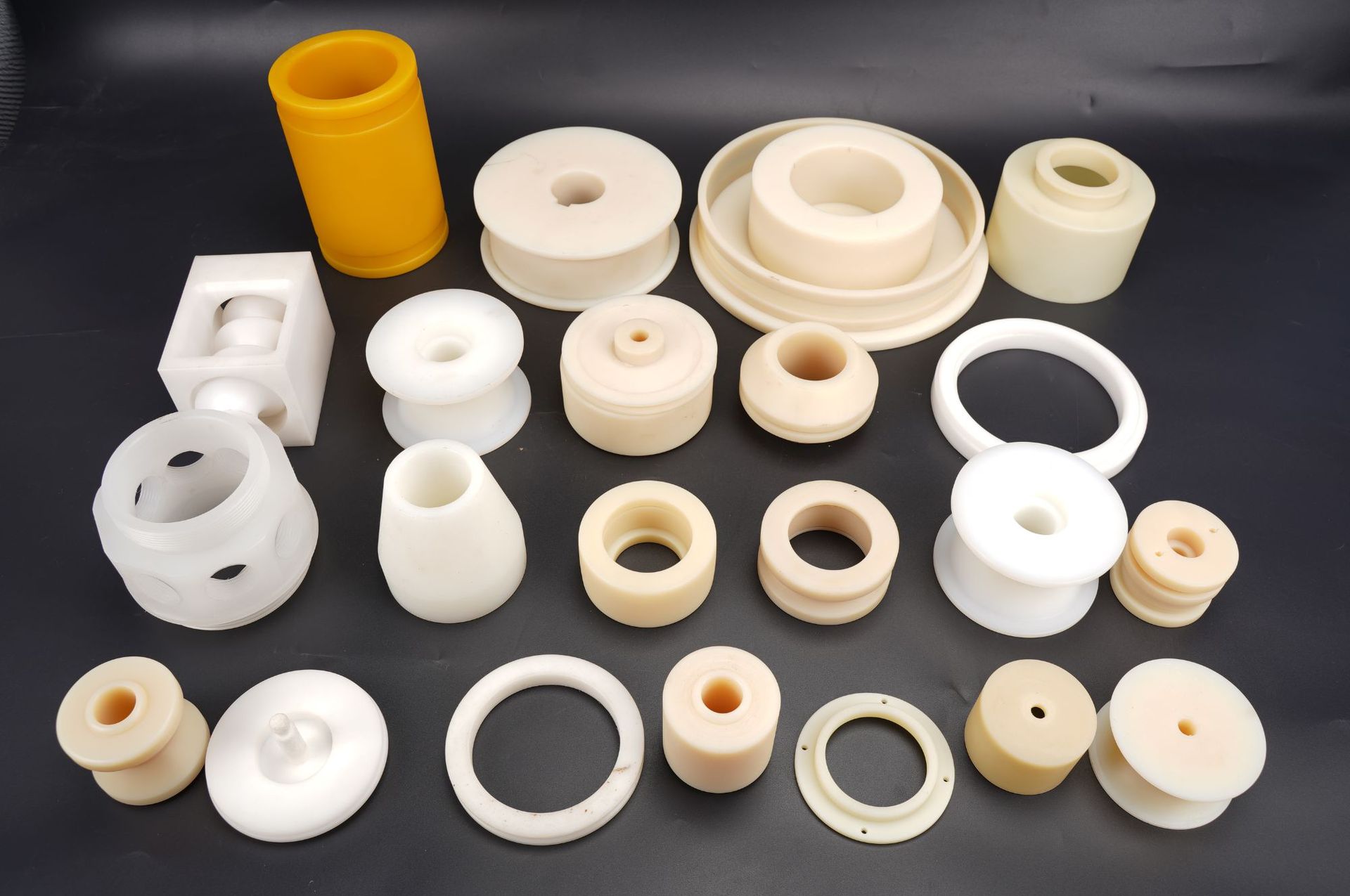
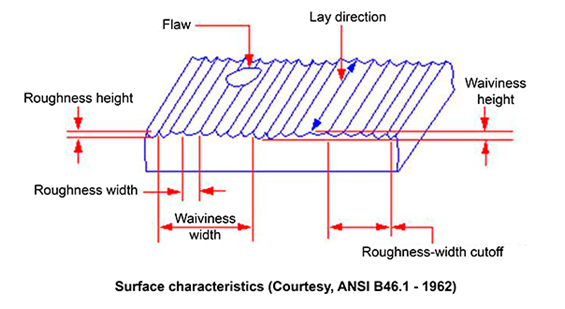
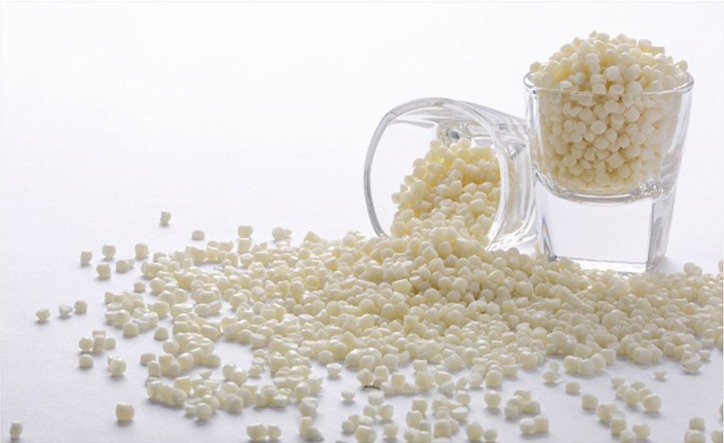
In the field of injection molding manufacturing, injection molding is a key process. Its quality directly affects the quality of plastic parts, as well as delivery time and price. It is at the heart of plastic component production and manufacturing.
In this article, we’ll deep dive into the fundamentals of injection molds, their composition, types, mold design considerations, advantages and disadvantages, as well as how they are manufactured. The aim is to help you gain a better understanding of injection molds.
Injection mold, also known as injection mold tooling or injection tooling, refer to tools designed and manufactured for the production of plastic products on injection molding machines. These precision tools play a critical role in shaping plastic or polymer materials into finished parts and components.
Injection mold tools are typically made from hardened tool steels or aluminum alloys, depending on production needs. Steel molds allow for higher part volumes due to their durability, while aluminum molds are better suited for lower volume runs due to their lower material cost and faster lead times.
The tooling process involves designing and engineering the cavity details that will impart the desired geometry on the molded part. Advanced computer-aided manufacturing techniques such as CNC machining or EDM are then used to precisely cut the mold shapes and features to the required tolerances.
In addition to the mold cavities themselves, injection molds also contain important components like cores, slides, lifters, ejectors and cooling channels. These internal elements are carefully positioned and customized based on the part design specifications.
Once the mold is manufactured, the molds undergo thorough testing and small batches to ensure dimensional accuracy and longevity for hundreds of thousands or even millions of injection cycles. When properly engineered, injection mold tools allow manufacturers to mass produce plastic components with unparalleled repeatability, quality and economies of scale.
It is very helpful to understand some basic characteristics and components of injection molds to better optimize mold structure and design. Essential parts of injection mold tooling are:
Also known as the A-side or stationary half, this is the non-moving side of the tool which is typically mounted to the injection molding machine to receive the injection of molten plastic material. It forms the shape of the part’s outer surface or cavity.
Also called the B-side or moving half, this is the tool portion connected to the opening side of the molding machine. It can open and close relative to the stationary cavity half. The B-side opens when the part has cooled and is ready to be ejected from the tool. It forms the shape of the part’s inner surface or core.
Mold inserts, also known as inlays or cores, are an important component of injection molds. They are usually embedded into the main structure of the molds to form or shape specific parts or features of plastic parts. These parts may be complex geometric shapes, threads, holes or other features that are difficult to machine directly on the mold main body.
The functions of mold inserts are:
Simplify mold machining: For complex or delicate geometric shapes, direct machining on the mold main body may be very difficult or costly. By using mold inserts, these complex parts can be manufactured separately and then embedded into the molds, simplifying the machining process of the mold main body.
Facilitate maintenance and replacement: During mold use, some parts may need repair or replacement due to wear or damage. If these parts are made as inserts, only the inserts need to be replaced or repaired without the need for the entire mold to be repaired, greatly reducing maintenance costs and downtime.
Prolong mold life: By using mold inserts, the mold main body can be protected from direct wear and impact, thus extending the service life of molds.
The common types of mold inserts classified by different uses are:
The lifter, also known as the top pin or top rod, is an important component of an injection mold. Its main function is to push the molded plastic product out of the cavity during mold opening so that the product can be removed. The design, manufacturing and installation precision of the lifter directly affect the demolding effect of the product and the service life of the mold. Lifters come in various types, commonly including vertical top, inclined top, and screw pin types. Different types of lifters are suitable for different product structures and mold designs. The material of the lifter should have sufficient strength and wear resistance to withstand high-frequency use in the injection molding process.
The slider, also known as the side slider or inclined slider, is the mechanism for realizing side core movement in the mold. It is commonly used for plastic products formed with side holes, side recesses and other structures. During mold opening, the slider removes the plastic material molded in the side hole or recess through side movement so that the product can be removed.
By using sliders, more complex structures and shapes can be realized in the mold, expanding the design space of plastic products. To prevent the slider from moving or falling off during injection molding, a reliable locking mechanism needs to be designed to ensure the stability of the slider in the closed mold state. The slider is easy to wear due to frequent movement, so a material with good wear resistance should be selected and worn parts need to be checked and replaced regularly.
An internal channel network formed within the cavity half to circulate a cooling medium and control the cooling characteristics of the plastic once injected into the tool. These channels help control the cooling process of the plastic part, ensuring uniform cooling and preventing deformations.
The moving parts (usually pins) located on the B-side of the tool that push forward after the mold opens to strip the cooled part from the tool for removal. The ejector system helps to eject the molded part from the mold cavity.
Runner system have two types:
Gate is the point where molten plastic enters the cavity from the runners/sprue. Its design impacts filling, weld lines, stresses. Size, number and placement of gates depend on part geometry, flow balance calculations and material requirements. Common gate types include edge, side, bottom, sub-gating, etc. Each suitable for different part/material/process needs.
Side actions are used in injection molding to create features such as threads, hinges, and snap-fit connections that require movement in the mold to be formed. Side actions are typically achieved using sliding cores or lifters that can move in and out of the mold cavity to create the undercut feature.
Side actions can be complex and require careful design and engineering to ensure proper operation and alignment. They also require additional mechanisms such as springs, cylinders, and guides, which can add to the cost and complexity of the mold. However, side actions are essential for creating many common injection molded parts with complex geometries and features.
Injection mold design is a complex engineering endeavor that involves consideration and balancing of numerous factors. A holistic approach needs to be taken when designing, comprehensively considering product requirements, process conditions, mold material selection, manufacturability, and maintainability. Through meticulous design and optimization, the tooling performance, production efficiency and ability to meet customer needs can be ensured. There are several critical design considerations for injection mold tooling
The part design dictates many aspects of the tool design like number of cavities, size/shape of the runners/gates, need for side actions/cores, etc. Designing for manufacturability from the start is key. The part’s geometry, dimensions, and features must be carefully analyzed to determine the appropriate mold configuration, gate locations, and ejection system.
The mold material used to construct the mold must be selected based on the part’s requirements, the number of parts to be produced, and the molding process parameters. Common mold materials include steel, aluminum.
The mold construction method, such as single-cavity or multi-cavity, and the mold’s parting line location, affect the mold’s complexity, cost, and production efficiency.
A proper cooling system is essential to ensure uniform cooling of the plastic during the molding process, which helps prevent warpage,, and other defects. The cooling system design should consider the mold’s geometry, the material’s thermal properties, and the molding cycle time.
The ejection system is used to remove the molded part from the mold. The ejection system design should consider the part’s geometry, the mold’s configuration, and the molding process parameters to ensure efficient and reliable ejection.
The gate location and type affect the plastic flow into the mold cavity, the part’s cosmetic appearance, and the mold’s manufacturability. The gate location and type should be selected based on the part’s geometry and the molding process parameters.
A proper mold venting system is essential to ensure that the air can be exhausted during the molding process, which helps prevent air entrapment, voids, and other defects. The mold venting system design should consider the mold’s geometry, the material’s flow characteristics, and the molding cycle time.
The mold’s machining and assembly processes should be carefully planned to ensure that the mold meets the required tolerances and surface finishes. The mold’s assembly process should also be designed to ensure that the mold can be assembled and disassembled easily for maintenance and repair.
The cost of the tooling is a significant factor in the injection molding process. The tooling design should balance the cost and performance to ensure that the tooling is cost-effective and meets the required production requirements.
Mold flow analysis is a very effective tool for optimizing injection mold design. Mold flow simulation software can be used to model the flow of plastic within the mold cavities, determine ideal locations for gates, parting lines and ejector pins. It also helps identify potential issues such as weld lines, trapped air voids and non-uniform filling. Analyzing the mold’s cooling system helps ensure even thermal distribution in the plastic, which helps prevent warpage and shrinkage defects.
Single-cavity mold with only one cavity, which can produce only one part per injection. This type of mold is typically used for small-scale production or prototyping because of its relatively low cost and ease of manufacturing and maintenance.
Multi-cavity mold with multiple cavities, which can produce multiple parts simultaneously per injection, reducing unit costs for medium to high volume production. This type of mold is typically used for large-scale production to increase production efficiency and reduce unit cost. The manufacturing and maintenance cost of a multi-cavity mold is relatively high due to its more complex design and processing.
Insert mold is incorporates inserts (such as nuts, bolts, magnets etc.) into plastic parts. This type of mold is typically used for producing parts that require assembly. The advantage of an insert mold is that it can improve the strength and assembly performance of the parts.
Insert molding is widely used in products that require metal inserts to be encapsulated in plastic. Such as automotive parts, electronic and electrical components and medical equipment. While saving costs, its good bonding reliability is a key factor.
Enables molding different materials together by injection molding onto a preformed component produce parts with complex geometries or requiring different material properties. This type of mold is typically used for producing parts with complex geometries or requiring different material characteristics, such as autmotive parts or medical devices. The advantage of an overmolding mold is that it can improve the performance and aesthetics of the parts.
Stack mold that stacks multiple molds together to increase production efficiency and reduce cost. This type of mold is typically used for producing large quantities of identical parts, such as plastic bottles lid. The advantage of a stack mold is that it can increase production efficiency and reduce unit cost.
Family mold that combines multiple different parts into one mold to reduce mold and cost. This type of mold is typically used for producing a series of similar parts, such as different sizes or shapes of parts. The advantage of a family mold is that it can reduce mold costs and inventory costs while improving production efficiency. While they further reduce costs vs single/multi-cavity molds, material flow imbalances between distant cavities can cause challenges requiring expertise to optimize.
Utilize a collapsible core to assist part ejection for designs with undercuts or intricate interior geometries. Such as automotive parts or medical devices. The advantage of a collapsible core mold is that it can improve the accuracy and surface quality of the parts.
A double injection molds that can injection two different materials simultaneously to produce parts with two different colors or material properties. This type of mold is typically used for producing parts that require different colors or material characteristics, such as power tools handle or toothbrush handles. The advantage of a double injection mold is that it can improve the aesthetics and performance of the parts.
The unscrewing mold with a mechanism for unscrewing the molded part from the mold, typically used for producing parts with threads or screw connections. This type of mold is commonly used in the production of bottles, caps, and other threaded components. The advantage of an unscrewing mold is that it allows for easy and efficient removal of the molded part without damaging the threads or screw connections.
Three plate injection mold tooling that consists of three plates: the fixed plate, moving plate, and ejector plate. This type of mold is typically used for producing parts with complex geometries or that require multiple injection points. The advantage of a three-plate injection mold is that it allows for more flexibility in the design of the molded part and can reduce the risk of warpage or other injection defects.
The bump offs mold that incorporates a bump-off mechanism for ejecting the molded part from the mold. This type of mold is typically used for producing parts with undercuts or complex geometries that would otherwise be difficult to eject. The advantage of a bump-offs mold is that it allows for easy and efficient removal of the molded part without damaging the part or the mold. Bump off moldA typical application product for bump offs moldl is spring water bottle caps.
The hot runner mold that incorporates a hot runner system for injecting the molten plastic into the mold. This type of mold is typically used for producing high-volume parts with complex geometries or that require multiple injection points. The advantage of a hot runner injection mold is that it allows for more efficient use of plastic, reduced waste, and faster cycle times.
Mold material directly affects mold performance, durability and quality of molded parts. Injection mold materials are mainly divided into two types: aluminum and steel. Steel can withstand high temperatures and pressures, and steel molds can produce millions of plastic parts. Aluminum molds are cheaper to make but can only produce thousands of plastic parts. The actual mold material selection should be based on the requirements of the specific application. The following are important considerations for selecting the correct mold material:
These are common injection mold materials:
Aluminum is a lightweight metal with good thermal and electrical conductivity. Aluminum molds have low cost and easy machining but lower hardness and wear resistance, suitable for low precision, low volume plastic products.
P-20 Pre-Hardened Tool Steel is a low alloy pre-hardened tool steel with hardness between 28-30HRC. It has good machinability and wear resistance. P-20 steel has balanced properties at a relative low price and is widely used as a general plastic mold steel. Commonly used for non-high heat/wear resistant substrates and fixtures, cores, cavities. Good machinability makes it suitable for early design iterations.
718H is a high nickel stainless steel, pre-hardened plastic mold steel with high strength, high wear resistance and hardness between 33-37HRC. It provides excellent corrosion resistance below 800°F. 718H has good machining and polishing performance for high precision, high surface quality molds. Its corrosion and heat resistance allow molding of corrosive and high temperature plastics.
H-13 Tool Steel is a through-hardening hot work tool steel that can reach 50-55HRC hardness. It has high wear resistance, heat resistance and toughness. Especially suitable for molding of high strength, high wear resistance plastics. Used for cavities, cores and sliders of injection molds. H-13 steel has a higher price but superior performance for high requirement molds.
420 Stainless Steel is a conventional martensitic stainless containing 13% chromium, hardened to 50-55HRC. It has good machinability and wear resistance. Especially suitable for molding plastics with corrosiveness. 420 stainless has a relative low price and is an economical corrosion-resistant mold material.
Nak80 is a pre-hardened high vanadium mold steel with hardness between 37-43HRC. Nitriding hardening to 60-62HRC. Very high fatigue strength below 600°F. It has excellent machining and polishing performance for high precision molds. Nak80 also has good corrosion and heat resistance, suitable for molding corrosive and high temperature plastics.
S-7 Tool Steel is pre-hardened high carbon/chromium tool steel with high strength, high wear resistance characteristics and hardness of 50-56HRC after tempering. It has excellent wear and corrosion resistance. S-7 steel has a higher price but superior performance for high requirement, high wear and heat resistant molds, such as molds for glass fiber reinforced plastics.
S136 is a corrosion resistant, high polishing mold steel with outstanding corrosion and wear resistance. Similar to H-13 but with addition of cobalt for higher thermal conductivity to improve heat transfer. S136 is commonly used for molds requiring long contact with water or corrosive plastics like PVC. Its excellent corrosion and polishing properties keeps mold surfaces clean and precise while resisting corrosive attacks.
M316 and M340 are high strength, high wear resistant, highly corrosion resistant special mold steels. Especially suitable for molding of high strength, high surface requirement, high wear resistant plastics. M316 and M340 contain over 16% chromium which provides excellent corrosion resistance, especially for molding of fluorine and chlorine containing plastics such as PVC, PFA. These materials have higher prices but very superior performance for extremely high requirement molds (over 500,000 cycles).
MOLDMAX is a copper-based alloy with additions of beryllium and nickel. It has excellent thermal conductivity and wear resistance, making it suitable for manufacturing cooling systems in injection molds, such as sliders and ejector pins that cannot accommodate traditional cooling channels. The thermal conductivity of MOLDMAX alloy is higher than steel and aluminum, but its hardness and strength are comparable to standard tool steels. Its cooling rate is 3-4 times faster than standard mold steels like P20 or H13, effectively improving the cooling efficiency of molds and shortening the injection molding cycle time.
Beryllium copper (BeCu) is a copper alloy containing a small amount of beryllium. It possesses high strength, hardness, and good thermal conductivity along with excellent wear and corrosion resistance. It is commonly used for producing cavities, cores and sliders of injection molds requiring rapid cooling to improve production efficiency.
Tungsten carbide possesses an extremely high hardness, wear resistance and heat resistance, second only to diamond. Its high thermal and mechanical properties make it an ideal material for mold cores, ejector pins and details. Its outstanding wear and impact resistance allow molds to withstand significant friction and impacts during molding cycles. In addition, tungsten carbide also possesses good thermal and chemical stability which allows it to maintain its properties in high temperature and corrosive environments. This characteristic makes it often utilized for manufacturing high temperature molds.
Injection mold making is a complex process involving multiple steps and professional skills. From mold design to mold machining, then to trial and sampling, each step requires careful operation and professional guidance to ultimately yield a production-ready mold capable of producing high quality parts in large quantities. Here are the details of the three main steps:
There are many factors that can influence the cost of an injection molding tooling, involving the part size and geometry, mold complexity, material selection, machining methods, and more. A thorough cost estimate should comprehensively consider these aspects to ensure accuracy and effectiveness. Meanwhile, optimizing design and manufacturing processes can lower unnecessary costs and improve the value and market competitiveness of the tooling.
The complexity level of a mold design directly impacts its cost. More complex designs with more intricate details and features will require greater manufacturing difficulty and labor hours, leading to higher costs. More complex mold structures, multiple cavities, intricate cavitation surfaces, and internal inserts will increase the difficulty and expense of mold production.
Larger part dimensions or convoluted geometries mandate longer machining/EDM times, while larger parts necessitate more material and fabrication – elevating costs. Challenging shapes (undercuts, slides) potentially needing sliding mechanisms also raise pricing
Molds with higher number of cavities can produce more parts in one shot, but also increase tooling cost due to additional complexity.
Higher quality tooling often demands more time and resources to manufacture, therefore increasing costs. Such as SPI-A1 grade mirror surface finish, textures (VDI, MOLD-TECH), chromium plating, PVD, paint and PTFE coatings require higher monetary and labor capital investments, all of which impact molding tool costs.
A designer’s experience level and skills are also important factors influencing mold design costs. More experienced designers can design mold tools that fulfill requirements in a more efficient manner, lowering modification and rework costs.
Mold material selection significantly impacts costs. Price variations between materials are large, and material performance directly affects mold lifespan and product quality. Proper selection considers the product traits, production needs against budgets – processing costs differ greatly between materials. For example, hard molds are over double the machining fees of soft molds.
Tolerance precision not only relates to part dimensional stability but influences mold assembly/debugging, in turn affecting total expenditure. Higher precision manufacturing demands more sophisticated equipment/processes, elevating costs.
The mold base forms the foundation structure to support and secure tool components. Rational and intricate mold base design directly influences pricing. Standardized base can deflate production costs. Base material selection also impacts price – common materials include cast iron, 45# steel, aluminum alloys. Mold base design entails suitable type, sizing, and structuring selection. Quick change systems prove more complicated yet eventually more economical than conventional single-block tools.
Mold inserts are accessories used in injection molds to create specific features or geometries or extend mold life. The design of these mold inserts likewise significantly impacts tooling costs. Key factors influencing mold inserts costs include:
During the mold manufacturing process or after completion, if the customer needs to make design changes, it may lead to an increase in costs. Additional engineering drawing modifications and re-milling modifications will increase the final cost of the mold.
The selection of processing equipment and processes has a direct impact on mold costs. Different manufacturing processes affect costs. For example, processes such as electrical discharge machining (EDM), wire cutting, milling, grinding, etc. have different costs. Complex processing techniques will also increase manufacturing costs
Advanced processing equipment and efficient processing technology can improve the manufacturing accuracy and efficiency of molds, but they will also increase equipment purchase and maintenance costs. Therefore, when selecting processing equipment and processes, cost-effectiveness and production needs need to be considered comprehensively.
Expenses vary between regions due to labor, facility, transportation disparities. China has competitive advantage for low-cost mold making.
In addition to the direct costs mentioned above, there are also some extral costs to consider, such as trial mold fees, packaging and transportation costs, and potential taxes. Although these additional costs are not directly related to the manufacturing process of the mold, they also have an impact on the overall costs.
There are many processes involved in making a complete mold, and multiple processes using different machines are required to complete the production from iron to complex shapes. The following is a detailed explanation of the process of processing molds
High-speed CNC machining utilizes computer numeric control technology to implement rapid and high-precision milling processing of molds. In high-speed CNC machining, the computer executes a pre-programmed process using high-speed rotating cutting tools to machine the mold. This machining method has the characteristics of high machining efficiency and precision. It is suitable for rough and semi-finished machining of complex shapes such as mold cavities and cores. Through high-speed rotating cutting tools and precise cutting paths, it can quickly remove excess material and lay a good foundation for subsequent processing.
High-speed CNC can also achieve high precision machining, generally achieving accuracies of tens of microns. By increasing the tool speed and feed rate, the processing time can be greatly shortened and the processing efficiency is greatly improved.
5-axis machining centers allow the use of standard cutting tools such as end mills to efficiently cut complex mold geometries. Automatic tool changing allows rapid switching between different sized tools to optimize metal removal rates for various surfaces.
Electrode making is an important step before electrical discharge machining (EDM) and is a key component in the EDM process. Electrodes are the tools used in EDM to machine the desired shape on the mold through electric spark erosion. Their shape and size directly affect the final precision and quality of the mold.
In the electrode making process, the electrode shape is first manufactured using CNC equipment or other machining devices according to the mold design requirements. Depending on complexity, electrodes can be cut by CNC milling, numerical control wire cutting, lathe or other methods to precisely match the shapes.
The material selection for electrodes must also consider conductivity and abrasion resistance to ensure good performance. The correct electrode material should be selected according to the electrode shape, size, accuracy. Electrodes are usually made of conductive materials such as red copper or graphite. Multiple electrodes are often made to machine inner mold details or tight inner radii during EDM operations.
After completion, critical dimensions of the electrode also need to be measured and calibrated to ensure matching of the machined shapes and dimensional accuracy.
Sinker electrical discharge machining (Sinker EDM) is a method of machining molds using the principle of electric spark discharge. It is used to machine complex shapes such as deep holes, narrow ribs, micro holes and non-circular holes in molds.
In Sinker EDM, high-frequency pulse discharge occurs between the electrode and workpiece, removing excess material from the workpiece through the high-temperature effect of electric sparks to machine the desired shape. Sinker EDM has the characteristics of high machining accuracy, good surface quality and no cutting force, making it particularly suitable for precision machining and mold adjustment.
Sinker EDM is suitable for machining complex shapes (such as sharp corner, deep holes, thin ribs) and hard materials (such as hard alloys) that are difficult to machine with conventional cutting methods.
Wire electrical discharge machining (Wire EDM) uses a fine metal wire as an electrode to perform electric spark discharge cutting on molds. This process is mainly used for mold cutting and processing of mold inserts.
In Wire EDM, a fine metal wire acts as the electrode to produce high-frequency pulse discharge on the workpiece, cutting the workpiece through the high-temperature effect of electric sparks. This machining method has the characteristics of high precision, high efficiency and accuracy. It is suitable for machining materials of various hardness, such as steel, hard alloys, copper, etc. It is particularly suitable for processing complex shapes and high-precision miniature mold components with small dimensions. Wire EDM is a non-contact machining process, avoiding the impact of cutting forces on the mold.
CNC turning is a rotating cutting process for mold materials implemented through computer numerical control lathes. CNC turning is mainly used to machine cylindrical components of molds, such as shafts, rods, sleeves, etc. By precisely controlling the tool movement and cutting depth, it can realize high-precision and high-efficiency machining. CNC turning plays an important role in mold manufacturing, especially suitable for machining axis and hole components of molds.
CNC turning can achieve high-precision and high-efficiency machining. It is applicable to various materials such as steel, aluminum, copper, etc. It can proessing complex shapes and precision dimensions to meet the requirements of molds.
Laser marking is a process that utilizes a laser beam to engrave marks, text, patterns and other information on the surface of molds. In the laser marking process, the laser beam scans the mold surface according to a preset path, using the energy of the laser to cause chemical or physical changes on the material surface to form permanent marks.
Laser marking can achieve high-precision and high-efficiency processing. It has advantages such as non-contact operation, clear and permanent marks. This machining method is suitable for identification marks, logos, numbers, QR codes, dates and other information labeling on molds. It is an indispensable processing step in mold manufacturing.
Polishing refers to the process of reducing the surface roughness of molds through manual, mechanical to achieve a glossy and smooth surface finishes.
In the polishing process, tools such as abrasive paper, grinding wheels, polishing cloths and polishing compounds are usually used to grind and polish the mold surface to remove machining marks and roughness, achieving the required level of surface smoothness.
Polishing can improve the surface quality of molds and endow them with better wear resistance, corrosion resistance and aesthetics. During polishing, the polishing force and time need to be controlled to avoid over-polishing causing mold deformation or damage. Polishing is commonly used in the final stage of mold machining to ensure the surface quality of molds meets requirements. The translation retains the original meaning without any changes.
Mold assembly refers to the process of assembling and fitting various machined mold components into the mold according to design requirements.
In the mold assembly process, first the individual components are cleaned and inspected to ensure their quality and dimensions meet requirements. Then according to the preset assembly sequence, the various components are assembled together and fixed using fasteners such as bolts, dowel pins and nuts. After assembly is completed, strict inspection is necessary to ensure tight fitting with no looseness between all mold components.
Mold assembly requires delicate operation and strict quality control to ensure assembly accuracy and reliability of the mold. After assembly, mold trial and debugging is also needed to ensure normal functioning of the mold.
Mold trial is conducted after mold assembly is completed by producing trial products to validate the mold performance and product quality.
During the trial, the flow of plastics in the mold needs to be observed, and molding parameters such as mold temperature and injection pressure adjusted to ensure smooth forming of plastics meeting product requirements. The molded samples will then be inspected and tested, including dimensional accuracy, appearance quality and material properties.
Sample mold trial is an important step in the mold making process, as it can find any issues or deficiencies with the mold so adjustments and improvements can be made promptly. Mold trials allow verification of mold reliability, stability and product quality.
Soft Injection toolings, also commonly referred to as rapid molds, are usually made of aluminum. Aluminum is softer than steel and cannot be hardened like steel.
During the component design process, in order to verify whether the plastic component design is reasonable and meets the assembly and product requirements, design changes may need to be made repeatedly. Therefore, before mass production, a sample mold, i.e. a soft mold, is usually made first to facilitate modification. When the design is stabilized and no longer changing, hard molds with multiple cavities are needed for mass production due to the limited capacity of single-cavity molds
The main advantages of soft injection molds are that they are highly adaptable, low cost and have a short manufacturing cycle. They are mainly used to shorten the mold manufacturing cycle and develop test plastic products for structure verification and testing, as well as confirmation of product performance, appearance and data.
Due to the relatively simple manufacturing process, soft molds cannot compare with hard molds which may affect the appearance and performance of the product.
The main drawbacks of soft injection molds are: low accuracy and surface quality, generally shorter life than hard molds, and easy to produce defects such as flash.
Hard Injection molds are generally made of steel. Due to its high strength and hardness, steel can withstand high injection pressures and temperatures, making it suitable for mass production. The manufacturing process of injection steel molds is relatively complex and costly, but they can provide high production efficiency and consistency. The most common P20 steel is not heat-treated, but its hardness is still significantly higher than aluminum and can be used for medium to small batch production.
For molds requiring even higher quality, mold steels with better hardness such as H13, NAK80, S136 can be selected. Molds made with these steels have life cycles between 500,000 and 10 million injection shots.
Durability: Hard molds can withstand high pressures and temperatures, thus having a long service life.
High precision: Hard molds have high manufacturing accuracy and can produce products with high precision and quality.
High production efficiency: Hard molds are suitable for mass production and can improve production efficiency and reduce production costs.
Repeatability: The dimensional stability and consistency of hard molds can ensure product consistency and repeatability.
Wide application range: Hard molds can be used for injection molding of various plastic materials, including thermoplastics, thermosets and elastomers.
High cost: The manufacturing process of hard molds is complex, requiring higher technical and equipment standards, so the cost is higher.
Long manufacturing cycle: It generally takes weeks or even months to manufacture hard molds as their manufacturing cycle is longer.
Low flexibility: Once the shape and size of hard molds is determined, it is difficult to modify them, so flexibility in product design and modification is relatively low.
High maintenance cost: Hard molds require regular maintenance and care to ensure performance and accuracy, so maintenance costs are higher.
Injection mold tooling play an extremely important role in modern industrial production. Their design and manufacturing quality directly affect the product quality, production efficiency and cost. Therefore, for mold manufacturers, continuously improving technical levels, optimizing mold design and manufacturing processes are critical to meet market demand and enhance competitiveness. At the same time, for users, selecting suitable injection molds and conducting proper maintenance and care are also important guarantees to ensure smooth production and stable product quality.