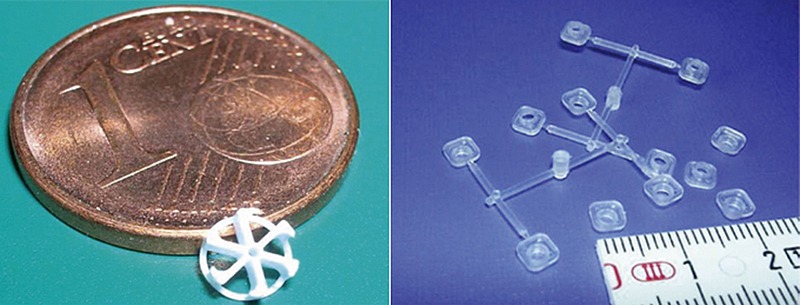
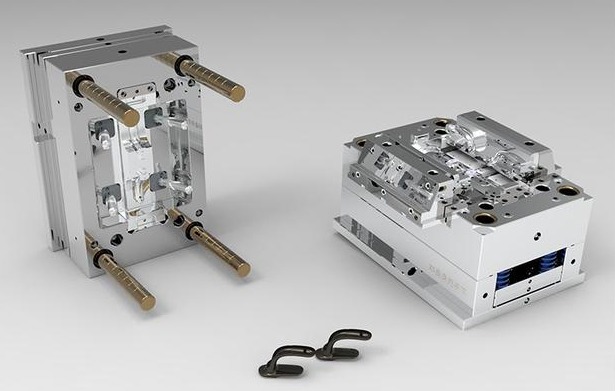
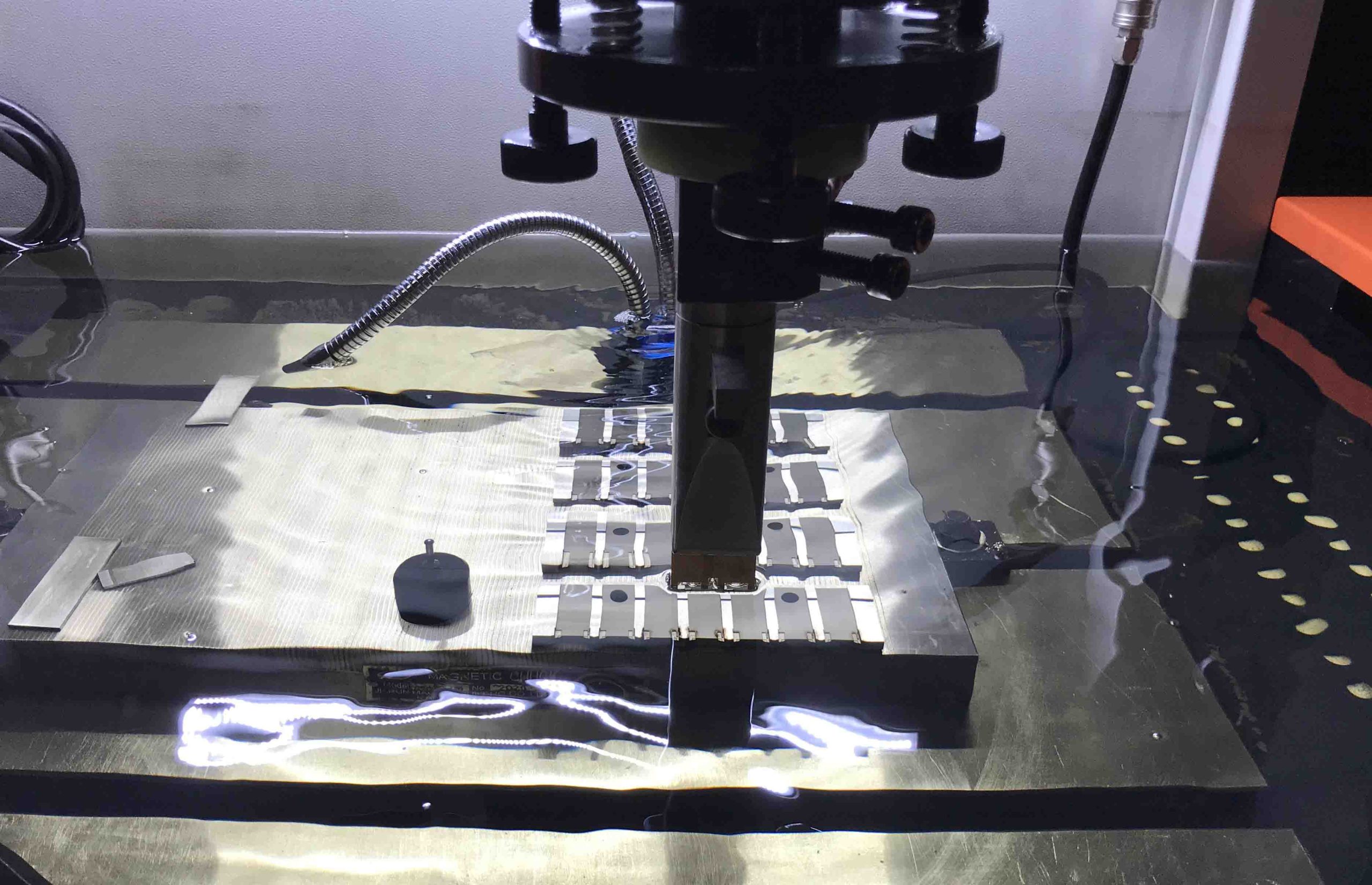
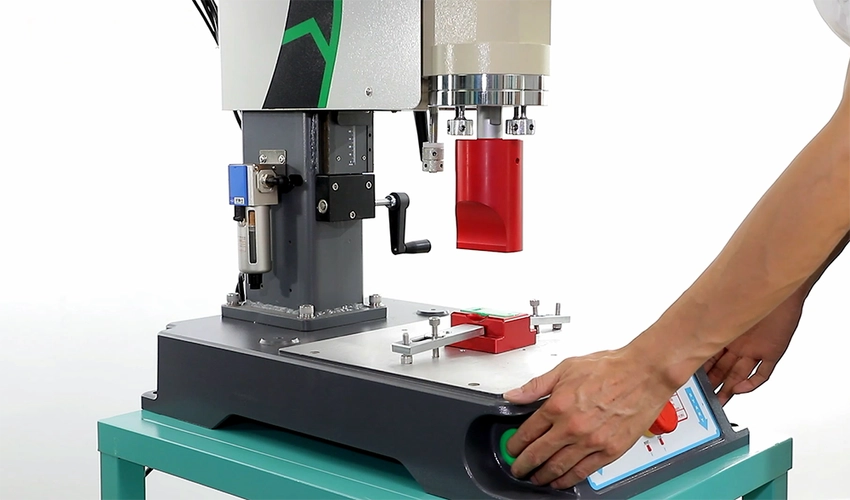
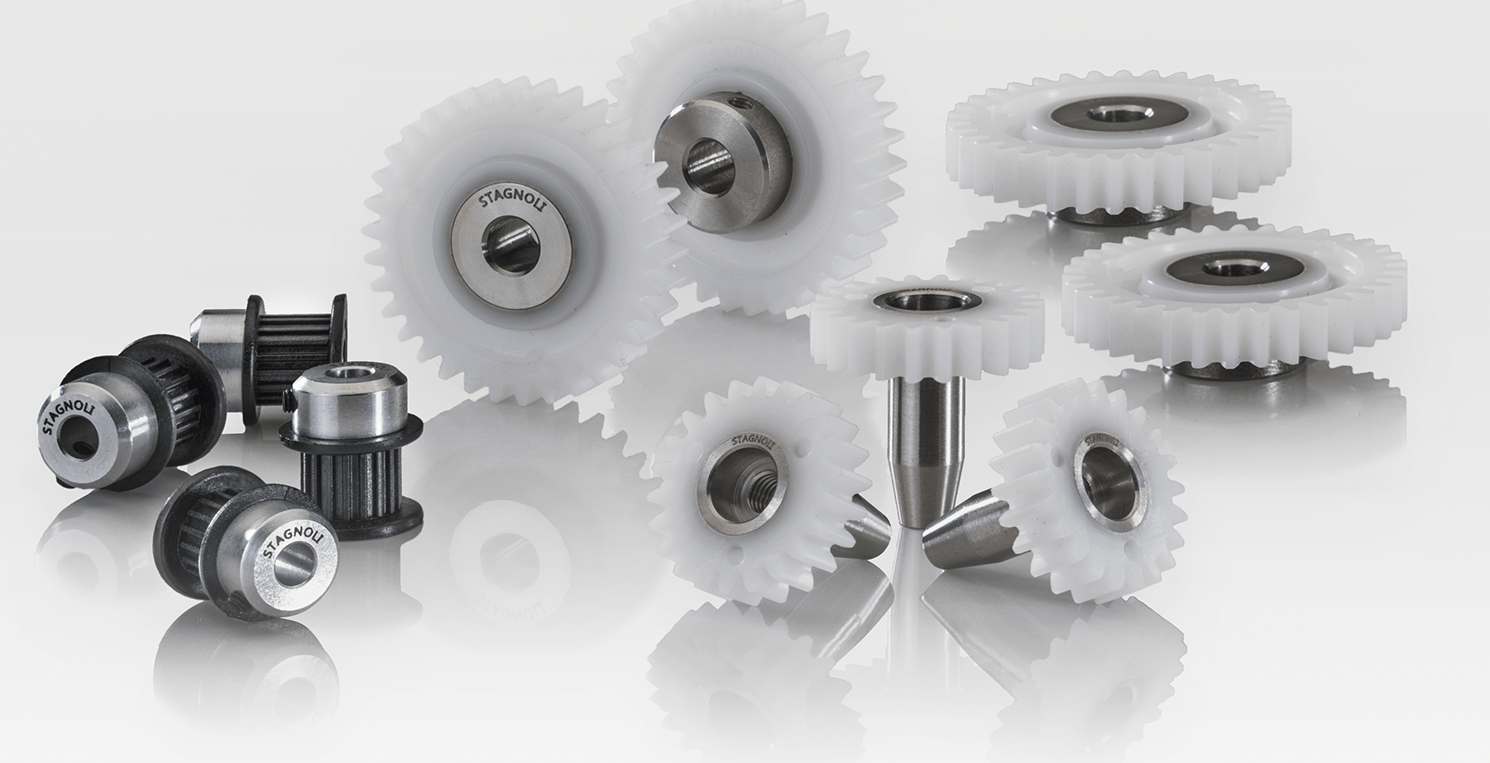
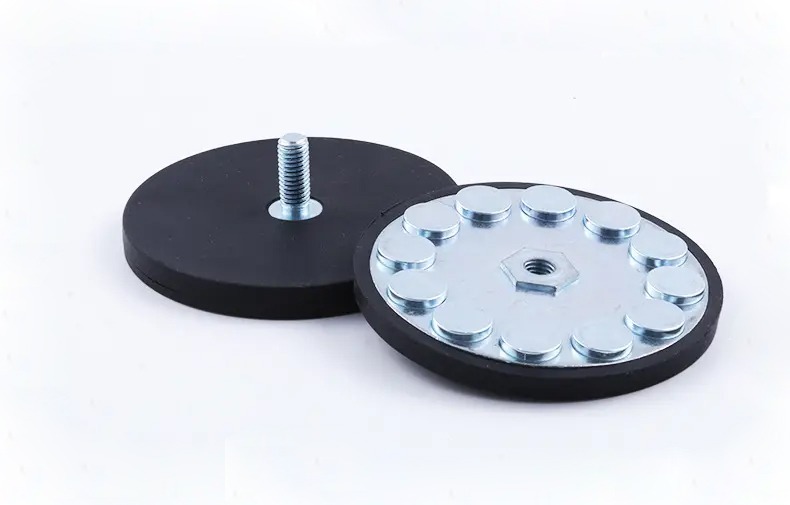
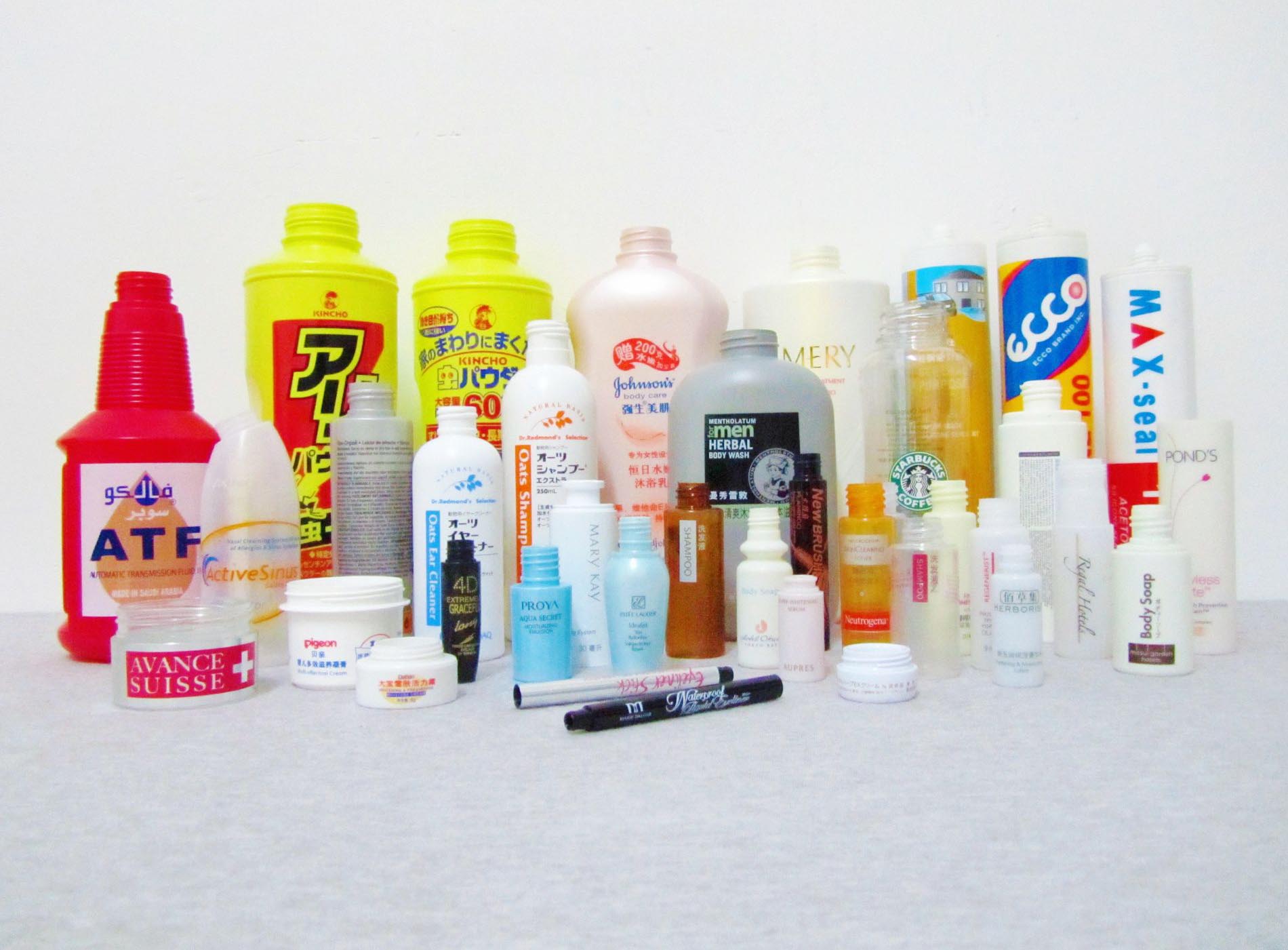
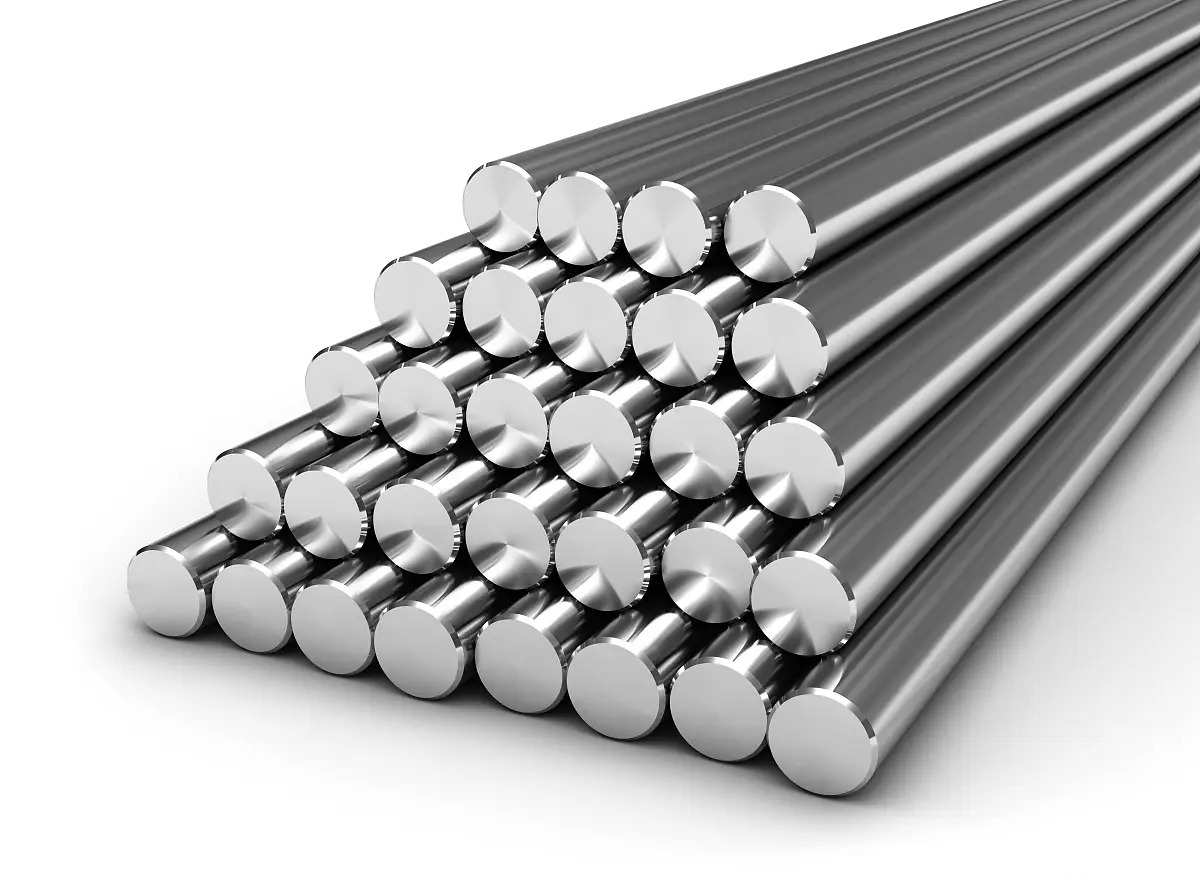
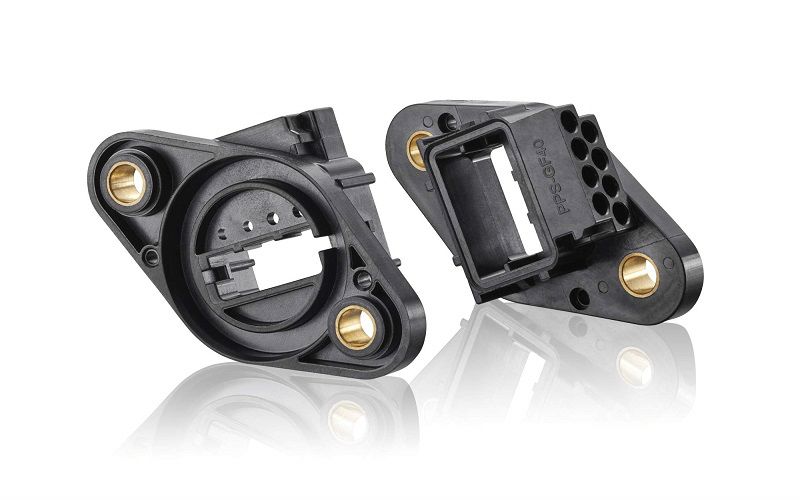
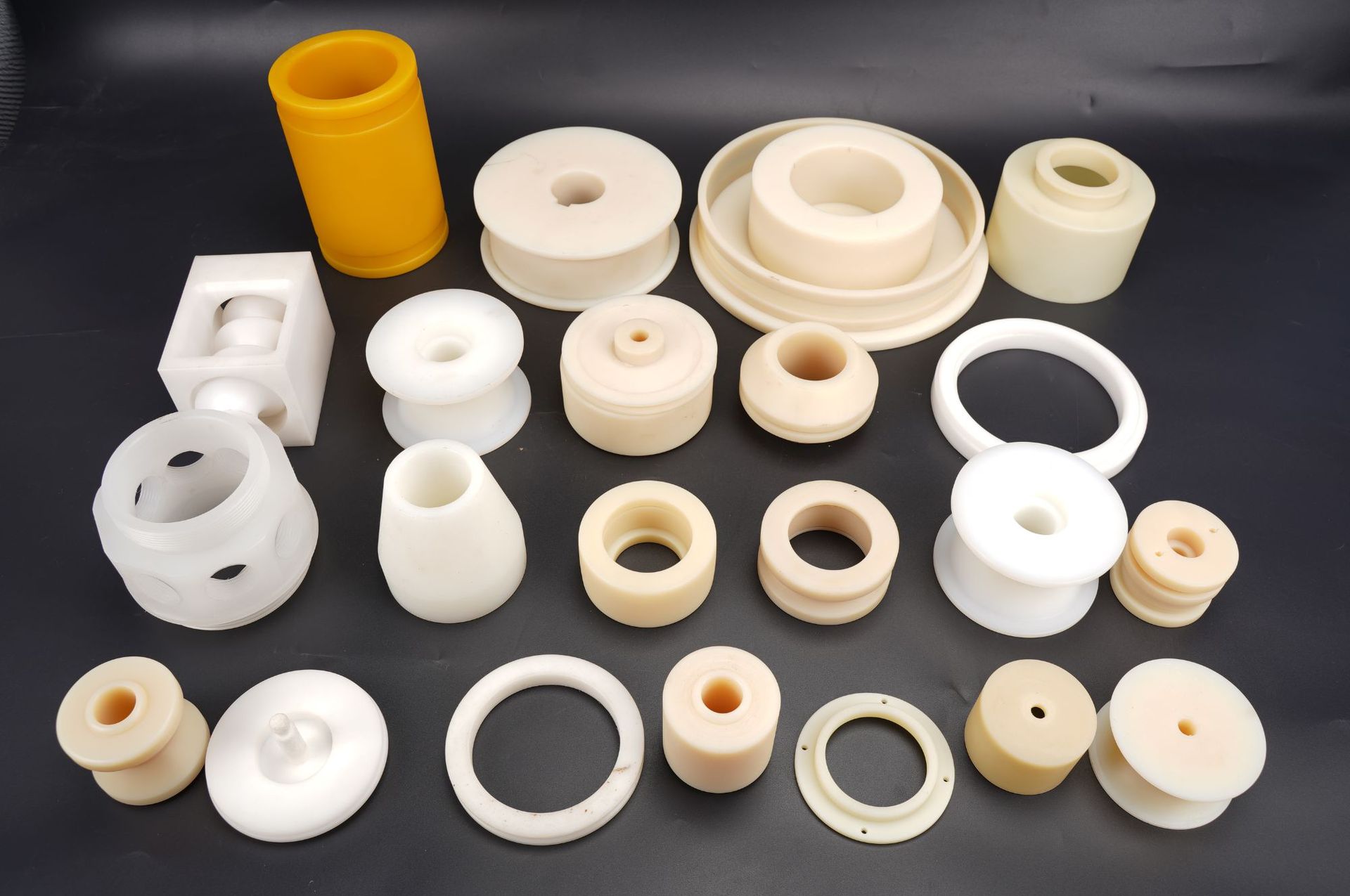
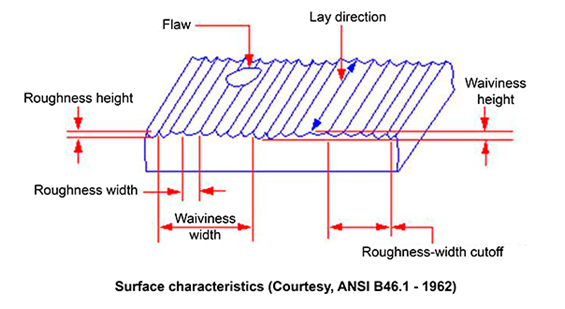
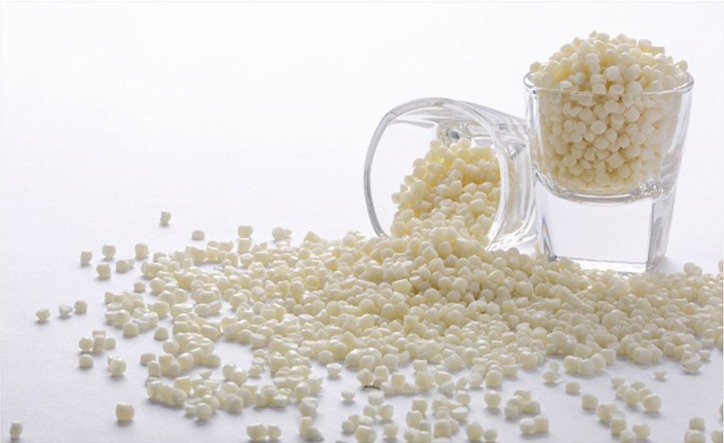
In the intricate world of precision manufacturing, micromolding stands as a testament to human ingenuity, pushing the limits of microscopic size. From complex gears in medical devices to delicate components in electronics, micromolding has revolutionized industries by creating parts with unparalleled precision and detail.
In this article, we’ll take a closer look at the intricacies of micromolding, the challenges, and what it takes to successfully create a micro plastic part.
Micro molding, or micromolding, refers to a niche technology in the field of injection molding, specifically used for manufacturing micro-features on larger parts or for producing parts with overall dimensions, functional areas, or tolerances measured in millimeters or even micrometers. It is a miniaturized version of the conventional injection molding process but with much tighter tolerances and smaller dimensions.
Micro molding has several key characteristics that distinguish it from traditional molding processes:
Although micro molding is more difficult than conventional injection molding, there are still certain rules to follow. The key to mastering the process from micro plastic part design to molding is to carefully check and verify every step related to molding from the beginning of design. It is also helpful to verify with experience to prevent possible injection defects. helps to increase the probability of successfully making micro plastic parts. Here are some key factors of micro molding that we have summarized based on our 15 years of experience
Miniaturization challenges: Designing for micro parts requires careful consideration of size reduction. Features that are easily manufacturable at larger scales may pose significant difficulties when scaled down. For example, thin walls need to be carefully designed to ensure proper filling and structural integrity. The aspect ratio of features such as ribs and bosses must be optimized to avoid issues like warping or incomplete filling.
Tolerance requirements: Micro parts often have extremely tight tolerances. The design must take into account the allowable dimensional variations. Tighter tolerances may require more precise manufacturing processes and quality control measures. For instance, a micro gear may have a tolerance of only a few microns on its pitch diameter, which demands highly accurate tooling and injection molding parameters.
Geometric complexity: Complex geometries can be achieved in micro parts, but they need to be designed with manufacturability in mind. Undercuts and internal cavities may require special mold designs such as side actions or collapsible cores. The draft angles of the part also play a crucial role. In micro molding, even a small deviation in draft angle can lead to difficulties in part ejection and potential damage to the part or the mold.
Cavity and core design: The cavity and core must be designed to high precision to achieve the desired part geometry. Surface finishes of the mold components are critical as they directly affect the surface quality of the molded part. For example, a mirror finish on the cavity surface may be required for optical parts. The cooling channels in the mold also need to be carefully designed. In micro molding, proper cooling is essential to control the cycle time and ensure consistent part quality. The channels should be sized and located to provide uniform cooling across the mold, taking into account the small size of the part and the high heat transfer rates.
Gate design: The gate is the entry point of the molten plastic into the mold cavity. In micro molding, the gate size and location are crucial. A very small gate may be needed to minimize the vestige left on the part, but it must also allow for proper filling. For example, a pinpoint gate can be used for small, thin-walled parts, but it requires careful control of the injection pressure and speed to ensure that the plastic can flow through without clogging or causing excessive shear stress. The gate location should be chosen to promote balanced filling of the cavity and avoid issues like jetting or air entrapment.
Ejection system design: Ejecting micro parts from the mold without damage is a challenge. The ejection system, including pins and sleeves, must be designed to apply minimal force and have precise positioning. For delicate parts, a combination of ejector pins and air ejection may be used. The ejector pins should have a small diameter and smooth surface to avoid marking the part. The travel and force of the ejection system need to be carefully calibrated to ensure proper part ejection while maintaining the integrity of the part and the mold.
Melt viscosity: Materials with low melt viscosity are preferred in micro injection molding as they can flow more easily into the small and complex mold cavities. For example, some specialty engineering plastics have been developed with modified molecular structures to reduce viscosity. However, the trade-off is that low-viscosity materials may have lower mechanical properties. So, a balance must be struck between flowability and the required part performance.
Thermal properties: The material’s thermal conductivity and heat capacity affect the cooling process. Materials with high thermal conductivity can cool faster, reducing the cycle time. But they may also cause rapid solidification near the mold walls, leading to issues like surface defects or internal stresses. The glass transition temperature and melting point of the material are also important. They determine the processing temperature range and the stability of the molded part during use. For example, a material with a high glass transition temperature may be suitable for applications where the part will be exposed to elevated temperatures.
Fillers and additives: Fillers such as glass fibers or carbon nanotubes can be added to improve the mechanical properties of the molded part. However, in micro molding, the size and distribution of fillers need to be carefully controlled. Large or agglomerated fillers can clog the small mold features and affect the flow of the molten plastic. Additives like lubricants can improve the flowability of the material, but they may also affect the surface quality and adhesion properties of the part.
Precision and accuracy: The injection machine must be capable of delivering precise amounts of plastic material with high accuracy. The screw diameter and stroke length should be appropriate for the small shot volumes required in micro molding. For example, a machine with a small screw diameter and fine control of the injection volume can accurately meter the small amounts of material needed for a micro part. The injection pressure and speed controls must also be highly precise. Micro parts often require high injection pressures to fill the small cavities, and the machine should be able to maintain a stable pressure profile throughout the injection process.
Clamping force: Although micro parts are small, the clamping force required can still be significant due to the high injection pressures. The clamping force must be sufficient to keep the mold closed during injection and prevent flash. However, excessive clamping force can damage the mold or the machine. The clamping unit should have accurate force control and be able to adjust to different mold sizes and part geometries. For example, a servo-electric clamping system can provide more precise force control compared to a traditional hydraulic system.
Machine control and monitoring: Advanced machine control systems are essential for micro injection molding. They allow for precise programming of injection parameters such as pressure, speed, and temperature profiles. The machine should also have real-time monitoring capabilities to detect any variations in the process. For example, sensors can monitor the melt temperature, cavity pressure, and screw position. This data can be used to adjust the process parameters in real-time to ensure consistent part quality and detect any potential defects or malfunctions.
Mold tryout: Before full-scale production, a mold tryout is conducted. This involves testing the mold in the injection machine with the selected material and process parameters. The purpose is to identify and correct any issues with the mold design, such as improper filling, flashing, or part ejection problems. During the tryout, adjustments can be made to the gate size, cooling channels, or ejection system. For example, if there is incomplete filling in a particular area of the part, the injection speed or pressure can be adjusted, or the gate location can be modified.
Process optimization: After the mold is found to be functional, the injection process is optimized. This includes fine-tuning the temperature, pressure, and speed settings to achieve the best part quality and production efficiency. Statistical process control (SPC) methods can be used to analyze the process data and determine the optimal parameter settings. For example, by analyzing the variation in part dimensions over multiple shots, the injection pressure and temperature can be adjusted to minimize the dimensional spread and ensure that all parts meet the required tolerances.
Design of Experiments (DOE): DOE is a powerful tool in mold and process validation. It allows for systematic testing of multiple process parameters and their interactions. By varying factors such as injection pressure, temperature, and mold temperature simultaneously and analyzing the results, the most significant factors affecting part quality can be identified. For example, a DOE study may reveal that the interaction between injection speed and mold temperature has a major impact on the surface finish of the part, enabling the optimization of these parameters for the best surface quality.
Temperature: The barrel temperature, nozzle temperature, and mold temperature all play crucial roles. The barrel temperature must be set to melt the plastic material evenly. For example, for a thermoplastic elastomer, the barrel temperature may need to be in the range of 180 – 220°C. The nozzle temperature should be carefully controlled to ensure proper flow of the molten plastic into the mold cavity. The mold temperature affects the cooling rate and the surface quality of the part. A higher mold temperature may result in a better surface finish but a longer cycle time, while a lower mold temperature can cause faster cooling and potential warping or surface defects.
Pressure: Injection pressure is required to force the molten plastic into the mold cavity. In micro molding, high injection pressures are often necessary due to the small gate and cavity sizes. However, excessive pressure can cause issues like flash, warping, or damage to the mold. The holding pressure, which is applied after the cavity is filled, is important for compensating for the shrinkage of the material as it cools. The pressure profile, including the ramp-up and ramp-down rates, needs to be carefully controlled. For example, a slow ramp-up of injection pressure can help to avoid jetting and ensure a smooth filling of the cavity.
Speed: The injection speed affects the flow behavior of the molten plastic. A high injection speed can cause turbulence and air entrapment, leading to voids or surface defects in the part. A slow injection speed may result in incomplete filling or a long cycle time. The speed profile, similar to the pressure profile, can be adjusted to optimize the filling process. For example, a variable injection speed can be used, starting slow to fill the gate area and then increasing the speed to fill the main cavity.
Regular inspection: Molds should be regularly inspected for signs of wear, damage, or contamination. Visual inspection can detect issues like cracks in the cavity or core, worn ejector pins, or deposits on the mold surface. For example, if there are scratches on the cavity surface, it can affect the surface quality of the molded parts. The inspection frequency depends on the production volume and the type of material being molded. Higher production volumes and abrasive materials may require more frequent inspections.
Cleaning methods: Proper cleaning of the mold is essential to maintain its performance. Different cleaning methods can be used depending on the type of material and the level of contamination. Chemical cleaning agents can be used to remove residues from the plastic material. For example, a solvent-based cleaner may be effective for removing certain types of adhesives or additives left on the mold. Ultrasonic cleaning can be used to remove small particles and debris from hard-to-reach areas of the mold. The mold should also be dried thoroughly after cleaning to prevent rust or other forms of corrosion.
Lubrication: The moving parts of the mold, such as ejector pins and slides, need to be lubricated regularly. The lubricant should be compatible with the mold material and the plastic being molded. It helps to reduce friction and wear, ensuring smooth operation of the ejection system and other moving parts. For example, a silicone-based lubricant may be suitable for molds used in micro injection molding of certain plastics.
Dimensional measurement: Precise dimensional measurement is crucial for micro parts. Coordinate measuring machines (CMMs) with high accuracy and resolution are often used. For example, a CMM with a measurement accuracy of ±0.5 microns can measure the dimensions of a micro gear with great precision. Optical measurement techniques such as microscopy and interferometry can also be used to measure surface roughness and other micro-scale features. The measured dimensions are compared to the design specifications, and any deviations are analyzed to determine the cause and take corrective actions.
Visual inspection: Visual inspection is used to detect surface defects such as scratches, blemishes, or flash. Microscopes with different magnifications are used depending on the size of the part and the level of detail required. For example, a stereo microscope with a magnification range of 10 – 100x can be used to inspect the surface of a micro connector. Automated visual inspection systems can also be employed to increase inspection speed and accuracy. These systems use cameras and image processing software to detect and classify defects.
Material property testing: In addition to dimensional and visual inspection, the material properties of the molded part may need to be tested. This includes tests such as tensile strength, hardness, and thermal stability. For example, a micro tensile testing machine can be used to measure the tensile strength of a micro-sized plastic specimen. The results of these tests are compared to the material specifications to ensure that the part meets the required performance standards.
Gentle handling: Micro parts are delicate and require gentle handling to avoid damage. Specialized handling tools and fixtures may be needed. For example, vacuum tweezers can be used to pick up and transfer micro parts without applying excessive force. The handling process should also be designed to minimize the risk of electrostatic discharge (ESD), as ESD can damage sensitive electronic components. Anti-ESD mats and wrist straps can be used in the handling area.
Packaging design: The packaging for micro parts must protect them during storage and transportation. It should provide a stable and clean environment. For example, micro parts may be packaged in anti-static trays or blister packs. The packaging material should be chosen to prevent scratches, contamination, and damage from mechanical shock. Desiccants can be included in the packaging to control humidity, especially for parts that are sensitive to moisture. The packaging should also be labeled clearly with part identification, quantity, and any special handling instructions.
By addressing these key elements, many micro injection molding manufacturers can achieve successful micro-injection molding, producing high-quality, precision micro-components that meet the demands of various industries.
Micro injection molding is a specialized process that presents several technical challenges distinct from conventional injection molding. Here are the key challenges succinctly summarized:
Micro injection molding can be expensive due to the high cost of tooling, specialized materials, and advanced manufacturing processes. The relatively low production volumes of micro molded parts may not justify the high initial investment. Cost-effective solutions need to be developed to make micro injection molding more accessible and competitive.
Micro injection molds require extreme precision and accuracy to produce parts with micron-level tolerances. The complexity lies in the minute dimensions, which demand high-resolution design and manufacturing techniques. Variability in mold performance can lead to inconsistencies in part quality.
Micro molds need to withstand high injection pressures without deforming, which poses a significant challenge in material selection and mold construction. The intricate geometries of micro molds make them difficult and expensive to manufacture, requiring specialized machining techniques and equipment.
Managing material flow is critical to avoid defects such as underfills or weak sections. Uniform cooling is equally important due to the small size of the parts, which makes monitoring cooling rates challenging. Proper layout of cooling channels and precise temperature regulation are essential.
The high level of precision in micro injection molding necessitates rigorous quality assurance. Inspecting and measuring micro molded parts is a complex task. Conventional inspection methods may not be sufficient, and specialized equipment and techniques are often required. The small size of the parts makes it difficult to detect defects such as voids, flash, and warpage. Accurate measurement of dimensions and tolerances is crucial but can be challenging due to the microscopic nature of the parts.
Micro molded parts often require injection pressures upwards of 30,000 to 50,000 psi and very short injection times, typically less than 0.1 seconds. This demands robust and highly precise tools to handle the high pressures without causing damage to delicate core pins. 5. High-Cavitation Tools: Micro injection molding often involves high-cavitation tools, which present challenges in maintaining balanced flow of molten plastic to each cavity. It is vital to ensure that all cavities are filled simultaneously and uniformly to avoid defects like air traps or voids.
The time that the molten plastic spends in the barrel before injection is critical in micro-molding. Improper residence time can lead to material degradation, color and property variations, and contamination, especially with heat and shear-sensitive materials like bioresorbable polymers.
The small size of micro molded parts complicates assembly and handling. Specialized equipment and techniques are required to handle these tiny components without causing damage, which adds to the complexity and cost of the process
Precision molds, advanced technology and processing equipment, and proven injection molding processes are essential for success in micro injection molding. As a reliable partner, Attractive Plastics offers comprehensive custom micro injection molding services that utilize advanced technology to bring your concepts to life. Rely on our highly skilled and experienced engineering team to bring you the confidence that you are getting the best injection molding manufacturing solution for your project.
Plastic micro injection molding is able to produce extremely small, close tolerance micro plastic parts with high precision, making it an essential manufacturing process for industries requiring miniaturization, precision engineering, and aerospace.