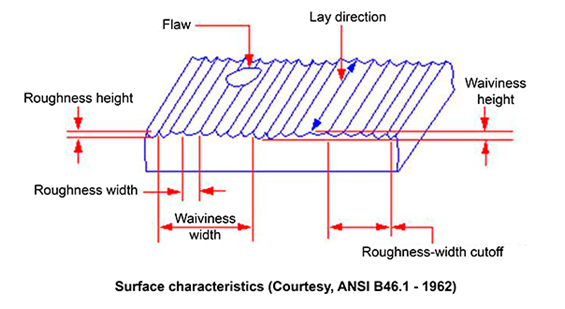
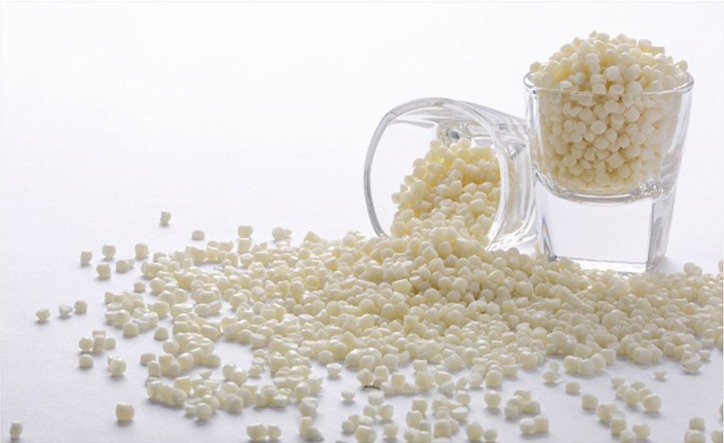
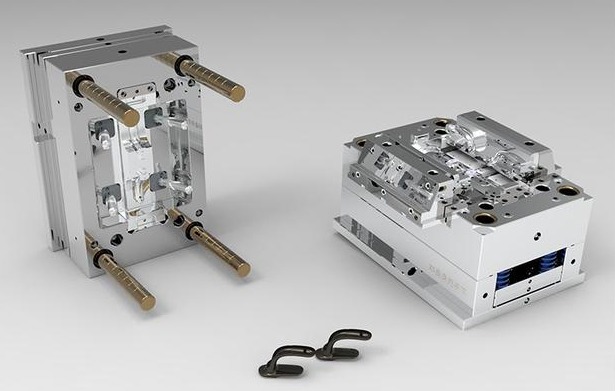
PEEK is a unique polymer that exhibits impressive heat, electrical resistance and corrosion resistance. In addition to its exceptional durability, PEEK is lightweight and easy to process, making it ideal for the manufacture of complex, high temperature plastic parts. In precision production environments, PEEK ensures accurate and consistent production runs, even with tight tolerances.
When your team is considering using PEEK as a material for your plastic parts, in-depth research is required to determine its suitability. However, working with a trusted injection molding manufacturer can greatly simplify this decision-making process.
This article will introduce all aspects of PEEK in detail, including its types, applications, design, and precautions when using it. We hope this information will help you gain a more complete understanding of this high-performance material.
The history of PEEK (polyetheretherketone) can be traced back to 1977, when John B. Rose/Philip A. Staniland of Imperial Chemical Industries (ICI) successfully developed this material. In 1978, they applied for a patent for PEEK resin and began small-scale production the same year.
In 1981, ICI officially launched commercial PEEK resin under the trademark Victrex. With the wide application of PEEK in Western military and industrial fields, the market scale gradually expanded. In 1993, ICI sold its PEEK polymer business to Victrex, which began independent operation.
Subsequently, PEEK resin has been widely used globally. In 1999, Victrex expanded its production capacity worldwide to 2000 tons per year, and again to 2800 tons per year in 2005. At the same time, the market scale of PEEK resin has been continuously growing.
In China, PEEK has been listed as a national key project since the “Seventh Five-Year Plan”. In 2000, Changchun Jilin University High-tech Materials Co., Ltd. established a production line with a capacity of 500 tons per year and started production. In 2005, Evonik Industries AG invested to establish Jilin Jida Yingchuang High-performance Polymers Co., Ltd., which cooperated with Victrex to build and operate a new PEEK polymer production base in Liaoning Province, China.
PEEK (polyetheretherketone) is a high-performance engineering thermoplastic that belongs to the polyaryletherketone family. Its molecular main chain contains linear aromatic polymer compounds with the following links. It is a semi-crystalline, thermoplastic special engineering plastic with excellent comprehensive properties such as high temperature resistance, self-lubrication, corrosion resistance, flame retardancy, hydrolysis resistance, wear resistance and fatigue resistance. It was initially used in the field of national defense and military industry, and then gradually expanded to the civilian field, including industrial manufacturing, aerospace, automobile industry, electronic and electrical and medical equipment. With the continuous improvement of PEEK synthesis and processing technology, its application fields have been broadened by high-performance materials obtained through chemical modification, blending, composite filling, etc.
PEEK processing technology includes injection molding, extrusion molding, CNC processing and other processing methods. In recent years, the combination of PEEK resin with advanced manufacturing technologies such as 3D printing has given it new applications in medical fields such as medical implants. development direction.
Pure, unfilled PEEK itself is very abrasive, but in order to improve its performance, carbon fiber or glass fiber is often added to PEEK to enhance its mechanical properties. Glass fiber-filled PEEK has higher stiffness than unfilled PEEK and is often used in the oil and gas industry to meet applications in special environments such as steam, chemicals and high temperatures.
Glass fiber-filled PEEK plastic parts have high strength, but the disadvantage is that they are prone to wear and tear of matching parts. Carbon fiber-filled PEEK increases the compressive strength of PEEK parts, greatly reduces their expansion rate, and supports better wear resistance and load-bearing capacity. Carbon fiber-filled PEEK plastic products also have higher thermal conductivity, extending the service life and mechanical properties of parts.
As shown in the figure below, there are many polymers in the polyaryl ether ketone (PAEK) family, among which polyether ether ketone (PEEK) is the most widely used and has the largest production scale:
PEEK (polyetheretherketone) is a linear polymer composed of ether, ketone and phenyl groups. These repeating structural units give PEEK excellent chemical stability. The units, called benzene rings, are made up of six carbon atoms and six hydrogen atoms and take on the shape of a planar hexagon.
The main chain of PEEK is composed of carbon and oxygen atoms arranged alternately. Each carbon atom is connected to two benzene rings and forms chemical bonds with adjacent carbon atoms and oxygen atoms. This structure makes PEEK molecules highly rigid and heat-resistant.
The side chains of PEEK refer to additional atoms or groups attached to the main chain. The type and location of these side chains play an important role in the properties and uses of PEEK. For example, if the side chain contains fluorine atoms, it can increase the chemical corrosion resistance and wear resistance of PEEK. if the side chain contains acid or alkali groups, it can make PEEK more biocompatible.
The molecular structure of PEEK is shown below:
Let’s explore its characteristics to better help you understand the performance of PEEK plastic. The main Properties of PEEK plastic include:
PEEK material has excellent high temperature resistance and can maintain stable performance in high temperature environments. It can withstand short-term operating temperatures up to 300°C and high temperatures of 250°C for continuous use. This means that in high-temperature environments, such as during manufacturing or use, PEEK materials are able to maintain their physical and chemical properties without deformation or decomposition. This is very beneficial for applications that require working in high temperature environments for long periods of time. This is one of the main reasons why PEEK materials are often used to replace metal parts.
PEEK material has high strength and hardness, which allows it to withstand greater pressure and wear. In applications that need to withstand greater stress, such as mechanical parts, wear-resistant parts, etc., PEEK materials can provide excellent mechanical properties. At the same time, its hardness also makes it excellent in applications that require wear resistance.
PEEK material is very resistant to most chemicals. This means that in applications that come into contact with chemical substances, such as chemical equipment, pharmaceutical equipment, etc., PEEK materials can resist the erosion of chemical substances and maintain stable performance.
PEEK material has excellent wear resistance and can resist friction and wear. In applications that need to withstand friction, such as bearings, gears, etc., PEEK materials can provide excellent wear resistance and extend the service life of the equipment.
PEEK material is self-extinguishing and can resist the spread of flames. This means that in applications that require fire protection, such as electronic equipment, automotive parts, etc., PEEK materials can provide good flame retardant properties and reduce the risk of fire.
PEEK material has good electrical insulation properties and can resist electric shock and sparks. In applications that require insulation, such as electronic components, power equipment, etc., PEEK materials can provide excellent electrical insulation properties to ensure the safe operation of equipment.
PEEK material has excellent fatigue resistance and can resist repeated stress changes and fatigue fracture. In applications that need to withstand fatigue stress, such as springs, bearings, etc., PEEK materials can provide good fatigue resistance and extend the service life of the equipment.
PEEK material can resist high-energy radiation and has good radiation resistance. In applications that need to withstand radiation, such as the nuclear industry, medical equipment, etc., PEEK materials can provide good radiation resistance to ensure the normal operation of the equipment.
PEEK material has good compatibility with biological tissues. In the field of medical devices, PEEK materials are compatible with human tissues and will not cause adverse reactions. This makes PEEK materials widely used in the field of medical devices.
PEEK material has excellent self-lubricating properties, which means it can reduce friction and wear with other materials without additional lubricants. Especially those applications that require reducing friction and wear to improve efficiency and durability. This feature makes PEEK excellent in the field of bearings and has a wide range of applications.
PEEK material has good processing properties and can be processed through injection molding, extrusion, compression molding, and other processes. This allows PEEK materials to be easily processed and shaped during production. At the same time, its processing properties also enable PEEK materials to meet the needs of various complex shapes and applications.
Unparalleled chemical inertness, FDA compliance, and strength up to 300°F. Its excellent machinability and cleanliness make it an ideal choice among all ketone-based polymers for manufacturing complex machine parts to tight tolerances or injection molded parts such as gears, ferrules, and life sciences and medical parts.
Has the highest strength and stiffness among PEEK grades. It is 7% lighter than glass-reinforced grades despite containing more reinforcement material per unit volume. It is an excellent choice for high-duty machined or molded parts.
Provides greater strength and stiffness than unfilled PEEK grades, but has excellent electrical and thermal insulation properties. It is an excellent choice for high-load machined or molded parts including replacement seals and electrical connector bodies.
Has the lowest wear rate among PEEK grades and is suitable for demanding wear applications. The most common grades contain a combination of graphite, PTFE and carbon fiber, with the most common ratio being a 10-10-10 mix. This combination promotes low friction and higher conductivity, resulting in higher PV and lower wear rates.
Properties of unfilled vs. filled PEEK grades | |||
Property | Unfilled PEEK | PEEK+30% carbon fiber | PEEK+30% glass fiber |
Dielectric Constant | 3.2 | 3.2-3.4 | 3.3-4.2 |
Dielectric Strength (kV/mm) | 20 | 18.5-19.0 | 15-24 |
Volume Resistivity (x 1015 Ohm.cm) | 16-17 | 1.0-8.0 | 15-16 |
Elongation at Break (%) | 30-150 | 1.0-3.0 | 2.0-3.0 |
Flexibility or Flexural Modulus (GPa) | 3.7-4.0 | 13-19 | 9.0-10.0 |
Young Modulus (GPa) | 3.5-3.9 | 13-22.3 | 9.0-11.4 |
Toughness or Notched Izod Impact at Room Temperature (J/m) | 80-94 | 85-120 | 95-130 |
Density (g/cm³) | 1.26-1.32 | 1.4-1.44 | 1.49-1.54 |
Thermal Insulation or Thermal Conductivity (W/m.K) | 0.25 | 0.9-0.95 | 0.43 |
PEEK 450 G unfilled does not contain glass fiber or carbon fiber
PEEK 90GL30 GF 30% is filled with 30% glass fiber
PEEK 450CA30 CF 30% is filled with 30% carbon fiber
PEEK 150G903 is unfilled, but is pigmented so that the color is black
Material Properties of Common PEEK Grades | |||||
ITEM | PEEK 450 G Unfilled | PEEK 90GL30 GF30% | PEEK 450CA30CF30% | PEEK 150G903Black | |
Physical | Density (g/cm³) | 1.3 | 1.52 | 1.4 | 1.3 |
Shrinkage Rate (%) | 1-1.3 | 0.3-0.9 | 0.1-0.5 | 1-1.3 | |
Shore Hardness (D) | 84.5 | 87 | 87.5 | 84.5 | |
Mechanical | Tensile Strength (MPa) | 98 @ Yield | 195 @ Break | 265 @ Break | 105 @ Yield |
Elongation (%) | 45 | 2.4 | 1.7 | 20 | |
Flexural Modulus (GPa) | 3.8 | 11.5 | 24 | 3.9 | |
Flexural Strength (MPa) | 165 | 290 | 380 | 175 | |
Injection Molding | Drying Temperature (°C) | 150 | 150 | 150 | 150 |
Drying Time (hrs) | 3 | 3 | 3 | 3 | |
Melt Temperature (°C) | 343 | 343 | 343 | 343 | |
Mold Temperature (°C) | 170-200 | 170-200 | 180-210 | 160-200 |
The mechanical specifications of PEEK are important indicators for evaluating its performance and application. The mechanical specifications of PEEK mainly include its mechanical performance parameters, such as elastic modulus, yield strength, elongation and hardness. These parameters can be used to evaluate the mechanical properties and behavior of PEEK materials, which is of great significance for the design, selection and application of materials.
Mainly include its mechanical performance parameters, such as elastic modulus, yield strength, elongation and hardness, etc. These parameters can be used to evaluate the mechanical properties and behavior of PEEK materials, which is of great significance for the design, selection and application of materials.
Elastic modulus is a measure of the degree of deformation of a material when it is stressed. It expresses the material’s ability to resist deformation within the elastic range. The elastic modulus of PEEK is usually higher, indicating that it has better rigidity and resistance to deformation.
Yield strength is the critical stress at which a material begins to plastically deform when it is subjected to a certain stress. The yield strength of PEEK is usually higher, indicating that it has better tensile strength and impact resistance.
Elongation is the percentage of elongation of a material during stretching. PEEK generally has a lower elongation, indicating better rigidity and impact resistance.
Plastic hardness is the ability of a plastic material’s surface to resist external forces. Common plastic hardness measurements include Rockwell hardness, Brinell hardness, and Vickers hardness. PEEK generally has a higher hardness, indicating better wear resistance and scratch resistance.
Some other mechanical specifications for pure, unfilled PEEK include:
PEEK (Polyetheretherketone) machining can be classified into several types based on different processing methods. Here are some common types of PEEK machining.
PEEK has excellent rigidity and toughness and can withstand high pressure and load. Its strength, stiffness and wear resistance make it suitable for a variety of demanding applications.
PEEK can maintain its mechanical properties and stability in high temperature environments without deforming or melting. This makes it an ideal material choice for high-temperature environments.
PEEK has excellent corrosion resistance to a variety of chemicals and solvents, and can resist the erosion of acids, alkalis, organic solvents and other substances. This makes it have broad application prospects in chemical industry, medical and other fields.
PEEK has good biocompatibility and will not cause adverse reactions to human tissues. Therefore, it is widely used in the medical field, such as manufacturing artificial joints, dental implants, etc.
PEEK can be formed through various processing methods such as injection molding, extrusion molding, CNC processing, etc., and has good processing performance. This makes it highly flexible and convenient in the manufacturing process.
PEEK has a high melting point, making it capable of melt processing. PEEK does not produce corrosive gases during injection molding and additive manufacturing, so it is safe to use. Additionally, PEEK’s high melting point also opens up possibilities for CNC machining, as fast-moving tools can cut PEEK without causing any melting.
PEEK can support complex designs and geometries through additive manufacturing. Additive manufacturing technology can create parts with complex structures and precise dimensions that may be difficult to achieve using traditional methods.
For the aerospace and automotive industries that have thermal efficiency requirements, lightweight is an important indicator. And PEEK can surpass the performance of many metal parts. Therefore, in recent years, there has been a strong trend of PEEK materials replacing metal parts in the aerospace and automotive fields.
PEEK (Polyetheretherketone) machining can be classified into several types based on different processing methods. Here are some common types of PEEK plastic machining.
Injection molding is one of the most common processing methods for PEEK materials. PEEK particles are melted by heating and pressure, and then injected into a mold for molding. This method is suitable for mass production and high performance plastic parts.
Compared with other plastic injection molding, PEEK injection molding needs to provide higher mold temperature, molding temperature, and stable process parameters. Usually the injection molding temperature of PEEK is 350 °C to 400 °C, and the mold temperature is 180-200°C. Pay attention to the mold design, so it is best to find a professional, professional and reliable injection molding manufacturer with experience in high-temperature plastic molding. It would be better if these details are effectively controlled at the beginning of mold design, so that unnecessary risks in production can be avoided.
According to our many years of experience, mold temperature plays an important role in PEEK injection molding and this type of high-temperature plastic molding. Lower mold temperatures can lead to the formation of amorphous structures in PEEK. The optimal mold operating temperature for most grades of PEEK plastic is between 180 °C to 200 °C to achieve a semi-crystalline structure.
During the PEEK compression molding process, PEEK powder or granules are mixed with an appropriate amount of plasticizer and then placed into the mold. The mold is heated to the appropriate temperature so that the PEEK material melts and fills the mold. Then, the mold is cooled and demoulded to obtain the desired PEEK product.
The advantages of using compression molding making PEEK include:
It should be noted that the compression molding process requires precise control of parameters such as temperature, pressure and time to ensure the quality and performance of the product. At the same time, selecting the appropriate mold and materials is also a key factor in the successful application of the compression molding process.
PEEK CNC machining is a precise manufacturing technology used to machine PEEK materials into the desired shape and size. CNC machining is a method of processing workpieces through cutting tools, and is suitable for the processing of PEEK materials. In milling, a milling or turning tool is used to remove material from a workpiece to obtain the desired shape and size.
In PEEK CNC machining process, high-precision machine tools and cutting tools are usually used to ensure the accuracy and consistency of the parts. The machining process includes cutting, drilling, milling, turning and other operations.
CNC machining of PEEK has many advantages, including high precision, high efficiency, high consistency, etc. Through precise CNC machining, parts with complex shapes and sizes can be manufactured to meet a variety of application needs.
It should be noted that PEEK is a high-temperature polymer, so the processing temperature and time need to be controlled during CNC processing to avoid affecting the material properties. In addition, appropriate tool and feed speed need to be selected to ensure processing quality and efficiency.
This method is suitable for the manufacturing of PEEK material pipes, rods, plates, films and other products. During the extrusion molding process, the PEEK material is heated to the appropriate temperature so that it melts. The molten PEEK material is then extruded through one or more extruder heads to form a continuous PEEK plastic product.
To ensure optimal performance and functionality of PEEK products, designers need to consider physical properties, mechanical loads and stresses, thermal stability, chemical resistance, and processing challenges. By working with an experienced injection molding manufacturer or machinist, the manufacturing process can be optimized to achieve the precision and surface finish required for PEEK polymer applications.
PEEK’s strength, stiffness and wear resistance make it ideal for many applications. Understanding the physical properties of PEEK, such as tensile strength, flexural strength, impact strength, etc., is critical to selecting the appropriate PEEK material to meet application requirements.
During the design process, it is important to consider the mechanical loads and stresses that the part will be subjected to during use. By optimizing design features such as part geometry, wall thickness, threads, and fillets, the strength, stiffness, and load-bearing capacity of the part can be enhanced. Avoid sharp corners or sudden changes in the cross-section to reduce stress concentration and improve the fatigue life of the parts.
PEEK has excellent thermal stability, but the operating temperature range of the application still needs to be considered. Components should be designed to withstand the expected thermal conditions. Also, given the effects of thermal expansion and contraction, additional cooling or insulation may be required to maintain part performance.
PEEK has broad chemical resistance, but may be affected by prolonged exposure to certain chemicals or high temperatures. It is important to evaluate the chemical environment the component will be exposed to and ensure it is compatible with PEEK’s chemical resistance. For specific applications, it may be necessary to select a specific PEEK grade or undergo special treatments to enhance its chemical resistance.
PEEK is a tough and wear-resistant material, but it also brings great processing challenges. High temperature and high pressure during injection molding, high cost of molds, tool selection, cutting speed and feed amount during CNC machining, etc. These all require planning ahead.
No matter what process is used to produce PEEK plastic parts, the cost of PEEK is very high compared to conventional processes. First, the material cost is quite high than regular thermoplastic, second, the processing cost will also be much higher. If the injection molding process is used, the mold cost also needs to be considered. But compared to the making cost, PEEK’s high durability is unmatched by other materials. In the long run, these high costs will be averaged out, and overall, it is still low cost.
PEEK is a plastic material used in harsh environments because of its unique and valuable properties. PEEK material has excellent performance and wide application fields, and can meet the needs of different fields. With the continuous advancement of science and technology and the expansion of application fields, the application prospects of PEEK materials will be broader. Here are some popular applications including:
PEEK plastic are widely used in the aerospace field. Due to its excellent high temperature resistance, mechanical strength and hardness, PEEK materials are used to manufacture aircraft and spacecraft parts, such as engine parts, structural parts, brackets, electrical connectors, cable insulation, fuel systems, etc. At the same time, PEEK material also has excellent flame retardant properties, which can ensure the safe operation of aerospace equipment.
In the automotive industry, PEEK are used to manufacture automotive parts, such as engine parts, seals, bearings, electrical connectors, fuel system components, piston components, etc. Due to its excellent wear resistance and mechanical strength, PEEK plastic can provide better durability and reliability, improving the performance and safety of automobiles. In addition, the lightweight advantage of PEEK is also an important reason why many metal parts are changed to PEEK plastic parts.
PEEK plastic are widely used in the field of electronic and electrical appliances. Due to its excellent electrical properties and electrical insulation properties, PEEK materials are used to manufacture electronic components, circuit boards, connectors, insulation materials, sockets, circuit boards, cable insulation, high-temperature wire coatings, etc. At the same time, PEEK material also has excellent high temperature resistance and mechanical strength, which can meet the high temperature working environment requirements of electronic equipment.
PEEK materials are widely used in the field of medical devices. Due to its non-toxic and biocompatibility characteristics, PEEK is used to manufacture medical device parts, such as artificial joints, dental implants, etc. At the same time, PEEK also has excellent wear resistance and mechanical strength, which can improve the service life and reliability of medical devices.
The applications of PEEK in the petrochemical industry include glands and seals, valve seats and pipe fittings, pump and compressor parts, chemical reactor linings, and catalyst support materials. Its excellent heat resistance, corrosion resistance and wear resistance are of great help in improving the efficiency and safety of petrochemical equipment.
The application of PEEK in the power industry covers insulation materials, connectors and connectors, insulators, switches and contacts, busbar clamps, cable sheaths and insulation layers, transformers and capacitors, etc. Its excellent thermal resistance, electrical properties and chemical resistance make PEEK an ideal choice for power equipment, helping to improve the performance and safety of power equipment.
Because PEEK doesn’t release harmful substances during food processing, it helps ensure food safety. In addition, PEEK also has low hygroscopicity, which helps prevent moisture absorption during food processing and maintain the taste of food.
PEEK, PEK and PTFE are all polymer materials, and they have some differences in performance and application.
PEEK (polyetheretherketone) is a semi-crystalline high-temperature thermoplastic with excellent high-temperature resistance, mechanical properties, chemical stability and electrical insulation properties. It is often used to manufacture parts that require high temperature and high pressure environments, such as in aerospace, automotive, and electronics. PEEK has high strength, high rigidity, good wear resistance, and is easy to process and manufacture.
PAK (polyketone) is a thermoplastic that, similar to PEEK, also has excellent high temperature resistance, mechanical properties and chemical stability. PAK has lower density and better processing properties, making it more suitable for applications that require lightweighting and ease of processing.
PTFE (polytetrafluoroethylene) is a fluoropolymer with excellent chemical resistance, low coefficient of friction and good electrical insulation properties. It is commonly used in the manufacture of seals, pipes, valves and other applications that require chemical resistance and low friction.
In general, these three polymer materials have their own characteristics in terms of performance and application, and which material to choose depends on the specific application needs and requirements.
Advantages and disadvantages of PEEK plastic
The properties of PEEK stem from its polyetheretherketone properties, which make it one of the materials of choice for many products with demanding requirements due to its durability and wide temperature range, especially its high temperature resistance. As the demand for higher mechanical properties and lighter weight continues to grow, so does the demand for this material from manufacturers. In many cases, PEEK polymer can actually serve as a metal replacement. Below we’ll explore some of the properties of PEEK that make it a versatile material suitable for a variety of applications. At the same time, we will also examine the shortcomings of this material.
PEEK can maintain its performance at very high continuous use temperatures, making it ideal for steam and high-pressure water environments. It remains dimensionally stable even at high temperatures and is resistant to thermal fatigue, allowing it to be heated, cooled and reheated repeatedly without degradation. It can be used continuously at temperatures up to 250°C. It can also operate in an environment of -70°C.
PEEK is resistant to dilute acids, alkalis and alcohols. The only solvents that can seriously corrode PEEK are concentrated nitric acid and concentrated sulfuric acid. It performs very well in salt water environments and has low water absorption, which helps maintain the dimensional stability of the seal.
PEEK has excellent wear resistance, providing a low-friction, hard surface that is very wear-resistant. It is not hard enough to damage metal surfaces with which it comes in contact, which is critical for rotary shaft seals and piston ring applications.
PEEK material has low density and light weight. It has a lower density, usually about 1/5 to 1/6 the weight of metal, making it an ideal choice for metal replacement in automotive and aerospace filed..
PEEK plastic material exhibits excellent properties in terms of strength, stiffness, creep and fatigue, making it ideal for manufacturing plastic parts with strict requirements on mechanical properties and dimensions. Over time, its performance will become more stable. In addition, PEEK also has excellent wear resistance and a low coefficient of friction in abrasive or wet environments, which helps extend the life of the part and maintain its integrity.
PEEK products have excellent hydrolysis resistance and will not hydrolyze even at high temperatures and in environments with water (whether fresh water, salt water or steam). This characteristic makes PEEK excellent in applications requiring high reliability.
PEEK exhibits excellent electrical properties over a wide temperature and frequency range. It is an excellent insulator and is widely used in the fields of electronics and electrical engineering, especially considering its heat resistance.
Since PEEK has low thermal conductivity, its thermal properties make it an excellent thermal insulation material. Combined with its mechanical properties and high temperature resistance, PEEK is ideal for applications requiring thermal stability.
PEEK is a fully recyclable material and halogen-free. This means it reduces environmental impact and meets sustainability requirements. In addition, PEEK polymer also complies with Europe’s RoHS directive and REACH regulations, proving its environmental compliance.
Properties can be changed by adding composite materials: The properties of PEEK can be changed by adding different composite materials according to needs.
The price of PEEK materials is relatively high relative to other thermoplastics, which may limit its use in applications where high volumes are required or where cost-effectiveness is a primary consideration.
Due to the high melting point of PEEK plastic, special equipment is usually required for processing and molding, such as high-temperature injection molding machines and mold temperature machines. This makes the machining process more complex and increases manufacturing costs.
PEEK material has poor melt fluidity, requiring higher injection pressure and longer injection time to ensure filling of the mold. This can lead to production inefficiencies and increased product defects.
PEEK material has a large shrinkage rate, especially at high temperatures. This may lead to product dimensional instability or defects such as shrinkage cavities.
PEEK material is sensitive to moisture and easily absorbs moisture and expands. Therefore, you need to pay attention to moisture-proof measures when using it in humid environments.
Long-term exposure to UV radiation can cause PEEK plastic to degrade, especially outdoors or in high-exposure environments. Degradation issues in PEEK polymers are often reduced by adding UV stabilizers
Although PEEK has good high temperature resistance, oxidation reactions are prone to occur at high temperatures. This oxidation reaction will cause an oxide film to form on the surface of PEEK, thereby reducing its physical properties and chemical stability.
PEEK may have more limited availability in some regions or markets than some of the more common thermoplastics. This may result in longer lead times and higher costs when sourcing PEEK components or materials.
PEEK has a limited range of color options compared to some other polymers, often only natural (light brown) or black available. This may be a consideration for applications that require color coding or aesthetic appearance. Therefore, when choosing PEEK as a material, you need to consider whether its color selection meets the application requirements.
Polyetheretherketone (PEEK) is a high-performance, expensive, semi-crystalline, high-temperature thermoplastic commonly used in demanding applications. Therefore, it is critical to conduct design for manufacturability (DFM) and work with a skilled injection molder to ensure that the part is manufactured successfully the first time.
Our professional team has extensive experience in various material types and manufacturing methods, especially injection molding of high performance plastics like PEEK, PFA, PPS, PEI, PAI, etc. If you have determined PEEK as the material for your project, please contact our engineers. They will help guide you through the entire process from drawings to prototyping and manufacturing. We are committed to providing you with the highest quality manufacturing services to ensure your project moves forward smoothly.
Attractive Plastics is a full-service injection molding partner that can manage your project throughout its entire lifecycle, especially with PEEK injection molding, for which we have unique experience. With full-service engineering and tooling knowledge and a wide range of value-added services, we provide a one-stop solution for all your plastic injection molding and high performance plastic molding needs. We look forward to hearing from you via the Contact Us page of our website to discuss your needs and how we can meet them.