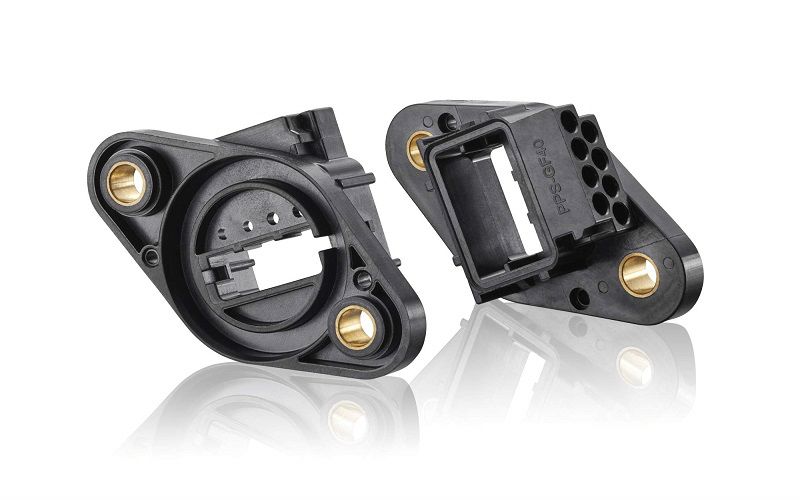
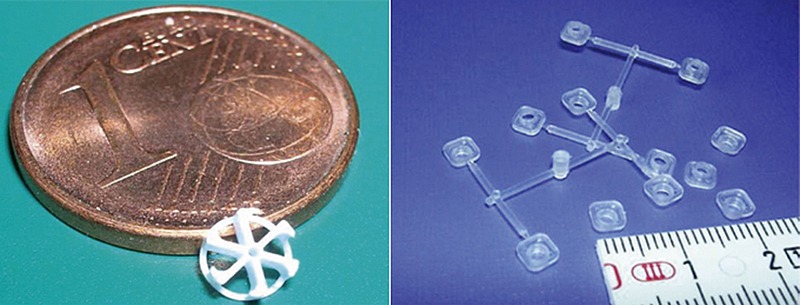
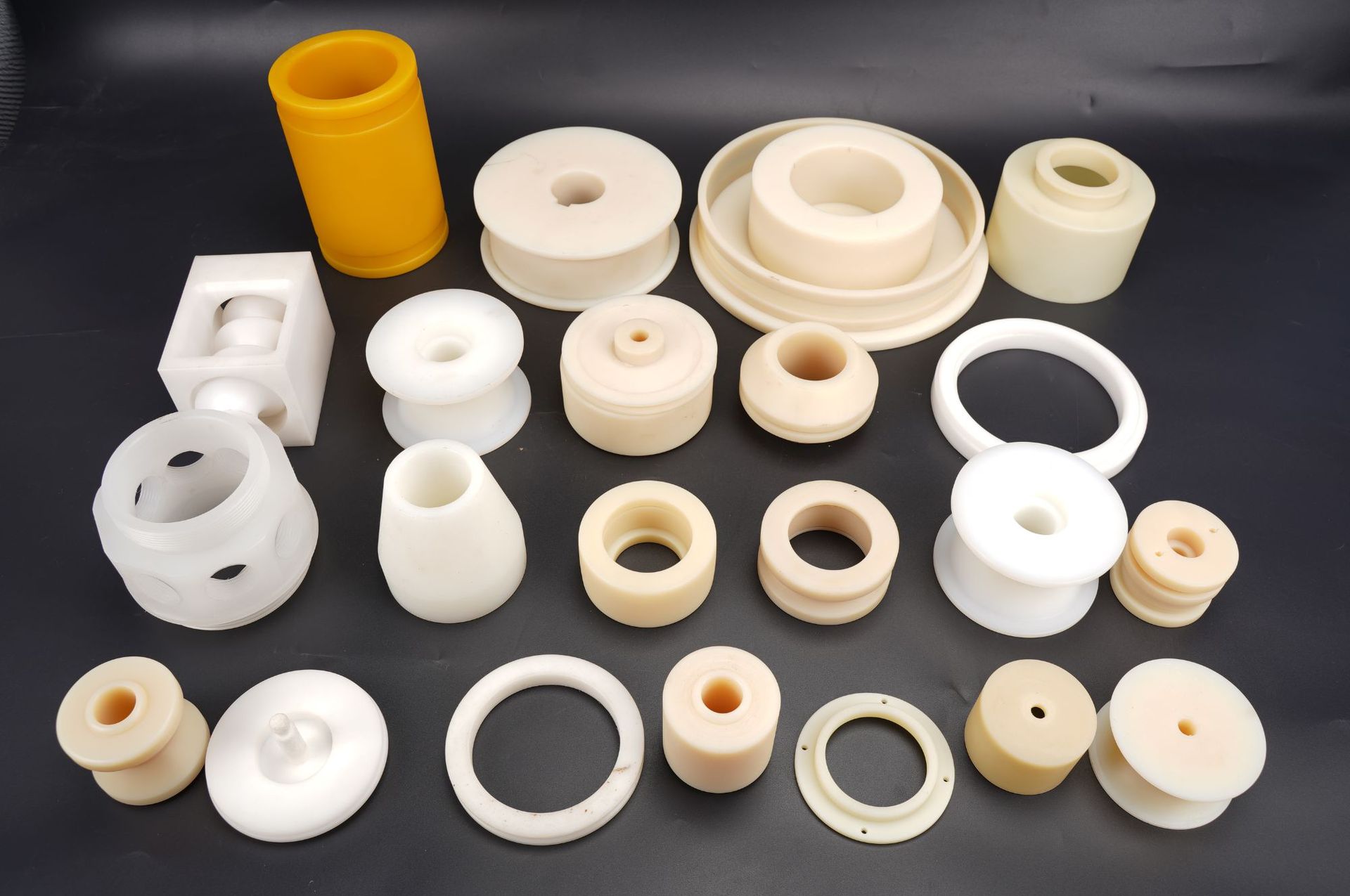
Magnets are critical components in many electronic devices and mechanical systems. However, the intrinsic fragility and environmental sensitivity of magnets limit their applications under certain conditions. Bare magnets are prone to damage from external environments like corrosion, impacts and abrasion. To protect magnets and improve their performance and reliability across various applications, overmolding technology was developed. Overmolding is a manufacturing process that encapsulates magnets within plastic materials, providing a robust casing while enhancing durability, insulation and water resistance.
This article will examine in depth the advantages of overmolding technology in magnet applications, and introduce common encapsulating materials and their characteristics. We will understand how overmolding shields magnets from external environmental influences, and improves performance and reliability in areas like motors, electronic devices, and medical equipment. Through an in-depth analysis of this critical manufacturing process, you will gain a better understanding of how to optimize magnet applications utilizing overmolding technology.
Overmolding magnets refers to the process of encapsulating magnets with plastic through injection molding. In this process, a plastic material is injected into a mold cavity that contains the magnet, and the plastic then solidifies around the magnet, creating a secure and protective encapsulation.
Overmolded magnets are an advanced manufacturing process that enhances magnetic performance and durability by completely encapsulating magnetic material with plastic. Here are the detailed steps of the overmolding magnets process:
Manufacturing or selecting a suitable magnet that can be any shape and size depending on the end product requirements.
This process typically requires two molds, with the first mold used to create a plastic part that can accommodate the magnet.
Inserting the prepared magnet component into the first molded plastic part.
Placing the entire assembled component into the second mold cavity, injecting more plastic that fuses with the plastic from the first molding to form a magnetically charged assembly encapsulated within plastic, with the magnet fully encased upon cooling.
After the two injection moldings are completed and the magnetic material is completely cooled, the entire product can be put into the magnetizing machine for charging and complete magnetization.
The magnets encased in plastic get good protection and can withstand harmful factors such as moisture, dust and corrosion in the environment. This helps extend the service life of magnets and prevents their performance from degrading due to environmental factors.
The plastic encapsulation layer provides extra mechanical strength, making the magnets more durable. Even under impact or vibration, the encapsulating layer can act as a buffer to reduce the possibility of damage to magnets.
Custom encapsulated magnets of specific shapes and sizes can be produced through mold design. This allows magnets to better adapt to different application scenarios and product structures to meet specific design requirements.
Encapsulated magnets can be more easily integrated with other components or assemblies. The plastic encapsulating layer provides a smooth surface and stable structure, allowing the magnets to be conveniently installed inside or outside the product.
For some applications that need to avoid direct contact with magnets, encapsulation can provide an extra layer of safety barrier to reduce the risks of accidental touching or swallowing.
In some cases, encapsulated magnets can integrate multiple manufacturing steps into one step, simplifying the production process and improving production efficiency.
Magnets are precisely placed and firmly locked in position by molded plastic without additional fasteners. No risk of detachment.
Provides an opportunity to integrate magnets within customizable plastic housings/casings for improved aesthetics and design flexibility.
Encapsulation bonds the magnet and plastic mechanically without extra adhesives or assembly steps.
The process molds magnets and casings in a single shot for high-volume production, more economical than multi-part assembly.
Properly encapsulated magnets perform consistently over long-term use without loss of magnetic strength or reliability issues.
The plastic forms a waterproof seal around magnets suitable for water-resistant applications.
The overmolding process for magnets involves many key factors that require a comprehensive consideration of material selection, mold design, molding process, magnet fixing and positioning as well as product performance testing. Through reasonable process design and strict production control, the quality and performance of overmolded magnet products can be ensured to achieve optimum states. Here are some of the key factors we have summarized based on our 10 years of experience encapsulating magnets.
1) Choosing the right magnet material
The magnet should have sufficient strength and heat tolerance range. Rare earth neodymium iron boride magnets are more heat resistant compared to ferrite magnets. The brittleness of magnets should also be considered – the magnet should be able to withstand the high pressure during injection molding without breaking.
The injection material should be compatible with the magnet in terms of chemical and physical properties to avoid adverse reactions. The selected plastic material should have good heat and chemical stability to withstand various environments. The bond between two overmolded plastics needs to be strong to fully encapsulate the magnet and prevent exposure, which could damage or weaken the magnet’s magnetism.
The mold design should consider the displacement of magnets caused by the flowing plastic. The plastic mold manufacturing need to be precise to ensure the final product dimensions and shape meet requirements. The mold should be designed accurately according to the shape and size of the magnet to ensure precise and complete encapsulation. Good venting channels can also improve the bonding performance of plastics during second molding and increase quality.
Differences in thermal expansion coefficients between magnets and plastics can cause deformation or cracking of parts. Carefully calculating the injection temperature and cooling rate helps alleviate stress, or preheating magnets before molding to reduce cracking probability.
Thoroughly clean the magnet surface to remove any impurities, oils or contaminants to ensure good bonding between the encapsulation layer and magnet.
Magnets can be demagnetized due to high temperatures during injection molding, although there are heat-resistant magnets, they are more expensive and brittle for many applications. Therefore, most overmolded and insert molded magnets are magnetized after molding. But if magnetized before molding, the temperature, molding cycle and duration should be strictly controlled to avoid seriously impacting magnet properties due to overheating.
The adhesion strength between encapsulating materials needs to be ensured to prevent magnet exposure due to poorly bonded areas. Whether materials can bond firmly during double molding is a key quality point.
Optimize molding processes to prevent bubbles in the encapsulation layer.
Thoroughly evaluate the impact of overmolded plastics on magnet magnetism to ensure no significant effect. The thicker the plastic covering the outer surface of the magnet, the weaker the magnetism; and vice versa, but molding becomes more difficult with thinner plastic. A balanced solution should be carefully considered.
Conduct comprehensive and rigorous quality inspections, including visual checks, dimensional measurements and performance testing. Production processes and products should perform excellently under various environments through physical testing and simulation.
Continuously improve and optimize overmolding processes to enhance production efficiency and product quality stability.
Use appropriate non-destructive testing methods to detect leaks and sealing performance to ensure long-term stability of magnets.
If magnets need to be assembled and disassembled, the mold design should ensure magnets can be safely and reliably removed, or a snap-fit structure is easy to assemble and disassemble.
The options for plastic integrated magnets include various different methods, each with their unique application scenarios and advantages. The most suitable process to fix the magnet needs to be selected based on a comprehensive consideration of the specific application requirements, product design and production conditions.
Ultrasonic welding is a method that uses high-frequency vibrational energy to connect plastic parts together. It is one of the ideal ways to fully encapsulate magnets. The magnet is placed between two plastic components, and then the plastic parts are welded together by an ultrasonic welding machine to fix the magnet. This method has the advantages of being efficient, fast and environmentally friendly, and is applicable to various thermoplastic materials.
Things to note: Ultrasonic welding requires plastic parts to have a certain weldability, and the position and size of the magnet need to be precisely controlled to ensure weld quality and magnet stability. And too large sound wave frequencies are easy to break the magnet.
Insert molding involves placing a prefabricated magnet insert into a plastic injection mold before injection of molten plastic. The flow of plastic encapsulates and locks the insert into the part. This provides protection for the magnet and bonds it rigidly to the plastic structure.
Things to note: Insert molding magnets require precise mold design and manufacturing to ensure positional stability of the magnet during the injection molding process. Unmagnetized magnets are easily displaced by high-speed flowing molten plastic. The difference in coefficient of thermal expansion between plastic and magnet may also cause stress cracking problems, which need to be considered in design and production.
Similar to insert molding, but overmolding involves injection molding an additional layer of plastic over an existing component to protect and fix the magnet. Thermoplastic elastomers (TPEs) are commonly used.
Snap fitting secures through designing matching snap structures on the two halves of a plastic component, allowing them to easily snap together to fix the magnet. This method is simple, easy to assemble and disassemble, suitable for applications requiring frequent magnet replacement or rapid assembly.
Things to note: The stability and reliability of snap fitting depends on the design and manufacturing precision of the plastic components. To ensure the magnet is firmly fastened, the snap structure and dimensions need to be carefully considered with sufficient testing and validation.
Screw or bolt fixing is a method of securing the magnet within a plastic component by pre-drilling holes and using screws or bolts. This method is suitable for applications requiring higher pulling or torsional forces, providing higher fixation strength and stability.
Things to note: When using screws or bolts, the hole precision and dimensions need to match the screws or bolts to prevent looseness or falling off. Non-magnetic hardware must be carefully selected. This provides a rigid bearing connection while protecting the magnet inside the housing. Additionally, the strength and durability of the plastic component to withstand stress and pressure from the screws or bolts need to be considered.
Melt rivets provide a secure attachment of the magnet using the plastic material itself. There is integral bonding between the magnet enclosure and rivets for a seamless assembly without additional parts.
High-frequency welding is a welding technique that utilizes induced heating from high-frequency currents within the workpieces to heat up and join metal, plastic parts together. Its working principle is that a high-frequency current is applied to generate resistive heat within the metal materials due to their electrical resistance, rapidly heating and melting the metals to form a welded joint. Magnets encapsulated using this process are commonly used in invisible buttons for the garment industry. Typically it uses two pieces of PVC to sandwich the magnet, and the encapsulating material can be PVC, PET or TPU. These sealed magnets are waterproof, aesthetically pleasing and fashionable.
Choosing a right encapsulating plastic material for magnets requires considering factors such as the magnet’s usage environment, performance requirements and cost. Through reasonable material selection and process design, the stability and reliability of encapsulated magnets can be ensured.
Thermoplastic elastomers (TPE) are materials that possess both the elasticity of rubber and the processability of plastics. TPE is often used for encapsulating magnets requiring a certain flexibility and durability due to its excellent elasticity, abrasion resistance and resistance to chemical corrosion. It can protect magnets from impact and abrasion while providing some elasticity to resist deformation, acting as a buffer for magnets and reducing the probability of magnet fragmentation during use from impacts and vibrations. TPE also has good weather resistance, allowing magnets to maintain performance and stability even in harsh environments. TPE is most commonly used for overmolded magnet materials.
Nylon is a strong, abrasion-resistant synthetic fiber material with outstanding mechanical strength and abrasion resistance. In magnet encapsulation, nylon is used due to its excellent physical properties. It can effectively protect magnets from external impacts and abrasion to extend magnet lifespan. Meanwhile, nylon also has good processability and can be easily processed into various shapes and sizes. Additionally, nylon’s high melting point means it can maintain structural integrity in high-temperature environments, which is crucial for long-term magnet stability.
ABS’s good weldability and stability make it the most suitable material for encapsulating magnets using ultrasonic welding technology. ABS is a common engineering plastic with good mechanical properties, impact resistance and chemical resistance to effectively protect internal magnets. Meanwhile, ABS also has some insulation properties to prevent magnets from short-circuiting due to contact with external metals.
Polycarbonate’s high impact strength and transparency make it a preferred material for magnet encapsulation, especially where magnet visibility is required to observe the internal magnet state.
Polycarbonate is a high-performance engineering plastic with outstanding heat resistance and high heat distortion temperature, enabling it to withstand adequate high temperatures around magnets. PC’s good heat and UV resistance also mean magnets can be used for long periods outdoors or in high temperatures without losing performance. Additionally, PC properties can be improved to meet various application scenarios by adding various additives and reinforcing agents.
Silicone rubber’s flexibility and temperature resistance make it an ideal material for encapsulating magnets, especially in environments with extreme temperature fluctuations. Silicone rubber’s electrical insulation and weather resistance also help protect magnets from external factors and maintain stable magnet performance. It can also provide some buffering to reduce impacts and vibrations on magnets during use. Meanwhile, silicone rubber’s good sealing properties can prevent magnet moisture absorption or contamination. here is rubber coated magnets water ball.
PTFE, or polytetrafluoroethylene, is an engineering plastic with outstanding properties including excellent corrosion resistance, high insulation, low friction coefficient and good heat resistance. It is mainly used for encapsulating magnets requiring high corrosion resistance and good electrical performance. PTFE can maintain stability under extreme temperatures and chemical environments, which is particularly important for magnet encapsulation operating in harsh conditions. PTFE can provide a sturdy, durable casing protecting internal magnet bearings from chemical corrosion while maintaining high temperatures. PTFE also has good insulation to prevent magnet short-circuiting due to contact with external metals. Additionally, PTFE can provide some lubricating effects, reducing abrasion on magnets during use.
Overmolded magnets improve durability and functionality by encapsulating magnets in a shock-absorbing casing, enabling them to withstand various complex working environments and enhancing overall performance and safety. As a result, overmolded magnets have widespread applications across multiple fields.
In the automotive industry, overmolded magnets are used in various sensors, motors, door locks, window lifts, dashboard components and wiper motors. For example, speed sensors in ABS systems and components in fuel injection systems. Overmolding can protect magnets from high temperatures, vibrations and chemical corrosion generated during vehicle operation, ensuring reliable performance under harsh environments and improving reliability and lifespan of automotive components.
Speakers and vibration motors in smartphones, tablets and wearable devices may use overmolded magnets. This encapsulation method prevents magnetic interference on electronic devices while also protecting the magnets themselves from damage caused by drops or everyday use.
Magnets also have applications in some consumer goods like toys and decorations. Overmolding can provide an aesthetic, durable casing for these magnets while also improving product safety.
Magnets can be used in diagnostic and therapeutic devices in medical equipment such as magnetic resonance imaging (MRI) machines. Overmolding provides biocompatible casings to ensure safety, reliability and stability of these magnets, and also improves durability while preventing interference from patient metallic objects.
Servomotors and stepper motors in industrial robots and automation equipment often use overmolded magnets. This encapsulation helps improve precision and response speed of equipment while reducing maintenance needs and extending equipment lifespan.
Overmolding magnets encapsulated by nylon or engineered plastics provides strength and insulation for motors in appliances like refrigerators, washing machines and air conditioners. This encapsulation can improve energy efficiency, reduce noise, and ensure magnet performance is unaffected in humid or dusty environments, achieving high reliability over the entire usage lifespan.
Overmolded magnets provide interactivity and fun in magnetic toys and games like magnetic puzzles and desktop games. This encapsulation ensures magnet safety, prevents accidental ingestion by children, and protects magnets from damage.
Precision instruments and equipment in aviation and aerospace domains like navigation and flight control systems may use overmolded magnets. This encapsulation helps ensure magnet stability and reliability under extreme environments (high altitude, low temperature, high radiation).
Overmolded magnetic circuits with thermoplastic elastomers or silicone provide strength while maintaining flexibility for speaker vibrations. This can improve sound quality and prevent moisture ingress.
Nylon or TPE encapsulated magnets provide handles, triggers or switches for tools that withstand heavy-duty use. Overmolding solidly locks magnets in position without degrading magnetic field properties.
Overmolded silicone or rubber magnets can form durable seals preventing fluid/particle ingress for applications like hydraulic cylinders, medical devices etc. The flexible material conforms tightly to sealed surfaces protecting anything entering internally corroding magnets.
Yes, Magnets can be molded. Injection molded magnets are produced through a process of mixing magnetic materials with polymer plastics and then injection molding to manufacture magnets of specific shapes and structures.
In the injection molding magnets process first selects a suitable magnetic material like ferrites, neodymium iron boron or ferromagnetic alloys. This material is then blended with resins, plastics or other encapsulating materials. The blend can be thermoplastic, thermosetting, silicone rubber or other flexible materials depending on application needs and required properties. Typically works with a wide-ranging combination of magnetic materials and polymers including: Nylon 6, nylon 12, PPS, PP, ferrite, NdFeB magnets, SmCo.
The magnetic blend is then placed into a mold and shaped through heating and/or applying pressure. In some cases a subsequent curing or heat treatment process may be required to ensure final material properties.
Molded magnets provide several advantages:
Improved durability: Encapsulating materials protect magnets from physical impacts, abrasion and corrosion.
Customizable shapes: Magnet shapes can be tailored for applications, making integration easier into product designs.
Environmental adaptability: Suitable encapsulants increase magnet performance in extreme temperatures, humidity or harsh environments.
Overmolding is a manufacturing process that involves injecting a thermoplastic material to mold onto or around another material. Materials commonly used for overmolding primarily include plastic materials, which can tightly bond with other plastic or metal components to form integrated structures. We summarize the most commonly used overmolding materials in actual production:
Thermoplastic plastics are best material for overmolding. Because of they can become soft after heating, are easy to molding, good adhesion, are low in cost, and return to hardness after cooling. Common ones include polyethylene (PE), polypropylene (PP), ABS, polyvinyl chloride (PVC), polycarbonate (PC) and nylon (Nylon).
Unlike thermoplastic plastics, thermosetting plastics maintain their shape after heating and curing and cannot be reversed. While their application in overmolding is relatively less, they may be used in specific cases where extremely high heat resistance or special electrical properties are required.
Silicone rubber has good flexibility, heat resistance and cold resistance, suitable for products requiring soft touch or special environmental durability. It is commonly used in medical devices, kitchenware and baby products.
Polyurethane is widely used in overmolding due to its excellent abrasion resistance, flexibility and impact resistance. It can provide hard or soft coatings commonly used in automotive parts, footwear and furniture.
Thermoplastic elastomers combine the processing performance of thermoplastics and the physical properties of rubber, providing good elasticity and durability. TPEs are commonly used in toys, sports gear and automotive interior components.
Epoxy resin has good adhesion and electrical insulation properties, suitable for applications requiring high strength and durability encapsulation. It is commonly used for encapsulation and protection of electronic components.
Overmolding technology effectively improves the performance and lifespan of magnets in various harsh working environments by providing suitable casing materials. It has become the preferred method for many product applications utilizing magnets. This process provides greater flexibility to the design of magnet components, enhancing the practicality and durability of magnets, allowing better integration into various products and expanding the requirements of many specialized applications.