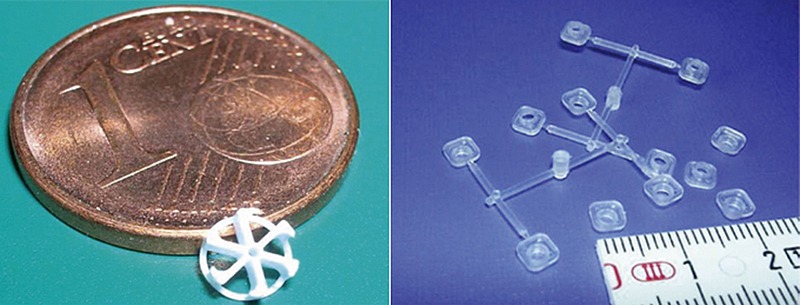
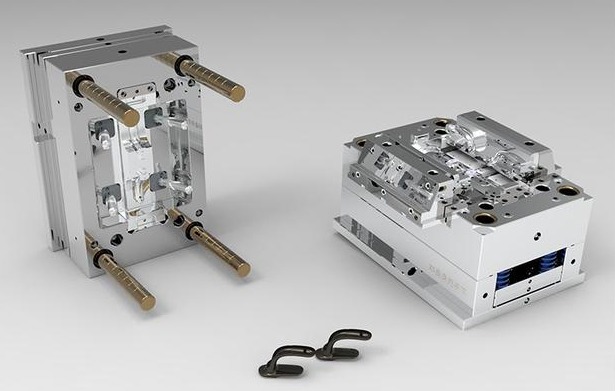
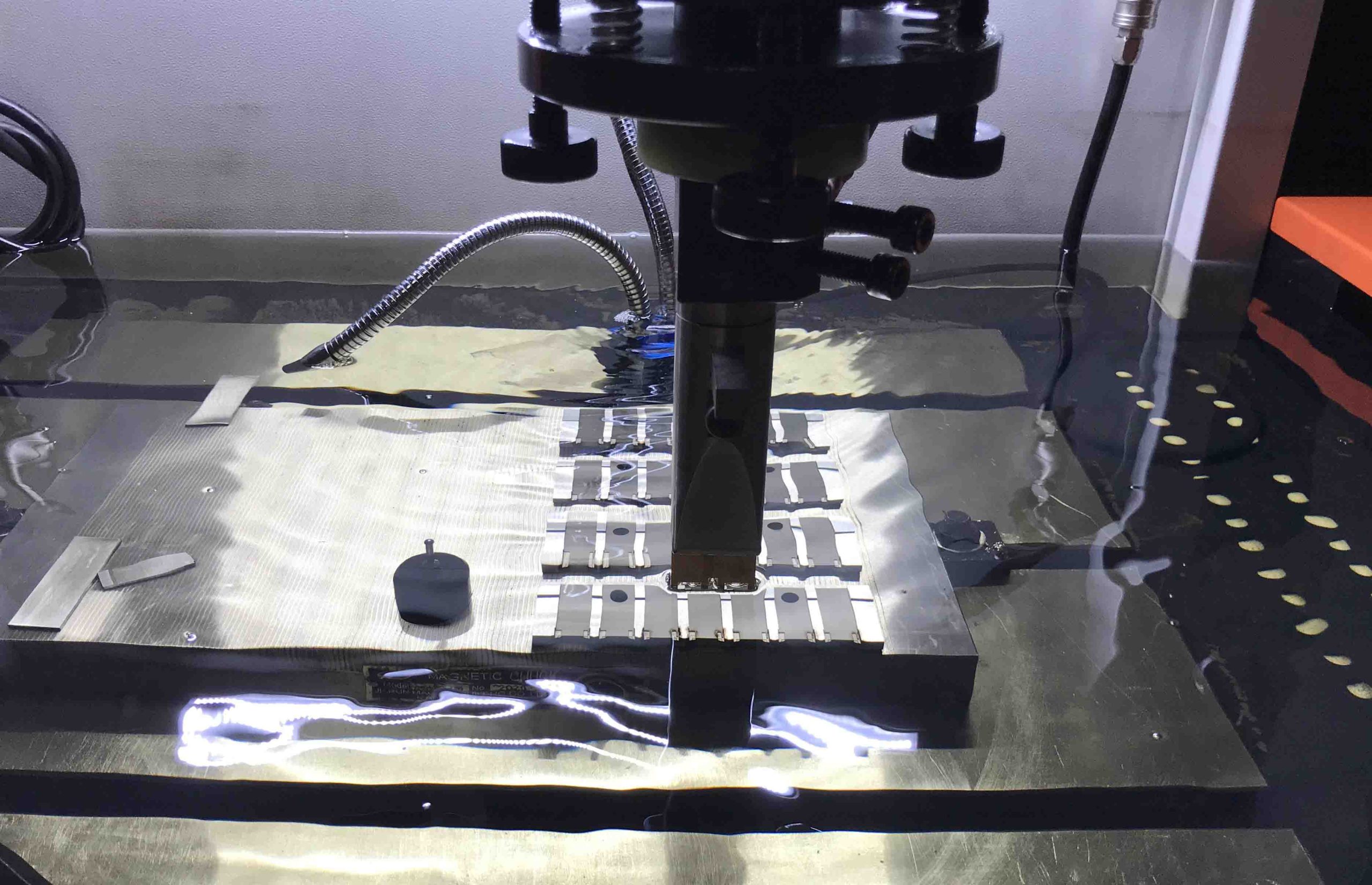
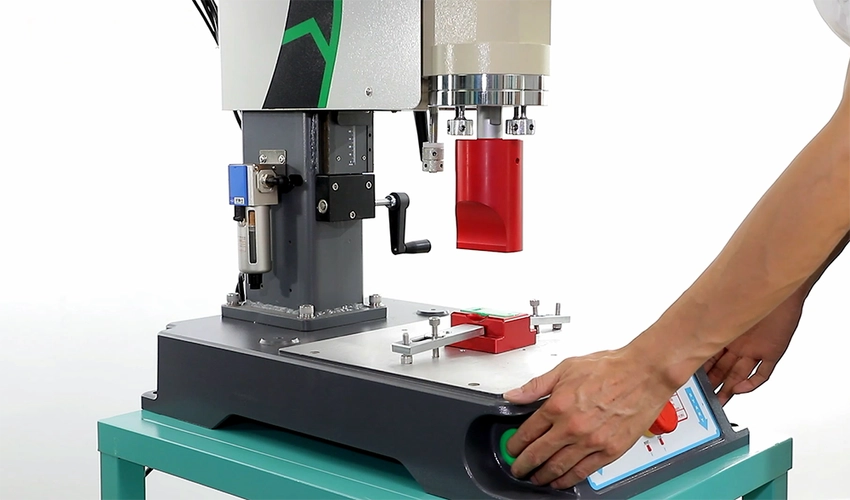
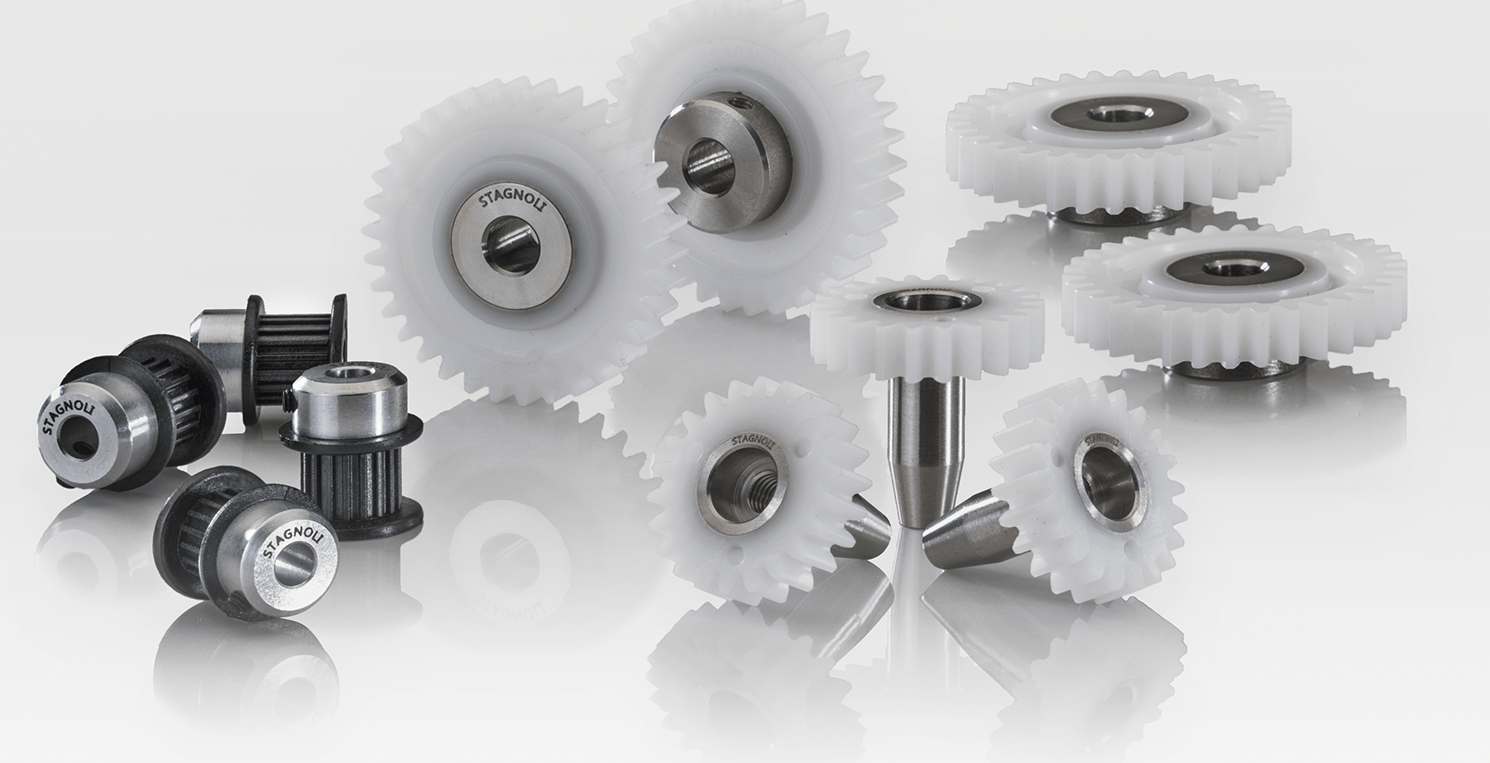
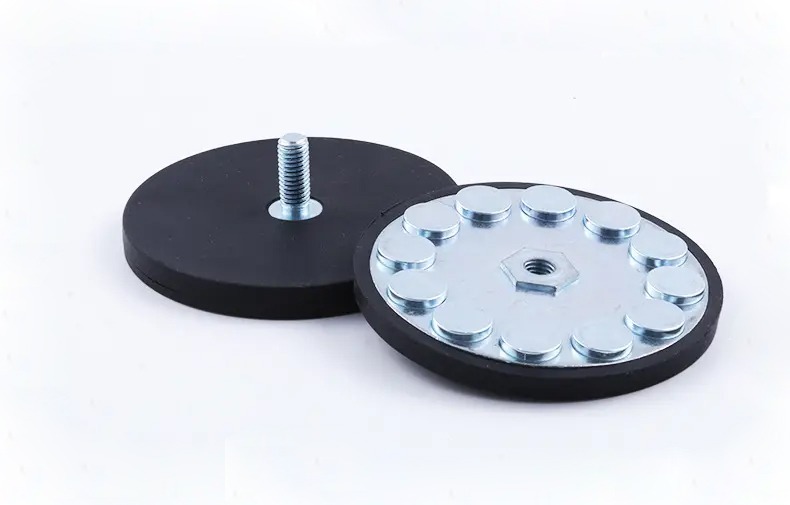
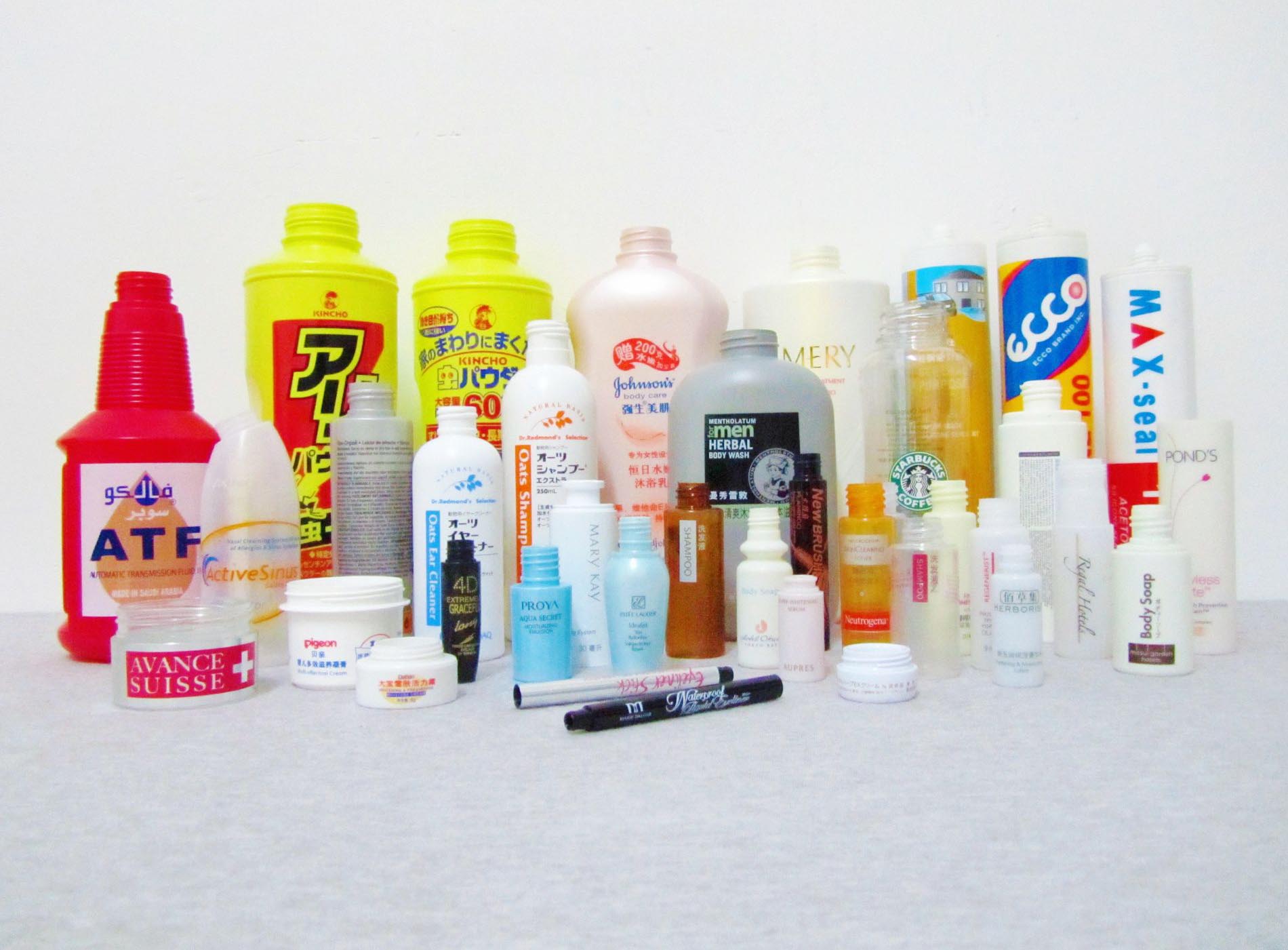
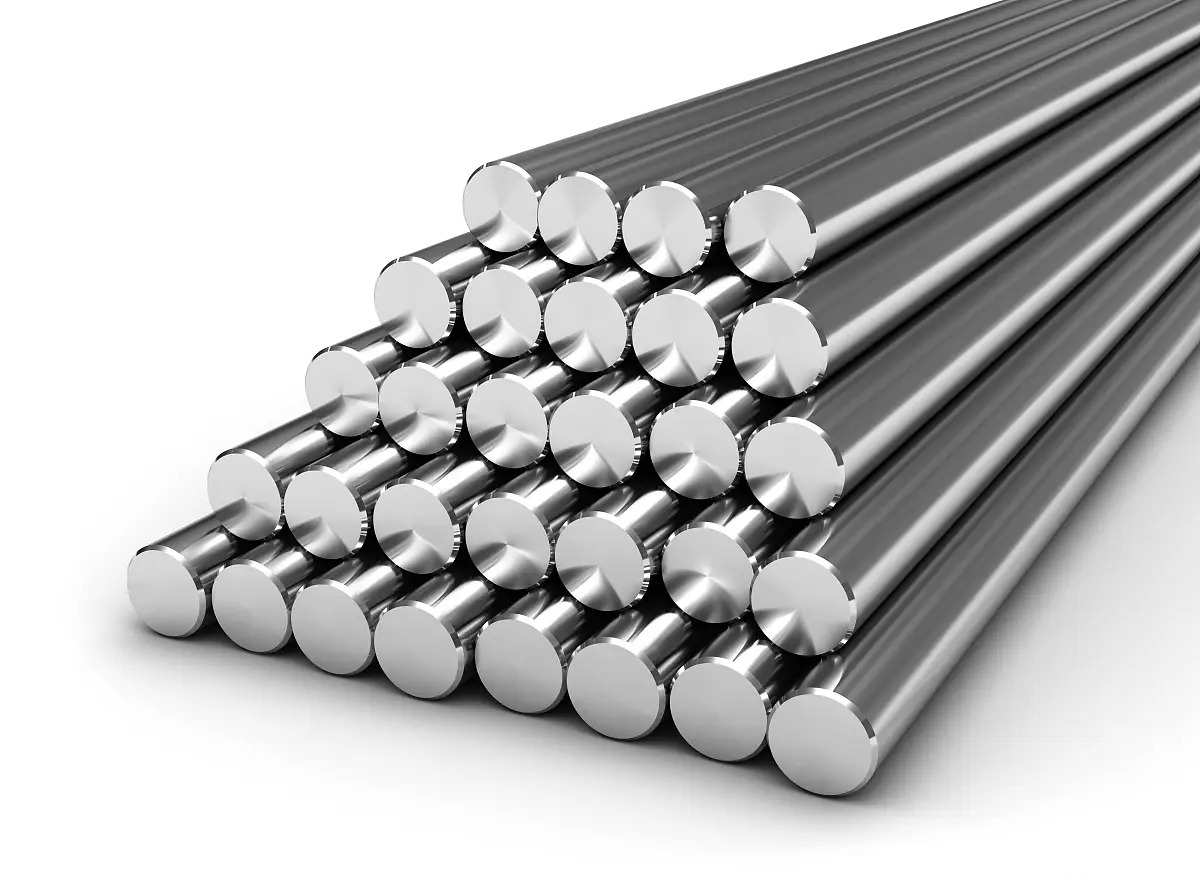
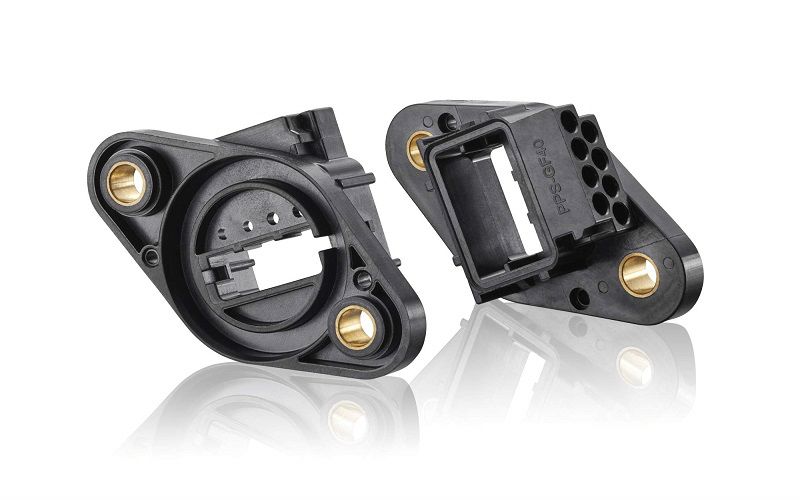
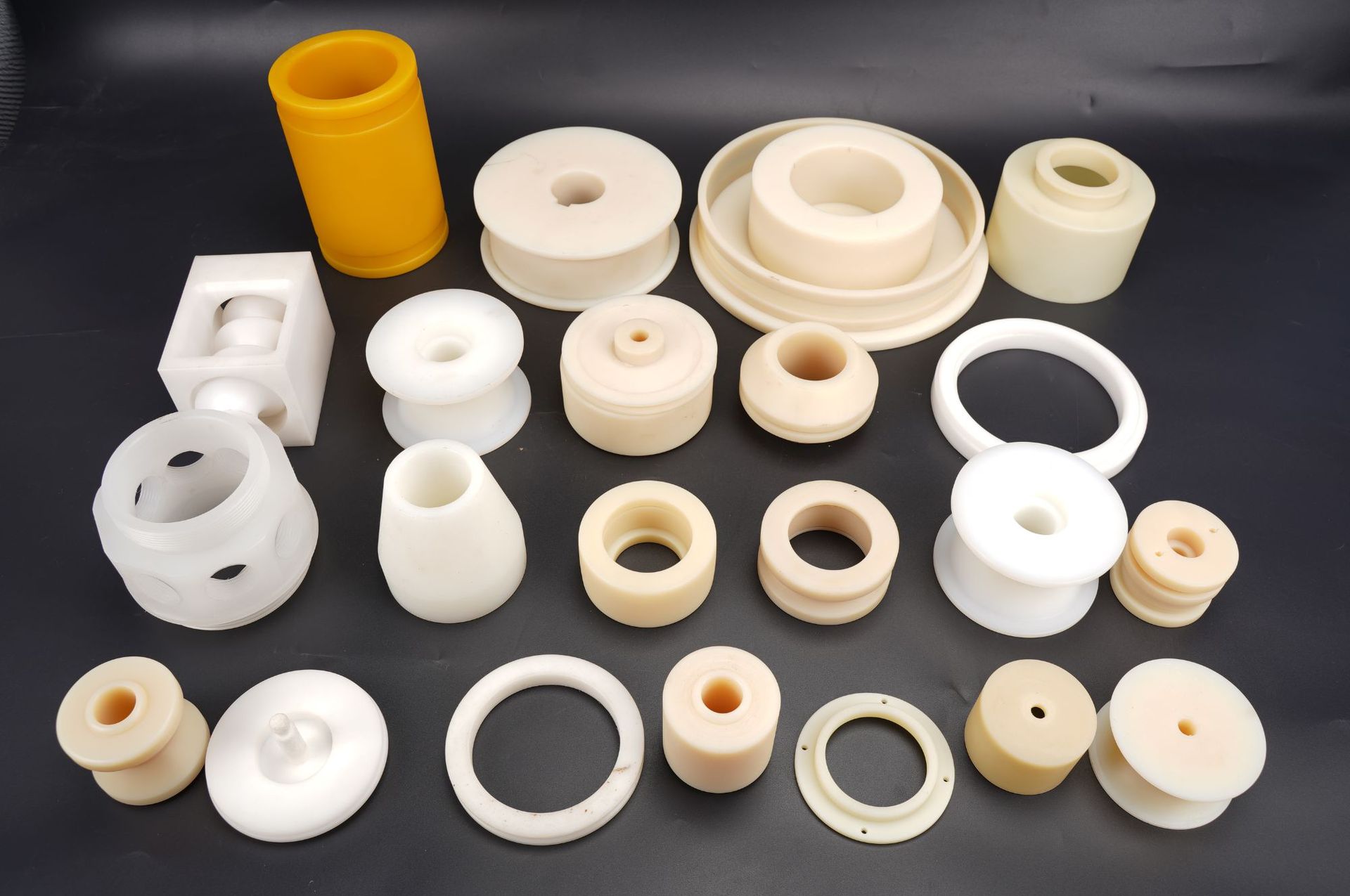
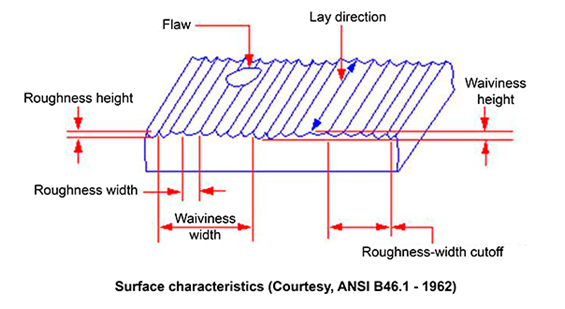
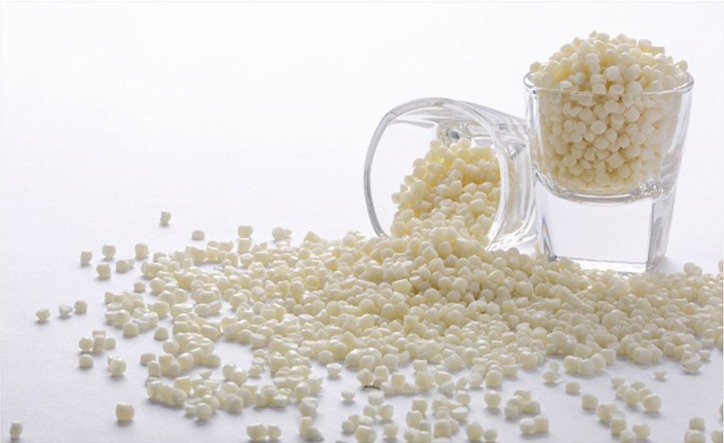
ABS is a cost-effective thermoplastic polymer. Its tough, hard and impact-resistant properties make it a popular plastic material for a variety of indoor and outdoor applications. As an affordable thermoplastic with appropriate mechanical and chemical resistance properties, ABS is well suited for high-volume molding processes.
This article will explore ABS injection molding technology and how it enables the precise, efficient production of a variety of commercial components. Factors such as the various characteristics of ABS, mold design considerations, and molding process parameters will also be discussed.
ABS was first invented in Germany in the 1930s. Bayer AG scientists produced the first ABS resin by blending polybutadiene with styrene and acrylonitrile.
During World War II, ABS production shifted towards military applications due to its toughness, resistance to chemicals and heat, and moldability. It was used in vehicles, tanks, aircraft components and other military gear.
In the 1950s, ABS began being used commercially for non-military applications. Its versatility and moldability made it popular for household appliances, business machines, tools and more.
Major advancements in ABS production technology occurred in the 1960s. New emulsion and bulk polymerization processes improved impact resistance and colorability of ABS. This boosting its use in consumer products.
By the 1970s, ABS had become one of the most commonly used plastics globally. Its tough, economical properties were well-suited for electrical/electronic device housings, automotive trim, pipes and fittings.
Today, ABS is still widely used due to its balance of properties and processability. Common applications include laptops, 3D printer filament, toy Lego pieces, protective gear, water system components and more. Continuous advancements improve ABS performance characteristics.
New bio-based ABS formulations are now being developed to allow for enhanced sustainability as a commodity plastic. Blends incorporating bioplastics are being commercialized.
ABS (acrylonitrile butadiene styrene) is a engineering thermoplastic formed from a terpolymer composition. The unique monomeric structure provides a balanced material property profile, consisting of acrylonitrile which enhances rigidity, butadiene imparting toughness through rubber modification, and styrene controlling processability. This specific acrylonitrile-butadiene-styrene terpolymer formulation yields a plastic with remarkable strength and impact resistance across a wide service temperature range from -20°C to 80°C.
As an engineered material, ABS exhibits superior performance characteristics including corrosion resistance, machinability, and ease of fabrication into complex shapes by various thermoplastic processing methods like injection molding and extrusion. Additional polymer blending and compounding can further refine ABS properties to satisfy diverse application demands. Variants include flame retardant and ultraviolet resistant types through incorporation of specialized additives. These standardized modifications create a versatile engineering plastic able to effectively meet the functional demands of common manufacturing applications.
ABS is mainly composed of three substances: acrylonitrile, butadiene and styrene. Through combining these three monomers in specific compositions, ABS achieves an ideal balance of material properties for numerous manufacturing applications.
In the structure of ABS resin, there are graft copolymers with elastomer as the main chain and graft copolymers with hard ABS resin as the main chain; there are also mixtures of rubber elastomer and hard ABS resin. The elastomer shows the toughness of rubber, and the hard ABS resin shows rigidity. Several varieties are available, such as high impact type, medium impact type, general impact type and special impact type. Different structural compositions can lead to different properties of ABS materials. Specifically, as the content of rubber component B (generally 5% to 30%) increases, the elasticity and impact resistance of the resin will increase; but the tensile strength, Fluidity, weather resistance, etc. will decrease. The increased content of ABS resin AS (generally 70%~95%) can improve the surface gloss, mechanical strength, weather resistance, heat resistance, corrosion resistance, electrical properties, processing performance, etc. of ABS materials. The impact strength will decrease. The proportions of A and B in the ABS resin composition are 30%~35%/80%~65% respectively.
Here is Chemical structure of ABS
By changing the proportions of the three monomers in ABS, ABS with different properties, melting temperatures, and fluidities can be obtained for different uses. In order to increase strength or other properties, glass fiber, carbon fiber, anti-UV agent, antistatic agent, etc. can be added to obtain unique properties.
Therefore, there are many types of ABS with different properties, molding parameters and uses. Common ones include high impact grade, high heat resistance grade, flame retardant grade, reinforced grade, anti-static grade, electroplating grade, transparent grade, etc.
Provides a balance of properties for basic uses. Offers adequate strength, stiffness and impact resistance.
Formulated with higher rubber content for improved toughness and resistance to fracturing. Used in applications requiring durability.
Contains additives like aluminum trihydrate or brominated compounds to self-extinguish and prevent fire spreading. Meets standards for electrical enclosures.
Polished surface appearance with reduced texture. Used in cosmetic trim parts for consumer electronics.
Formulated to prevent degradation from sunlight exposure. Maintains physical properties when used outdoors.
MABS is a kind of transparent ABS, mainly used for parts that require heat resistance or corrosion resistance, such as household appliance casings, industrial components, etc. Its relatively excellent performance brings higher design flexibility to product development. However, the processing difficulty is also relatively increased. Material costs also increase relatively.
PC/ABS is an important engineering plastic alloy widely used in automobiles, electronic and electrical, office and communication equipment and other fields. Nowadays, in order to meet the special requirements for fire safety in application fields (especially electronic and electrical products), the flame retardant technology of PC/ABS alloy has become a hot topic of research.
In engineering, ABS is widely used in engineering pipelines. In municipal projects that have relatively high material requirements, ABS pipelines can generally be used for pool bottom pipelines.
ABS is a commonly used engineering plastic whose price is influenced by multiple factors including raw material costs, market demand, brand influence, production capacity, international market changes and other elements. In April 2024, the price of ABS fluctuated between US$1500 to US$2000 per ton.
ABS plastic manufacturer( 要更新的,可后面更新)
The appearance of ABS is opaque beige particles or translucent particles. Density 1.05~1.18g/cm³, shrinkage 0.4%~0.9%, elastic modulus value 2Gpa, Poisson’s ratio 0.394, moisture absorption rate <1%, melting temperature 217~237℃, thermal decomposition temperature >250℃. It is non-toxic, odorless, has low water absorption, is easy to color, and has a high gloss of 90%. ABS has good bonding with other materials and has good adhesion for surface printing, painting and electroplating. ABS is a flammable polymer with a yellow flame, black smoke, burnt but not dripping, and a special cinnamon smell.
ABS has high impact strength and surface hardness in a relatively wide temperature range, has a higher heat deformation temperature than PA and PVC, and has good dimensional stability.
ABS demonstrates good impact resistance coupled with suitable tensile and flexural rigidity for functional components. Its noticeably high HDT retains structural integrity across a working temperature span. Increased rubber contents in some grades boost toughness furthefurther.ABS plastic has excellent wear resistance,
ABS has excellent mechanical properties, high impact strength, certain low temperature resistance, excellent wear resistance, high dimensional stability, and oil resistance. ABS can be used for bearings under moderate loads and speeds. The creep resistance of ABS is larger than that of PC, but smaller than that of PA and POM. The flexural strength and compressive strength of ABS are among the worst among plastics. The mechanical properties of ABS are greatly affected by temperature.
ABS melt has high viscosity, poor fluidity, and is sensitive to temperature and shear rate. It has poor weather resistance and UV rays can cause it to discolor or break down. ABS operates reliably in temperatures ranging from -30°C to approximately 80°C. Its heat deflection temperature under bending load is typically 95°C. The heat deformation temperature of ABS is 93~118℃, and ABS plastic products can increase by about 10℃ after annealing treatment. ABS can still show a certain degree of toughness at -40°C and can be used in the temperature range of -40~100°C.
ABS plastic has good electrical insulation, is almost unaffected by temperature, humidity and frequency, and can be used in most environments. Electrically, ABS is classified as a moderate insulator with surface resistivity around 10^13 ohms/square. Volume resistivity rates moderately higher at 10^14-10^16 ohm-cm. These traits qualify ABS for many non-conductive components.
In terms of environment, ABS shows good water resistance, oil resistance and solvent resistance, and is almost unaffected by water, inorganic salts, alkali and various acids, but is soluble in ketones, aldehydes and chlorinated hydrocarbons. Stress cracking will occur when corroded by glacial acetic acid, vegetable oil, etc. ABS is sensitive to ultraviolet radiation and is prone to degradation under the action of ultraviolet light. UV stabilizers can be added to ABS to solve the problem of outdoor use.
The following table is a summary of the characteristics of ABS materials:
Property | Value |
Density (g/cm³) | 1.04 – 1.07g/cm³ |
Shrinkage Rate (%) | 0.4 – 0.7% |
Pockwell Hardness | 70-120 |
Tensile Strength at Yield (MPa) | 30-50MPa |
Elongation at Break (%) | 10-50% |
Flexural Modulus (GPa) | 2-2.5GPa |
Flexural Strength (MPa) | 60-80MPa |
Drying Temperature (°C) | 70-90℃ |
Drying Time (hrs) | 2-4Hours |
Melt Temperature (°C) (Mold Temperature) | 200-250℃ |
Mold Temperature (°C) | 40-80℃ |
ABS has high strength combined with toughness to withstand impacts better than acrylic or polycarbonate. This makes it suitable for protective enclosures.
ABS can be easily machined, sawed, drilled, routed and sanded due to its moderate modulus. This allows for secondary processing after molding.
The stiff, durable surface of ABS accepts paints and inks well for coloring or printing decorative patterns and logos.
ABS is resistant to many common chemicals like alcohol, greases and detergents.
ABS resin and production processes are relatively inexpensive, making it a cost-effective plastic for low to medium volume applications.
ABS has good melt flow for molding complex shapes with fine details and is less likely to warp than polystyrene.
Molded ABS components maintain dimensional stability and resist impacts over extended use in various indoor conditions.
ABS has moderately high electrical resistance for use in non-conductive electrical/electronic parts.
Formulations exist to add UV resistance for extended outdoor exposure of ABS without significant degradation.
ABS material has excellent dimensional stability. For plastic parts with size requirements and mass production, ABS is a good choice. Once the mold and process are determined, mass production can be carried out, which is extremely beneficial for cost control. Glass fibers can be added to ABS to further enhance the dimensional stability and performance of ABS plastic.
ABS degrades when exposed to UV radiation and extreme temperatures. This is because the butylphenyl group in ABS is prone to dissociation and chain breakage after absorbing ultraviolet rays, resulting in a decrease in physical properties. This makes ABS unsuitable for outdoor applications that are often exposed to the natural environment.
ABS softens and loses mechanical properties above 80°C, limiting use in high-heat applications.
Prolonged exposure to certain chemicals and solvents can cause ABS to crack over time.
Without additives, ABS is prone to photo degradation when exposed to sunlight over prolonged periods.
If ABS is overheated during processing, it can release hazardous hydrogen cyanide gas. Proper ventilation is required.
Flow patterns from injection molding can sometimes leave visible weld lines in large ABS parts.
Though low, ABS will absorb moisture when exposed to high humidity environments over long periods.
In a fire scenario, ABS may melt and produce thick, black, toxic smoke compared to some engineering thermoplastics.
ABS is prone to warping and shrinking during the cooling process of injection molding. The shrinkage rate per 1mm wall thickness can reach 0.5-0.7%. In order to reduce warpage and shrinkage, careful mold design and injection molding process parameter settings are required.
ABS resin is widely used in the automotive industry, electrical instrument industry and machinery industry. It is often used as gears, auto parts, fenders, handrails, refrigerator linings, blades, bearings, handles, pipes, joints, instrument cases, instrument panels, basins Safety helmet etc. It has broader application prospects in household appliances and household electronic equipment, such as televisions, radios, refrigerators, freezers, washing machines, air conditioners, vacuum cleaners and various small household appliances; daily necessities include shoes, bags, various travel cases, office equipment, Toys and various containers, etc. Low-foaming ABS can replace wood and is suitable for building materials, furniture and household products, etc.
Applications in the automotive field include interior and exterior parts such as automotive dashboards, body exterior panels, interior trim panels, steering wheels, sound insulation panels, door locks, bumpers, air ducts, fenders and grilles.
In terms of electrical appliances, ABS is widely used in refrigerators, televisions, washing machines, air conditioners, and other electronic appliances.
File trays, inbox/outbox bins, document holders and storage containers where ABS provides durable and affordable options. Desktop accessories like phone/gadget holders, paper/business card trays utilizing ABS’s ability to take ink/finishes well.
Protective gear like helmets, shin/elbow guards, bats/racquets, grip tape benefiting from ABS’s impact/cut resistance. Interior fittings for bikes/racquets/clubs like handles, buttons, covers that require durability.
ABS is widely used in the consumer goods industry. Typical products include LegoⓇ building blocks, toys, kitchenware, bags, etc.
Power tools housings, guards, accessories that withstand impacts/vibrations from use while being affordable to integrate
Quality control is an important step in ABS injection molding, through various methods to ensure that the final product meets the required specifications. The following are some quality control methods for ABS injection molding based on our experience:
Before starting the injection molding process, computer simulation is used to analyze material properties, thermal deformation, rheology, etc., and the design of the part is evaluated and verified to confirm whether it meets the requirements. Such as wall thickness uniformity and manufacturing feasibility.
Select appropriate ABS raw materials according to the use environment and appearance performance requirements of the parts, such as toughness.
Mechanical performance testing is performed on samples and finished products to ensure that they meet customers’ unique requirements, such as mechanical strength, toughness, weather resistance, etc.
The ABS plastic resin used for production must be consistent with the sample material. Because incoming material inspection must be carried out before production to ensure that the raw materials meet the requirements.
Mold design is crucial to ensure the quality of the finished product. Mold flow software can be used for analysis to prevent various injection molding defects as early as possible. At the same time, many years of experience are used to optimize the mold design plan to ensure the high quality of the final product.
Every detail of the injection molding process affects quality. Therefore, the quality department should closely monitor production, including real-time monitoring of injection molding process parameters, inspections within a fixed period, etc. At the same time, any deviation should be reported to the production supervisor to reduce losses as much as possible.
Final inspection of finished plastic parts can ensure that the products received by customers are qualified. This is also an essential step in ABS injection molding production.
Apply barcodes and centralized recording systems to track single-piece quality performance, analyze abnormal causes and monitor improvement effects.
Any processes and operations involved in the injection molding process should be recorded and traceable to ensure that quality is maintained and quality problems can be identified and corrected if they occur.
Injection molding manufacturers should establish a clear quality function structure and standard operating procedures, implement personnel training and internal audits to continuously improve quality levels
ABS is a very cost-effective plastic material. Its high strength and durability, high chemical resistance, high thermal stability, good flexibility and impact resistance make it a favorite of manufacturers and engineers.
Plastic products made of ABS material can have good functions and beautiful appearance. ABS injection molding is available in more than 100 surface finishes. Usually no post-molding or polishing is required. This is also one of the plus points to improve competitiveness.
ABS is extremely easy to color and has a wide range of colors. By mixing ABS with colorants, ABS plastic parts of various colors and high-quality surface effects can be achieved. The most typical one is the variety of colors of LegoⓇ building blocks.
ABS automated injection molding can amortize mold costs. On-site recycled sprues/runners produce minimal waste. Mold life is long, exceeding millions of cycles. Fully automated robotic processes require less labor. The reduction in labor costs is ultimately amortized into a lower cost per part.
ABS injection molding produces less solid waste. The waste produced mainly comes from the runner and gate parts, and these materials can be recycled and reused. Recycled waste materials can be directly added to raw materials for reuse without additional processing and almost no substantial waste is generated. This also protects the environment.
Injection molding can produce a variety of plastic parts with complex structures, including metal insert molding or overmolding. By slider and lifter, various complex structures such as undercuts can be produced.
High Tooling Costs and long Mold Making Lead Times
Molds for ABS parts require steel molds, which can be an expensive capital investment, which increases the initial investment cost. In addition, the cost of modification is also higher than other processes such as 3D printing and CNC machining.
The general production cycle of injection molds is 25-35 days. This production cycle is difficult to accept for urgent projects. But compared to CNC, 3D printing can be completed in a few days, which is also one of the main disadvantages of injection molding.
Undercuts, thin walls, and other complex geometries require fabrication of structures such as sliders, which increases the complexity of the mold and increases the challenge.
Due to the narrow processing window of ABS materials, weld lines and warping are easily seen during the molding process. Defects such as shrinkage affect the appearance and function of the product.
At the junction of thickness and thickness of plastic parts, internal stress marks are very easy to occur. If pin gate is used, rupture due to excessive shearing force is also easy to occur.
Injection molding is an asset-heavy industry. robots, injection molding machines, auxiliary equipment and facilities are major upfront investments. This is a significant investment.
Internal stresses built up during orientation of the molecular structure and cooling can cause cracking, usually at locations of concentrated stress such as thick sections, weld lines or sharp corners. Relieving weld lines, designing draft angles and radii, and using a stiff mold materials help reduce stresses.
Prolonged exposure of ABS melt to temperatures above 220°C can cause chemical breakdown of the polymer chains throughunzipping. This degrades mechanical properties of the finished part. Short shotting may also occur due to melt degradation.
Generally, there is a central axis, or two or more injection gate. The two sides are filled first, and a line is formed at the intersection of the center, which we call weld line.
Causes:
Solutions:
Jetting is a pattern of wavy lines on the surface of the plastic part extending from the gate. During ABS injection molding, this occurs when the ABS can’t flow according to the contours of the mold, but instead enters the mold cavity as a direct flow.
Causes:
Solutions:
No venting system, or too little venting hole, or the venting groove is too shallow so that the air in the cavity can’t be exhausted, causing the raw material to burn brown or black.
Causes:
Solutions:
Low quality ABS, impurities like sprue/recycled materials cause.
Causes:
Solutions:
Shrinkage and Sink marks are depressions or dents that appear on the surface of a plastic product. This phenomenon usually occurs when the surface of the plastic part cools faster than the interior.
Causes:
Solutions:
During the injection molding process, the melt volume injected is insufficient and the entire cavity is not completely filled, resulting in incomplete parts.
Causes:
Solutions:
When plastic products are ejected and separated from the mold, due to poor positioning and balancing capabilities of the ejection system or problems with the mold itself, marks lines left by non-uniform pressure appear on the surface of the product.
Causes:
Solutions:
Injection molding flash refer to small, thin plastic protrusions that appear on the surface edges of plastic products.
Causes:
Solutions:
Due to different shrinkage rates, the external geometric shape of the plastic part is distorted and deformed.
Causes:
Solution:
Injection mold sticking means that during the injection molding process, it is difficult for the ABS plastic to be peeled off from the mold surface in time after solidification. This situation mostly occurs in pre-production molds.
Causes:
Solutions:
Drying treatment: ABS has different compositions, and its water absorption and adhesion properties are also different. Its water absorption rate is generally between 0.2~0.5% and sometimes can reach 0.3~0.8%. In order to obtain a more ideal product, before molding It must be dried to reduce the moisture content to less than 0.1%. Otherwise, bubbles, silver wires and other defects will appear on the surface of the product. Normally, it needs to be dried at 80~85℃ for 2~4 hours. Usually, recycled materials are controlled within 30% and no more than 50% at most. However, it is recommended not to add any recycled materials to electroplating grade ABS materials, otherwise poor plating will occur.
For heat-resistant ABS (PC/ABS alloy plastic) containing PC components, the drying temperature is generally 100°C. Drying time is 2-4 hours. It is recommended that the proportion of recycled materials does not exceed 30%.
ABS coloring treatment: ABS material has good coloring ability. By adding pigments or color masterbatch and mixing it evenly with ABS, various imaginable colors can be obtained.
The melting point of ABS is 200-280℃; the melting point of different grades is slightly different. The following is the recommended optimal injection molding temperature for different grades of ABS:
Impact resistance level: 220℃-260℃, 250℃ is better
Electroplating grade: 250℃-275℃, 270℃ is better
Heat resistance grade: 240℃-280℃, 265℃-270℃ is better
Flame retardant grade: 200℃-240℃, 220℃-230℃ is better
Transparency level: 230℃-260℃, 245℃ is better
Glass fiber reinforced grade: 230℃-270℃ For products with high surface requirements, use higher melt temperature and mold temperature.
ABS melt viscosity is relatively high, and the pressure of ABS plastic injection molding is relatively high. Excessive injection pressure may also cause the molded part to be too strong and stick in the mold. Pressure that is too low may result in increased molding shrinkage, resulting in large shrinkage of the part. Medium injection pressures of 3000-5000 psi are generally used for ABS molding. Higher pressures are needed for complex parts.
ABS products with thin walls, long processes and small gates require higher injection pressures, up to 130~150MPa, while products with thick walls and large gates only require 100MPa. In the actual production process, the injection pressure often used for screw injection machines is below 100MPa (we use 50~70MPa), while the injection pressure for plunger injection machines is generally above 100MPa. The holding pressure should not be too high. Screw-type injection machines generally use 30~50MPa, while plunger-type injection machines require more than 60~70MPa. If the holding pressure is too high, the internal stress of the product will increase.
Injection speed is extremely important to ensure the appearance of plastic products. But injection speeds that are too high can cause plastic materials to burn or thermally decompose. However, if the speed is too slow, insufficient mold filling will occur. Therefore, speed and pressure need to be balanced to obtain high-quality plastic parts. For example, the injection molding speed of flame-retardant grade ABS should be slow, and the injection molding speed of heat-resistant grade ABS should be fast. If the ABS product surface requirements are high, high-speed, multi-stage injection should be used to control it.
ABS cools and solidifies rapidly due to its high heat deflection temperature. Parts are typically cooled within 10-30 seconds.
ABS exhibits low shrinkage rates of 0.5-1% during cooling and subsequent crystallization. Proper venting can minimize warping.
The mold plays a key role in the successful production of ABS plastic parts injection molding. Therefore, gate design, product layout and other mold designs need to be cautious. Usually the gate thickness range of ABS molds is 0.025-0.05mm, the gate width is about 3mm, and the gate length is generally less than 1mm. In addition, the diameter of the ABS mold runner is generally 6-8mm, and the width of the exhaust hole is 4-6mm.
Generally, the lower the back pressure, the better. A common back pressure is 5 bar. For ABS plastic parts that need to be colored, in order to make the color mix more evenly, a higher back pressure is usually required.
Dwell time is the time it takes for plastic particles to move from the injection molding barrel to the injection mold. Below 265°C, the residence time of ABS in the melt in the cylinder should not exceed 5-6 minutes at most. The melt residence time of flame retardant ABS should be shorter. If the machine needs to be shut down, the set temperature should be lowered to 100°C first, and then the melt barrel should be cleaned with general-grade ABS.
ABS is easy to machine, drill, glue and paint after molding. Secondary operations improve surface aesthetics. You can also perform various textures or polishing treatments on the mold surface to obtain more surface finishes. Such as SPI, VDI3400, sandblasting, etc.
ABS can be ultrasonically or vibration welded for joining. Heated tool welding is also used during assembly.
ABS injection molded products can undergo various post-molding processes to improve appearance and competitiveness. Such as electroplating, spray painting, silk screen, pad printing, heat transfer printing, ultrasonic welding etc. Note: Electroplated plastic products do not need to use a release agent. At the same time, the product should be packaged immediately after being demoulded to prevent static electricity from adsorbing and affecting the electroplating results.
All ABS plastic parts follow standard injection molding design guidelines. Before injection molding ABS plastic, you need to make some preparations to minimize injection molding defects and limit potential processing challenges. Attractive Plastics’ injection molding experts can help you with this process. The following guidelines will ensure successful molding and expected results, and you can keep them as a reference:
There are also some specific design considerations with ABS plastic:
When designing the wall thickness of ABS plastic products, attention should be paid to the uniformity of the wall thickness, and the difference should not be too large. If there is uneven thickness, a slope or arc should be added for transition. When designing ABS parts, keep the wall thickness of the ABS plastic part between 0.045 to 0.140” (1.14 to 3.56 mm).
The wall thickness of the product is related to the flow length of the melt, production efficiency, and usage requirements. The ratio of the maximum flow length of ABS melt to the wall thickness of the product is approximately 190:1, and this value will vary depending on the grade.
The existence of sharp corners should be avoided in ABS injection molding to prevent stress concentration from causing cracks, and rounded corners should be used for transition. Keep the minimum radius equal to 25% of the wall thickness. For maximum strength, use a radius equal to 60% of the wall thickness.
In ABS injection molding, the thickness of the ribs should not be too large or too small, generally between 0.5-3mm. Too thin affects the flow. The draft angle of the ribs should be controlled at 15-30 degrees to avoid poor plastic flow or stretch deformation. The spacing between ribs is generally set to 2-4 times the wall thickness to ensure structural strength and reduce reduction stress.
Bosses are generally round or oval and easy to molding. The diameter is designed according to the required load-bearing size, and is generally not less than 2-3 times the wall thickness. The thickness is similar to the wall, and the spacing is based on strength requirements, generally 2-5 times the wall thickness to avoid stress concentration.
Add generous radii wherever possible. Consider rib/wall thickness changes, locational gates to minimize stresses.
Melt temperature is a key consideration in ABS injection molding because of its relationship to viscosity, a measure of a fluid’s resistance to flow. The higher the temperature, the better the melt fluidity. At the same time, the higher the temperature, the shorter the time the plastic is exposed to such temperatures to prevent degradation, and too high molding temperatures can lead to thermal decomposition. When injection molding ABS parts with high gloss, the molding temperature needs to be higher and ensure that the physical properties of the material are not damaged during the molding process.
The ABS injection mold temperature is generally set at 60-80°C, and the maximum temperature generally does not exceed 120°C. Note that the higher the mold temperature, the longer the molding cycle of the plastic part.
ABS melt cools quickly, and the mold pouring system should be thick and short to reduce mold pressure loss. The runner diameter should be no less than 5mm. According to experience, the cone angle of the main flow channel is 20~40°. The minimum diameter of the main flow channel should be 0.5mm~1mm larger than the nozzle hole. The general diameter of the flow channel is 6-8mm.
At the same time, a cold material cavity should be set up, and the gate should be large, such as direct gate, fan gate, etc. Try not to choose point gates, which are prone to shear stress. The gate width is usually about 1-3mm, the gate thickness should be greater than 30% of the product thickness, and the length of the flat part (the part that will enter the cavity) should be about 1mm.
The location of the gate should be determined according to the requirements of the product and the direction of material flow. According to experience, the pouring material of the ABS injection mold should be in an S shape to prevent injection defects such as spraying. At the same time, the pouring place should not directly face the mold cavity as much as possible.
ABS injection molding has a certain impact on the mold. It is generally recommended to use mold temperature heating and wear-resistant steel should be used.
The draft of injection molded plastic parts is directly related to its material shrinkage, surface roughness and product shape. The shrinkage rate of ABS is generally 0.3~0.6%, and sometimes it can reach 0.4~0.8%. In actual production, the appropriate draft angle should be selected according to the shape of the product, the thickness of the surface texture, and the thickness. For products with complex shapes or letters or patterns, the draft angle should be appropriately increased. Like other injection molded plastics, ABS plastic injection molded parts require a draft angle of 0.5 to 3° to ensure that the part can be easily ejected from the mold without damage.
Side or bottom plate ejectors used. Common slider pins or segmented movable mold structures for easy part removal. Ejector pins located away from stress-prone areas. Multiple ejector pins can be used to achieve better synchronization during the ejection process and even ejection force.
In order to prevent poor exhaust during the plastic filling process, resulting in melt burning and obvious weld lines. Vent holes or vent grooves can be opened in the mold, with a depth of generally 0.04mm, to facilitate the discharge of gas generated by the melt. The venting hole width is 4-6mm
In ABS injection molding, there are many factors that affect the cost of ABS injection molding. Optimizing these factors that affect cost can help you obtain high-quality plastic parts while also making your injection molding project cost-effective.
If you are using ABS injection molding to produce your unique plastic parts, it is necessary to understand the cost of the entire process before starting the project. ABS injection molding cost estimation involves the following considerations.
Material cost is the most basic cost of ABS injection molding. Depending on market fluctuations and material grade, the cost of ABS per kilogram ranges from US$2 and upwards. Cost may vary depending on grade of material and quantity purchased. Buying in bulk usually reduces the unit price, but the initial outlay may be higher.
The mold is the main investment and the main cost input of any injection molding project, so it needs to be treated with caution. Depending on the product requirements, the mold cost is also different, ranging from 1,000 US dollars to hundreds of thousands of US dollars. For batches of plastic parts, the mold cost will be gradually shared through the increase in later production quantities. This is also the main reason why many major projects choose the injection molding process.
The rapid production speed directly determines whether the project can be competitive. Faster production speed means more parts can be produced per hour, which can reduce the cost per part. Of course, this is without affecting the quality of the parts.
Skilled workers can increase the output of the injection molding process without affecting the quality of the plastic parts. For industries in countries with high labor costs, optimizing labor costs is the main way to improve competitiveness. In the future, automation will be the main direction to replace labor costs.
If you plan to purchase new machinery and equipment for a project, this is a significant cost, and part of these costs must be allocated to your project costs. So in the cost analysis, this is also part of the cost.
Maintenance costs include repair costs for defective parts, repair costs for machinery and equipment, repair of molds, etc.
We offer custom injection molding of a variety of thermoplastic materials. ABS has become a popular material in many industries due to its extremely high versatility, good machinability and moderate heat resistance. Used in a wide range of industries such as automotive, electricals shell, sports equipment and medical equipment.
ABS is one of the most commonly used and popular injection molding plastics. Because it is easy to obtain, has good comprehensive properties, is cheap, and has a wide range of uses, this is why it is used in many areas of life.
ABS injection molding is a process that seems easy to implement. However, there are many techniques and techniques that only experts understand. This is why many customers outsource ABS molding to companies that truly understand the physical properties of ABS raw materials and manufacturing processes, and have practical experience to produce corresponding products.