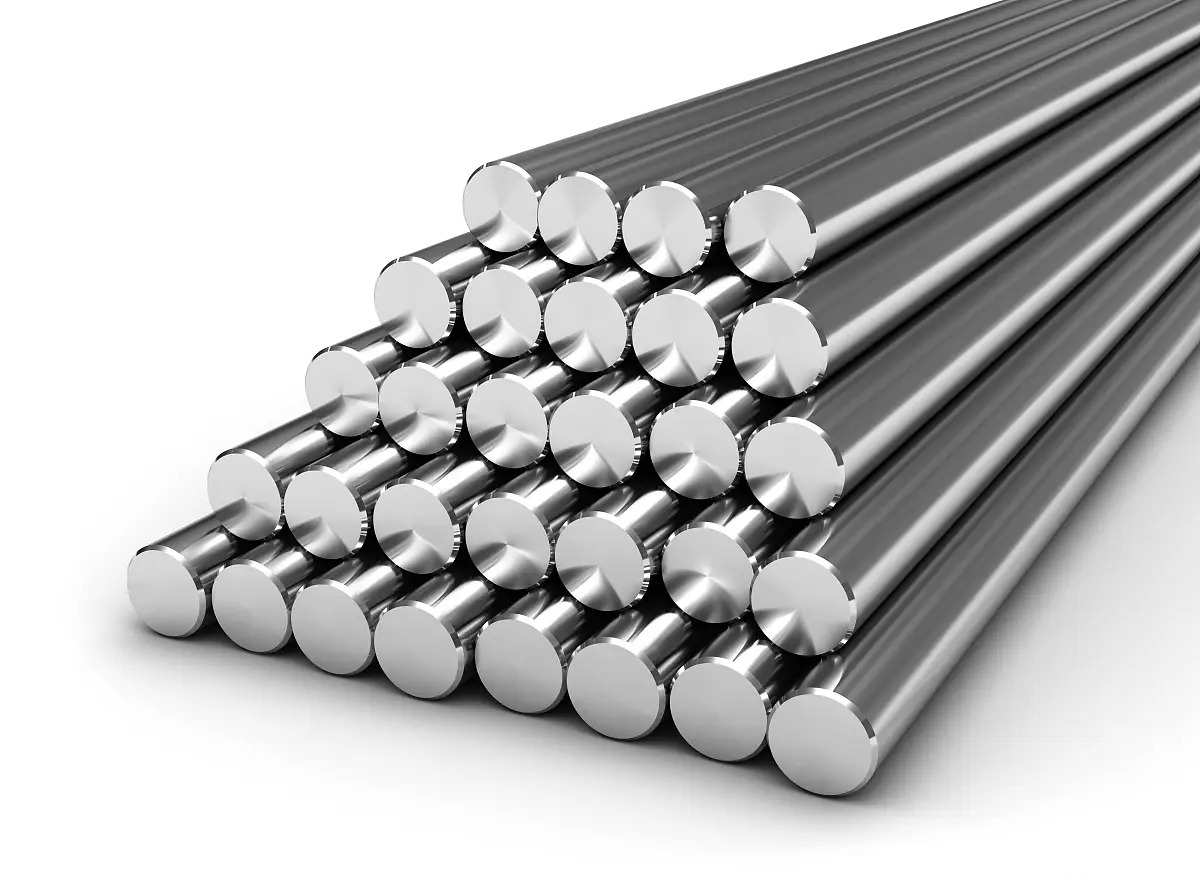
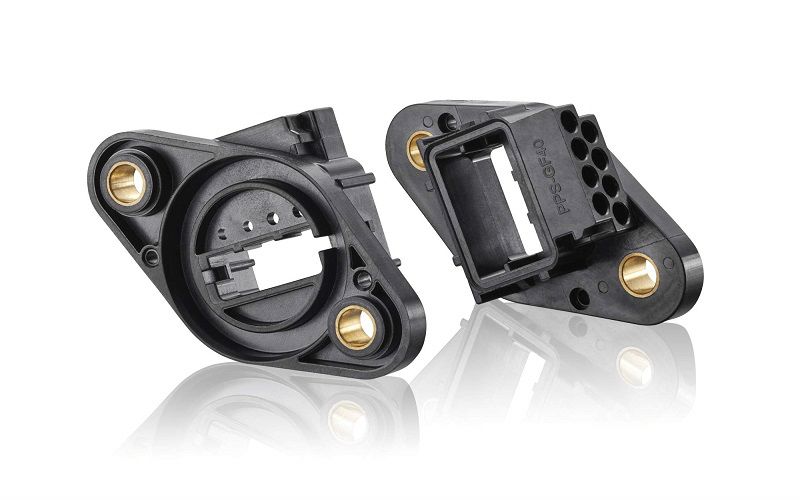
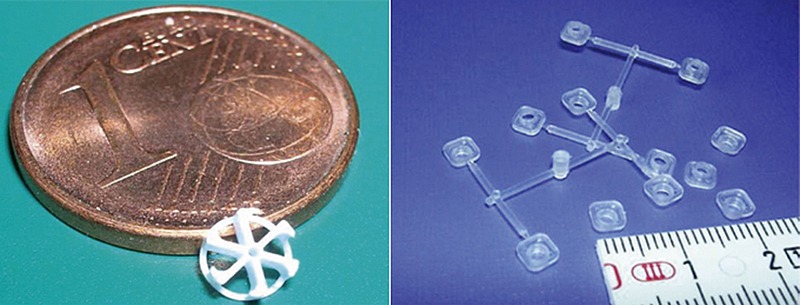
Nylon is a semi-crystalline thermoplastic that is a member of the polyamide family. It offers high strength, stiffness and dimensional stability, as well as elasticity and chemical resistance. Its properties make nylon widely used in the automotive, textile, aerospace and consumer goods industries.
This article will explain common nylon types, applications, properties, advantages etc. Nylon injection molding technological parameter and design considerations will also be discussed, with the goal of giving everyone a better understanding of nylon plastic.
1930s: Development began at DuPont to create an artificial silk that was stronger and more elastic than rayon. Scientist Wallace Carothers conducted experiments that led to the first prototype of nylon polymer.
1935: Carothers died before bringing nylon to market. Research continued under Dutch chemist Julian Hill.
1938: DuPont chemists Peter Scheommer and John Rex Whinfield accidently created the first fully synthetic thermoplastic polymer while trying to develop new polyamides – they named it nylon.
1939: DuPont announced nylon as the first fully synthetic fiber at the New York World’s Fair, branding it with the trade name “nylon”. Its strength yet flexibility created excitement.
1940s: Mass production of nylon began. Nylon replaced silk in applications like women’s stockings due to strong demand during WWII. New molded products emerged.
1950s: Nylon saw widespread use in apparel, carpets and upholstery. Molding techniques advanced. Nylon 6 and Nylon 6,6 became dominant commercial grades.
1960s: Automotive and appliance industries adopted nylon for parts. Use in mechanical components accelerated.
Today: Nylon maintains importance in textiles/fibers as well as engineering plastics for injection molding, 3D printing and other fabrication methods. Grades continue to be developed to meet modern needs.
Polyamide is commonly known as Nylon, and its English name is Polyamide (PA for short). Nylon is a synthetic aliphatic polyamide thermoplastic belonging to the class of polyamides. It is produced through step-growth polymerization of diamines and dibasic acids, forming repeating amide linkages along the macromolecular chain. The most prevalent industrial nylon varieties are nylon 6, derived from ε-caprolactam, and nylon 6,6 originated from adipic acid and hexamethylenediamine.
Due to strong inter-chain hydrogen bonding between amide groups, nylon polymers exhibit high tensile strength and stiffness even at elevated temperatures. Additionally, the aliphatic structure provides resilience and resistance to impact, abrasion as well as dissolution by many chemicals and moisture absorption. These key properties have led to widespread applications of nylon where high mechanical durability is required, such as in automotive, industrial and textile industries.
The molecular structure of nylon polymers allows for their unique combination of strength, rigidity, and durability. Nylon is formed through step-growth polymerization between aliphatic diamine and dibasic acid monomers, resulting in a linear macromolecular chain composed of repeating amide functional groups.
Specifically, the condensation reaction occurs as the amino group of the diamine reacts with the carboxyl group of the acid, releasing a water molecule and forming the amide linkage -CO-NH-. This yields a polyamide structure with the amide carbonyl and nitrogen alternately bonded along the polymer backbone. Common nylons like nylon 6,6 are synthesized from adipic acid and hexamethylenediamine, while nylon 6 polymerizes from caprolactam.
The amide linkages facilitate extensive interchain hydrogen bonding between the carbonyl and amino groups of adjacent polymer strands. This strong directional interaction plays a crucial role, inducing rigidity through crystallization of folded polymer regions and semi-crystalline morphology. The crystalline lamellae are interspersed with less organized amorphous regions. Together, the molecular microstructure endows nylon with its characteristic heat and chemical resistance as well as high tensile strength and stiffness even at elevated temperatures, owing to the hydrogen-bonded superstructure. These attributes have made nylon indispensable in numerous industrial applications demanding durable mechanical performance.
Tensile Strength | 90 – 185 N/mm² |
Regular Nylon Melting temperature
Reinforced nylon melting temperature |
230°C–280°C (446°F-536°F)
250-300°C (482-572°F) |
Notched Impact Strength | 5.0 – 13 Kj/m² |
Thermal Coefficient of expansion | 90 – 20/70 x 10-6 |
Max Cont Use Temp | 150 – 185℃ |
Chemical Formula | (C12H22N2O2)n |
Melting Point (°C) | ~220°C |
Tensile Strength | ~11,000 psi |
Impact Strength | ~0.6 fit-lb/in notched Izod |
Hardness Level (Rockwell) | R115 |
Flexural Modulus | ~16,000 psi |
Density | 1.13 – 1.35/1.41 g/cm3 |
Nylon has high tensile and impact strengths, ranging from 50-100 MPa and up to 200 kJ/m2 respectively, due to extensive hydrogen bonding between amide groups facilitating efficient load transfer across chains. Nylon 6,6 typically demonstrates higher tensile strength than Nylon 6 due to more densely-packed hydrogen bonding.
Approximately 2.7-4.1 GPa depending on moisture content and crystallinity level (higher crystallinity results in greater modulus). Nylon 6 typically has a modulus of 3.3-3.6 GPa.
Coefficient of friction is 0.25-0.40, with taber tests indicating wear volumes under 1 cm3 for 1000 revolutions of a 1 kg load on H-22 wheels. Reinforcements enhance abrasion resistance further.
Stiffness
Moduli typically exceed 1500 MPa, with glass transition temperatures (Tg) above room temperature fostering rigidity. Tg for many grades lies between 45-70°C due to constrained inter-chain segmental motions.
Wear resistance results from the hydrogen-bonded lamellar structure resisting shear planes. Fatigue endurance exceeds 109 cycles. Resistance to abrasives and cutting stems from high toughness and cohesive polymeric surface.
Impact strengths often surpass 100 kJ/m2 attributable to crystalline-amorphous phase segregation enabling energy dissipation via yield processes such as shear band formation rather than direct crack propagation.
Nylon Density is 1.1-1.35 g/cm3, 30-40% lower than comparable engineering metals like aluminum or steel, yet retaining commensurate mechanical attribute levels.
In general, nylons are inert to bases, dilute acids and alcohols at room temperature. Susceptibility to polar solvents increases with lowering of crystallinity. with concentrated acids cleaving amide bonds above 120°C.
Varies 140-210°C depending on loading conditions, with short-term resistance to over 250°C before thermally-induced degradation ensues. Retention of properties to -50°C.
Crystalline melting points range 130-250°C, limited primarily by decomposition onset starting above 300°C in air. Lower temperatures incur elastic modulus decreases.
Moldability arises from melt flow activated above the glass transition or melting point. Crystallization rate and extent govern cycle times.
Nylon is a semi-crystalline polymer. Part of the molecular chains are arranged in an orderly manner to form a crystalline region, and some are aggregated to form a non-crystalline region. This structure allows nylon to maintain its shape and resist deformation under usage conditions. Nylon molecular chains are bonded to each other through polar carboxamide bonds to form delocalized bonds. This combination is extremely stable, making it difficult for the nylon molecular chains to slide relative to each other, thereby maintaining the molecular size. Trace amounts of fillers such as glass fibers can also further improve the dimensional stability of nylon.
Nylon is insensitive to both temperature and humidity changes. Under normal use conditions, its linear expansion coefficient is very low, about 0.0001/°C.
Below are the different types of nylon plastics commonly used. The type of nylon raw material is selected based on the specific requirements of the application, including mechanical properties, chemical resistance, heat resistance and cost considerations.
This is the most common type of nylon plastic. Made from epsilon-caprolactam, it has good elasticity and abrasion resistance. The room temperature tensile modulus is 2.7-3.6GPa, with heat stability up to 50-80°C. Widely used in carpets, textiles and industrial parts due to low cost.
Produced from adipic acid and hexamethylenediamine, it has a higher melting point and stiffness, with a modulus of 3-4GPa. Commonly used for fiber spinning (plastic packaging nets), rubber reinforcement (tire cords) and engineering plastics. Heat stable up to 120°C.
Synthesized from sebacic acid and 1,10-decanediamine, it has high tensile strength and excellent creep resistance at high temperatures. Applied in mechanical parts operating in high-heat environments such as engine components. Heat stable up to 150°C.
Made from 1-dodecanediamine and sebacic acid, it has the highest melting point and is used where durable high-heat resistance is required, such as automotive bonnets. Heat stable up to 200°C.
Polymerized from 11-aminoundecanoic acid, it has outstanding resilience and chemical corrosion resistance. Suitable for applications like fuel lines requiring high performance nylon properties.
Produced from ω-laurolactam, it has self-lubricating properties and is used as low-friction bushes and fishing lines.
Thermally and chemically stable, used in applications such as sockets and bearings requiring corrosion resistance. Heat stable up to 130°C.
Filled with 20-40% glass fibers to enhance stiffness, strength and dimensional stability. Used in mechanical parts.
Contains molybdenum disulfide or PTFE for low friction. Used in gears and slider pads.
Formulated with additives like aluminum trihydrate or decabromodiphenyl oxide. Ratings of V-0 or 5VB.
Special grades meet FDA approval for food processing equipment due to low extractives.
Added compounds prevent discoloration and embrittlement from UV exposure. Used outside.
Nylon Plastic Processing Methods
Melted nylon is rapidly injected into a metal mold at high temperature and pressure, then cooled to solidify into the desired product shape. Suitable for mass production of complex components such as automotive and electrical parts.
Pre-formed nylon materials are cut, drilled and milled into shapes using computer numerical controlled machines. Common processes include milling, turning and drilling with accuracy up to 0.01mm. Suitable for low volume or customized products.
Melted nylon is pressed through a die by an extruder screw and rapidly cooled in mold cavities to form profiles, films, sheets and other continuous structures. Suitable for forming plastic films, pipes and other continuous structures.
3D objects are printed layer by layer through physical or chemical consolidation methods. It offers fast printing speed and design flexibility but at a higher cost. Suitable for customized samples or low volume production.
High Strength and Toughness: Nylon plastics exhibit high tensile and compressive strengths, which means they can resist both pulling and pushing forces effectively. This makes them suitable for applications where durability and impact resistance are crucial.
Good Fatigue Resistance: Nylon parts can withstand repeated bending and flexing without significant loss of mechanical properties. This fatigue resistance allows nylon to be used in parts that undergo cyclic loading, such as gears, bearings, and other mechanical components.
High Stiffness: Although nylon is not as stiff as some other engineering plastics, it still offers good stiffness-to-weight ratios, making it a lightweight yet strong material for structural applications.
Resistance to Solvents and Chemicals: Nylon plastics are relatively inert to many solvents and chemicals, including acids, alkalis, and fuels. This chemical resistance makes nylon suitable for use in harsh environments where exposure to chemicals is a concern.
Good Moisture Resistance: Nylon’s resistance to moisture absorption ensures that its mechanical properties are maintained even in damp or humid conditions. This is beneficial in applications where exposure to moisture is unavoidable.
Thermal Plasticity: Nylon plastics are thermoplastic, meaning they can be easily melted and shaped into desired forms using conventional molding techniques such as injection molding, extrusion, and blow molding.
Flexible Processing Options: The thermoplastic nature of nylon allows for a wide range of processing options, including machining, welding, and bonding, which further enhance its versatility in manufacturing processes.
Affordable Material: Compared to some other engineering plastics and metals, nylon is relatively affordable, making it a cost-effective material for large-scale production.
Long-Term Durability: The durability and resistance to wear and tear of nylon plastics mean that they have a long lifespan, providing value for money in the long run.
Recyclability: Many nylon plastics are recyclable, which helps to reduce waste and conserve resources. The recycling of nylon involves melting down used nylon parts and reusing them to create new products.
Biodegradability: Some types of nylon, such as nylon 6,6, can be produced using renewable resources like castor oil, making them more environmentally friendly. Additionally, research is ongoing to develop fully biodegradable nylon variants that can be used in sustainable applications.
The amide groups in nylon molecules are easily affected by high-energy radiation like heat and light, which may cause molecular chain scission and result in property degradation over time.
The strong bonds between alkyl and amino groups in nylon molecules make the structural structure tight and difficult for small molecules like O2 and H2O to pass through, resulting in low gas permeability.
The melting point range of different nylons is 130-250°C, and below 150°C is preferable, above which will lead to deterioration in properties.
The resistance to oil, acids, bases and organic solvents is generally poor, especially susceptible to chlorides and phenols.
Hydrolysis can break the bonds between nylon molecules, reducing strength and plasticity while causing swelling and deformation issues.
Nylon raw materials themselves are more expensive than other general engineering plastics, and processing costs are also higher.
Absorbed water molecules increase the intermolecular spacing of nylon and lead to dimensional deformation and property degradation.
The conditions of the nylon injection molding process are relatively harsh, and any small detail plays a key role in the result. Here are some key considerations for the nylon injection molding process.
Since nylon material is hygroscopic, it must be dried before injection molding. Excessive moisture content can cause bubbles, deformation or other defects in injection molded parts. Drying temperature and time depend on the specific nylon type and moisture level. Typically, nylon needs to be dried at a temperature of 80°C to 100°C for about 4 hours.
The shrinkage rate of pure nylon is relatively large. The shrinkage of nylon material after injection molding will cause warping, reduced strength, poor color, etc. The mold temperature and molding process should be appropriately controlled to reduce such defects.
Venting is essential to release air trapped during the injection process. Higher mold temperatures and poor ventilation can cause defects such as whitening in nylon plastics. The gate should be optimized and more vents should be installed to help exhaust.
Appropriate melt temperature can ensure the fluidity of nylon plastic, reduce internal stress and improve the quality of injection molded parts. Nylon has a specific molding temperature range, typically nylon has a melt temperature between 220°C and 280°C. It melts and flows normally within this temperature range. If the melt temperature is too high, the raw materials will decompose and the surface will become white.
Usually the Nylon mold temperature is controlled at about 80~90℃. According to the different shapes of plastic parts, the mold temperature can be fine-tuned. Mold temperature will affect the mechanical properties of injection molded parts, such as stiffness, strength, and may also reduce toughness.
Injection pressure determines the filling speed and filling quality of plastic in the mold. The viscosity of melt nylon is low and does not require excessive injection pressure. Too much pressure can cause nylon injection molded parts to deform or produce other defects, but too little pressure can also cause insufficient filling. In general, nylon material injection pressure usually ranges from 8000 psi to 20000 psi (55 MPa to 138 MPa)
The injection speed affects the flow behavior and filling effect of the plastic in the mold. Appropriate injection speed can ensure that the nylon melt fills the mold evenly and avoids problems such as flow marks or under-injection. Because the viscosity of nylon melt is low and the speed is medium, it should not be too fast. Too fast will cause defects such as burrs.
Compared with the cooling time of injection molding of other plastics, the cooling time of nylon materials is shorter. The cooling time may be affected by factors such as part thickness, shape, mold design and cooling system efficiency. The melt viscosity of nylon material is low and it cools quickly. To avoid gate freezing, the cooling time should be short. This also shortens overall cycle time and reduces cost per part. This is one of the reasons why many plastic parts choose nylon materials.
The mold design of nylon injection molding needs to take into account the shrinkage rate of the plastic, gate location, filling characteristics, cooling, exhaust and other factors to ensure the dimensional accuracy, appearance quality and performance of the injection molded parts.
After injection molding is completed, post-processing of the injection molded parts may be required, such as heat treatment, annealing, painting, printing, ultrasonic welding, etc. Post-processing can further improve the performance of injection molded parts, such as improving dimensional stability, improving surface quality or enhancing mechanical properties.
PEEK is a material used in harsh environments because of its unique and valuable properties. PEEK material has excellent performance and wide application fields, and can meet the needs of different fields. With the continuous advancement of science and technology and the expansion of application fields, the application prospects of PEEK materials will be broader. Here are some popular applications including:
Nylon plastics are widely used in the aerospace industry due to their lightweight, strength, and resistance to high temperatures.
Examples: Nylon is often found in aircraft components such as fuel lines, gaskets, and fasteners. It is also used in the manufacture of helicopter rotor blades and aircraft seats due to its durability and flame-resistant properties.
Gears, bushings, pulleys, fasteners, tubes, ducts, panels and other structural or functional components demanding strength and durability in aircraft engines, cabins, etc.
The automotive industry relies heavily on nylon plastics for various components due to their durability, weight reduction potential, and cost-effectivenesss.
Examples: Nylon is commonly used in automotive parts such as fuel pumps, hoses, bearings, and intake manifolds. It is also found in seatbelt anchors, door latches, and other safety-related components. Bearings, gears, pulleys, belts, hoses, timing belts, dashboards, trims, seat parts, air intake manifolds, oil pans and other under-the-hood components requiring heat resistance.
Nylon’s resistance to heat, solvents, and electrical insulation properties make it ideal for use in the electrical and electronics industry.
Examples: Nylon is commonly used in wire insulation, circuit board components, connectors, and switches. It is also found in the housing of electrical components and devices such as sockets, plugs, and resistors.Insulators, connectors, switches, casings, wire and cable sheathing, printed circuit boards for its self-extinguishing property and electrical insulation.
Nylon’s durability, flexibility, and resistance to wear and tear make it a popular choice for consumer goods. Examples: Nylon is widely used in clothing, fabrics, and textiles due to its strength and resistance to wrinkling. It is also found in household items such as ropes, brushes, and containers. Additionally, nylon is used in sports equipment like tennis rackets, ski boots, and hockey sticks due to its lightweight and durability. Textiles (clothing, carpets), sporting goods (fishing lines, gears), household appliances (washing machine components), electronics casings, 3D printing filaments.
The strength, toughness, and chemical resistance of nylon plastics make them ideal for use in industrial components that require durability and longevity.
Examples: Nylon is commonly used in gears, bearings, pulleys, and other mechanical components. It is also found in pipes, valves, and fittings for fluid handling systems due to its resistance to corrosion and wear. Gears, cams, washers, bushes, pulleys, spacers, guides, rods, structural parts employed in manufacturing machinery for their rigidity and machinability.
Nylon’s biocompatibility, resistance to sterilization, and low-friction properties make it suitable for use in medical devices and equipment.
Examples: Nylon is used in surgical sutures, catheters, and other medical implants due to its biocompatibility. It is also found in dental instruments, orthopedic devices, and medical tubing due to its durability and resistance to chemical cleaners and sterilants. Surgical instruments, prosthetics, tubings, trays, handles, syringe parts, diagnostic equipment components valued for biocompatibility, fatigue resistance and processability.
Attractive Plastics is a China leader in custom nylon plastic injection molding manufacturer. We have over 20 years of experience in plastic injection molding polyamide material parts and have completed many successful projects. We help customers make various nylon injection molds, injection molding manufacturing and processing, mold design, etc. We can injection mold a variety of polyamides, including nylon 6, 66, 11 and 12, including unfilled, fiberglass and mineral-filled formulations, toughened and conductive grades, and high temperature grades.
So, if you are looking for nylon injection molding supplier, Attractive Plastics is your best choice.
As an important engineering plastic, nylon is widely used in various industries because of its good properties. Nylon comes in many different forms, but the most common types are PA6, PA66 and PA12. Fillers such as glass fiber are often added to enhance the mechanical and thermal properties of nylon and reduce shrinkage, but this also sacrifices flexibility.